Filament Maker TWO
The most advanced filament extrusion system, made in The Netherlands.
Build custom materials, test new polymers, or close your filament loop — all from a single, compact, lab-ready system.
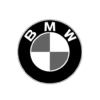
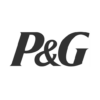
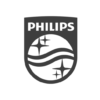
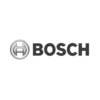

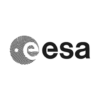
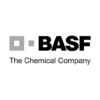
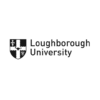
Create Custom Filament. Control Your Materials.
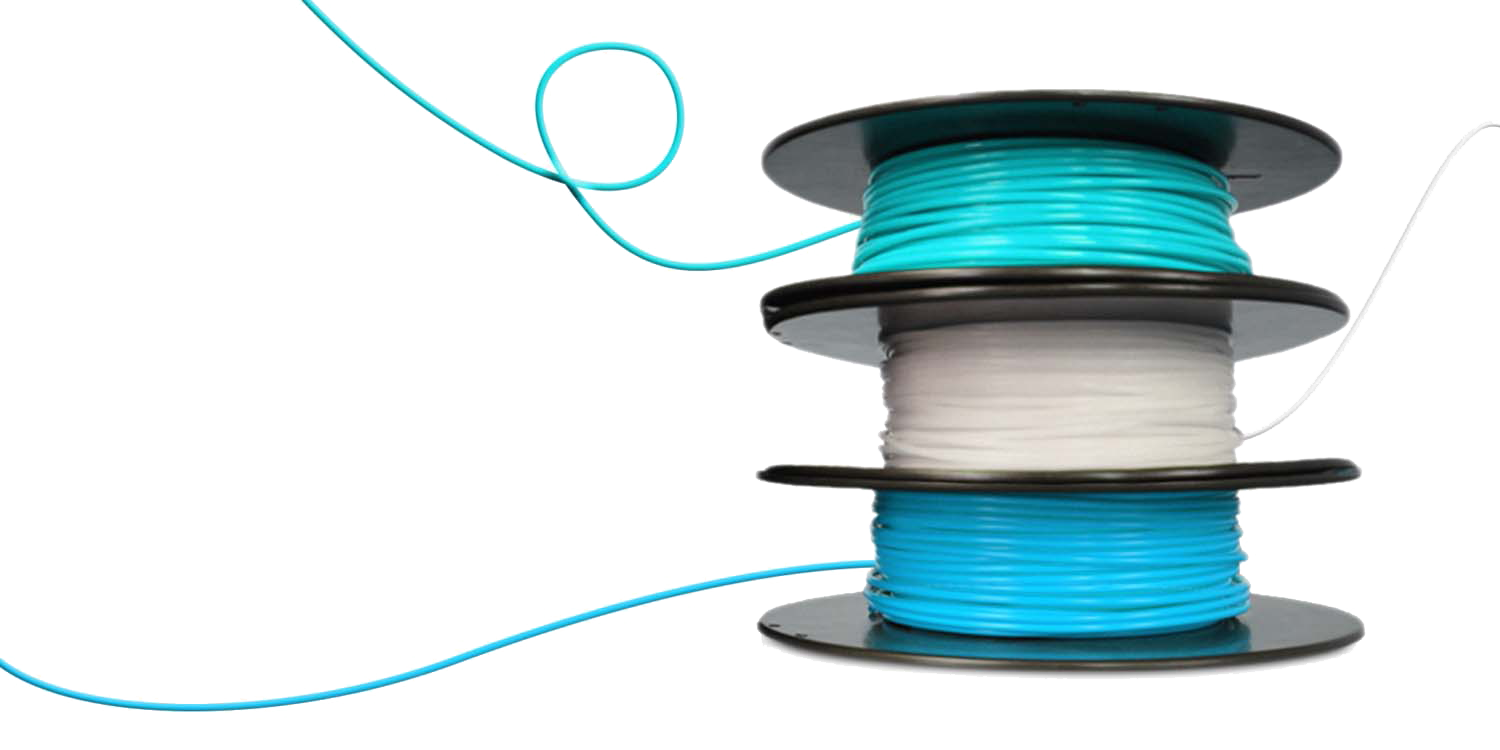
Shred it → Spool it → Print it

Designed For Professionals
Material R&D
Develop and test new polymer formulations in-house. Work with advanced composites like carbon or glass fiber, or validate materials like ABS, PETG, or PEEK.
Custom Filament Engineering
Create filament optimized for a specific function. Adjust properties, mix in additives or colorants, and fine-tune settings for functional prototyping and part validation.
Polymer Science Education
Bring real-world innovation into the classroom. Teach students about 3D printing, material science, and sustainability with tools designed for hands-on learning.
Recycle Plastic Waste
Close the loop in your R&D or production workflow. Repurpose support material, test prints, and process scrap into consistent input for future runs.
Hear From Our Customers
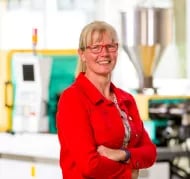
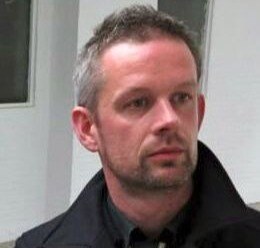
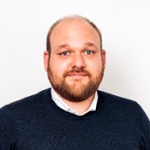
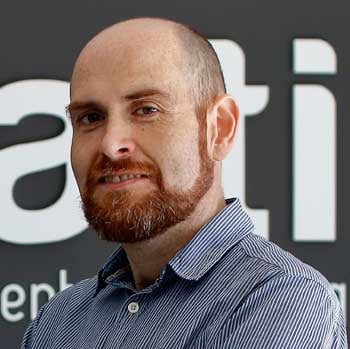
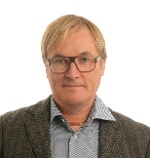
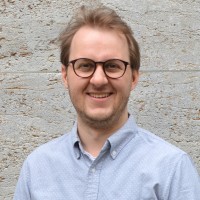
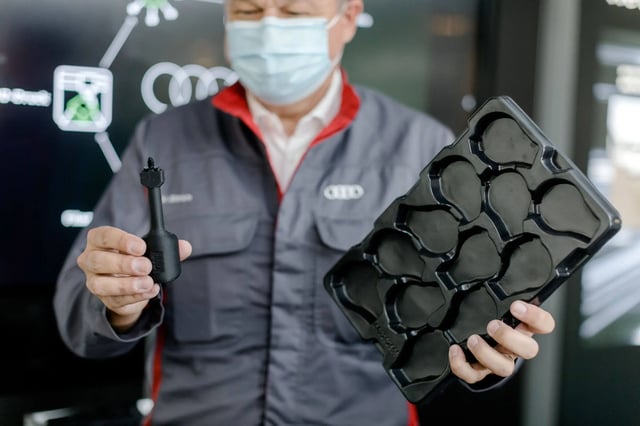