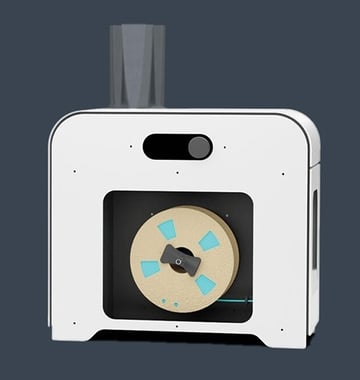
Filament Maker ONE
The original extrusion workhorse, trusted by innovators worldwide.
Trusted by professionals since 2016, Filament Maker ONE offers consistent, high-quality extrusion for material development and testing.
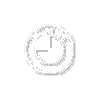
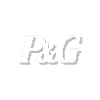
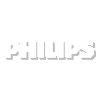
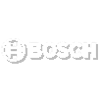
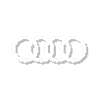
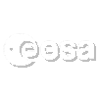
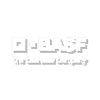
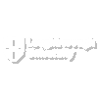
The Original Filament Maker
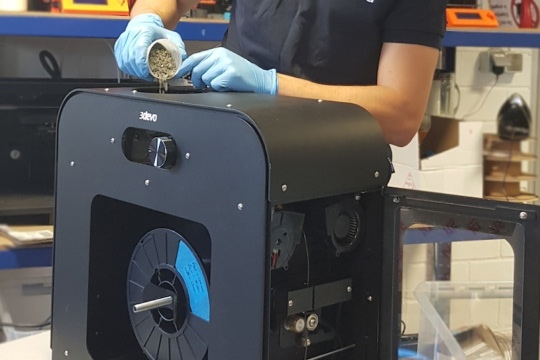
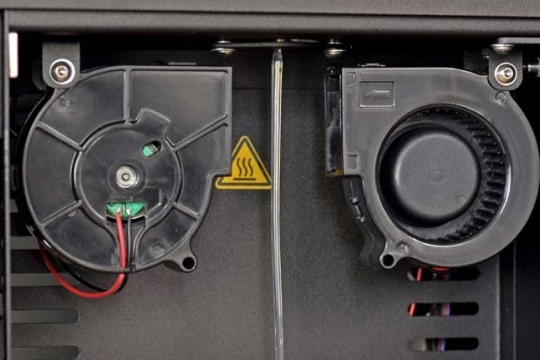
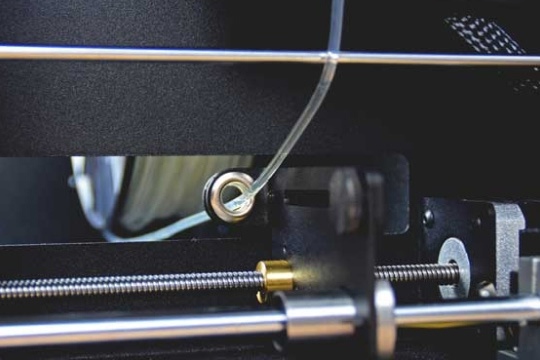
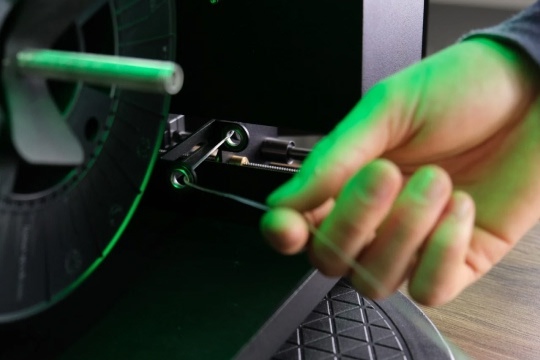
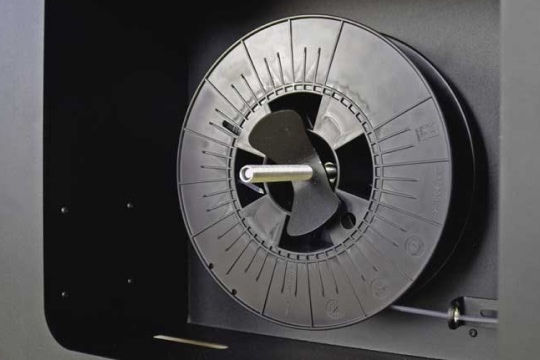
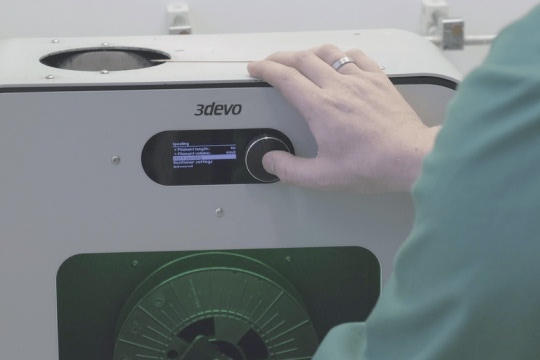
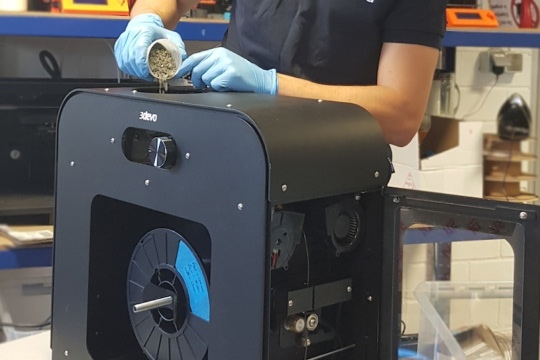
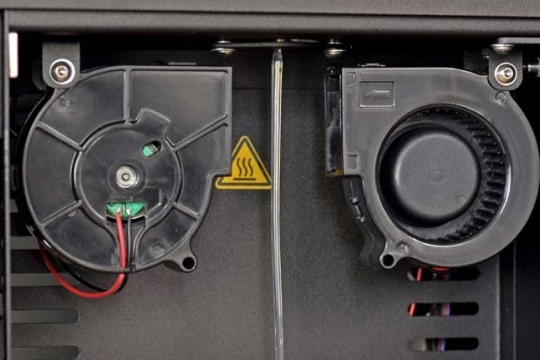
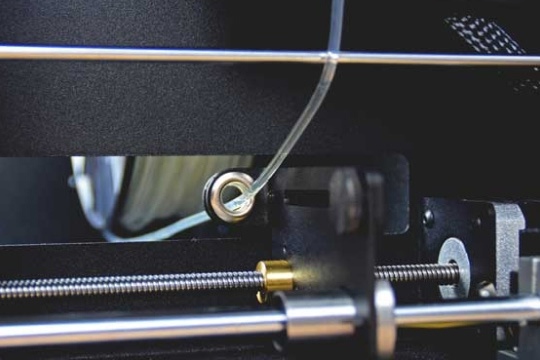
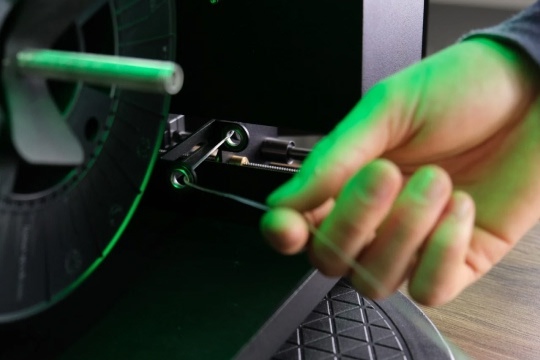
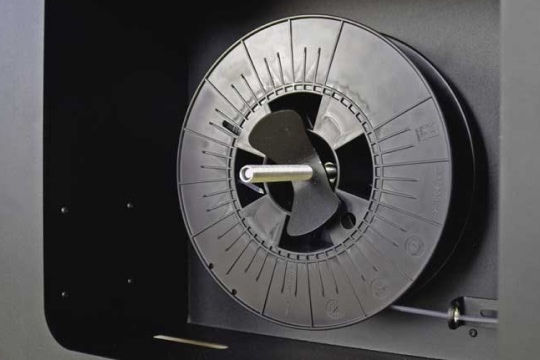
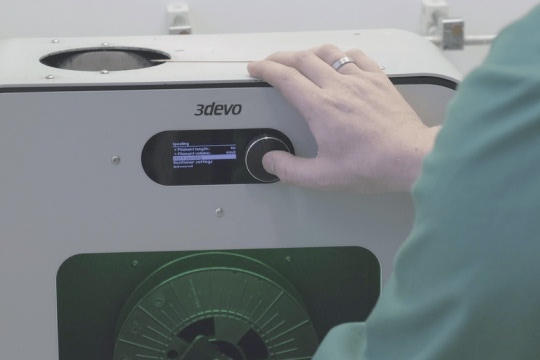
Key Features
High-Temperature Capacity
Precision Diameter Control
Durable Extruder Screw
Multi-Zone Heating
Flexible Start Modes
Material Mixing Option
An optional screw with a section for mixing materials enables the creation of custom filaments with unique properties.
Two Available Screws
Select the screw that fits your material needs:
- Composer Screw: Designed with an extended mixing zone to ensure thorough blending of additives, fillers, fibers, or colorants. The go-to choice for developing complex compounds or testing functional material formulations.
- Precision Screw: Built for high-throughput extrusion of standard or recycled polymers. Ideal for fast, stable filament production when processing pure materials or simple blends.
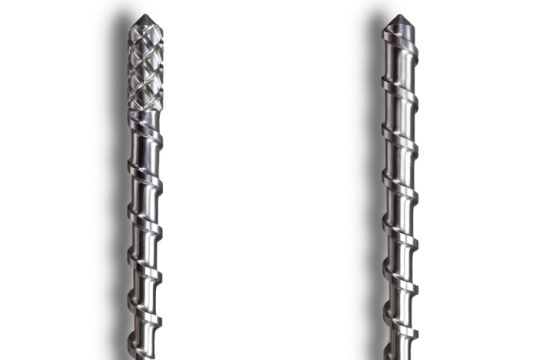
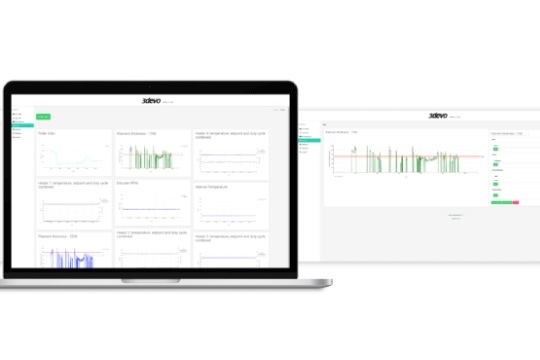
Comprehensive Data Monitoring
- Live Process Insights: Monitor key metrics like heater settings, filament thickness, and motor current in real time to maintain precise system control.
- Detailed Analytics: Track puller speed and screw RPM, all visualized in graphs, and easily export the data to Excel for further analysis.
- Optimize Performance: Leverage this comprehensive data to fine-tune your material settings, ensuring consistent, high-quality filament production.
Intuitive Control Panel
- Streamlined Interface: Navigate with ease through an OLED display and a simple rotate-and-push button.
- Quick-Set Profiles: Jumpstart your projects with standard material presets (PLA, ABS, PA12, PC, PEEK, and PS) or tailor custom profiles for unparalleled results.
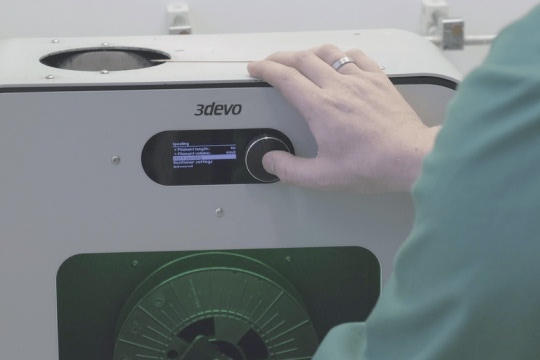
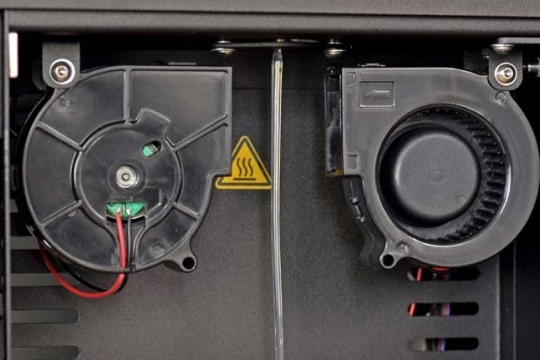
Precision and Quality
- Vertical Extrusion: Guarantees precise filament roundness and direct spooling, enhancing the quality of your 3D prints.
- Cutting-Edge Cooling and Spooling: Enhanced by a balanced dual fan system for even cooling and a precision spooling setup with an adjustable positioner and automatic spooling function
Optical Sensor and Puller
- Unparalleled Accuracy: The optical sensor measures filament diameter with 43-micron precision.
- Adaptive Puller System: Adjusts speed for consistent diameter control, with interchangeable wheels for various temperatures.
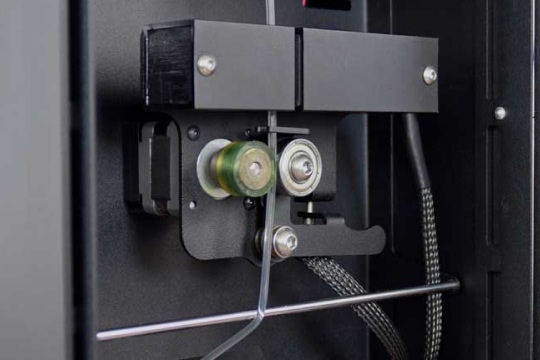
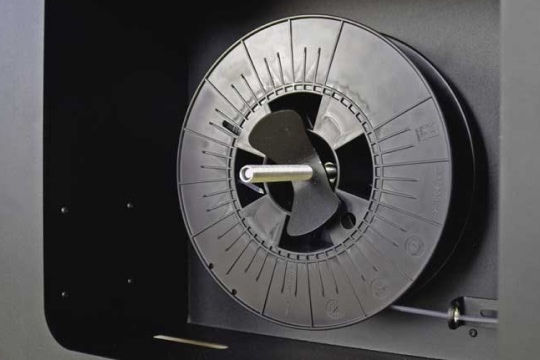
Automatic Spooling Mechanism
- Adaptable Spool Mount: Supports various spool sizes for flexibility in filament production.
- Customizable Spooling: Set specific dimensions for perfectly wound spools, while the built-in slipper clutch adjusts tension for smooth operation.
- Precision Spooling: Ensures tidy, tangle-free spools, supporting up to 240mm diameter and 120mm width.
Compatible Polymers
The Filament Maker ONE has proven its versatility and reliability over the years, effectively handling a broad spectrum of thermoplastics. This makes it ideal for numerous recycling and manufacturing applications. Here are some of the materials you can use with our extruder:
Common waste to recycle
PET | PLA | PP | HDPE |
PETG | ABS | PS | LDPE |
PC | PHB |
Engineering polymers
TPU | POM | PA6 | PVA |
TPE | PCL | PA66 | PA |
ASA | PA12 |
High performance polymers
PEEK | PEI | PSU |
PEKK | PPSU |
Additives and composites
Lattice Medical
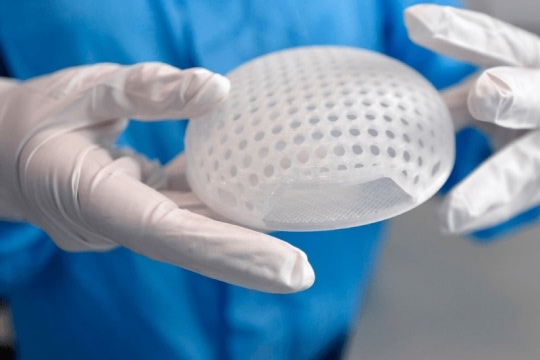
Pioneering Medical Advances
Lattice Medical
Revolutionizing Medical Procedures from Lattice Medical uses its patented 3D technology, Mattise, to revolutionize breast reconstruction, providing a more accessible and cost-effective solution.
AZ3D
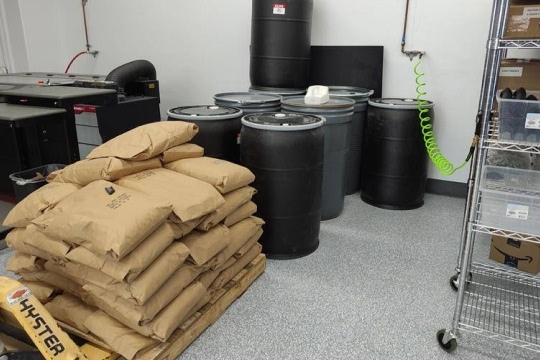
Recycling SLS/MJF Powder
AZ3D
Sustainable MJF Printing from
AZ3D, a Tucson-based prototype manufacturer, aimed to eco-friendly manage and repurpose their unusable nylon-based MJF material, by converting it into 3D printing filament.
Sika
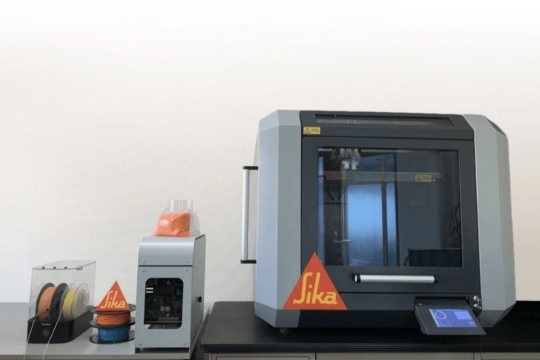
Processing Medium Melt Flow Index Polymers
Sika
Advanced Construction Solutions from
Sika leads in developing unique materials for modern construction using filament makers, streamlining production and quality assurance processes.
Specifications
PRODUCT SPECIFICATIONS
Band heater
Heating zones
Independent controls
450 series max temperature of 450 °C
Ceramic
4
Yes
Filament diameter range
Optical sensor accuracy
Nozzle extruder
0.5 - 3 mm (0.02 - 0.12 inches)
43 microns (1.69 mils)
Diameter 4 mm (0.16 inches) - Replaceable
Hardening treatment
Compression
Extruder design
Material mixing zone
Nitrided
3 stage
Swappable
Composer series ONLY
Consumption max.
Voltage
Frequency
1300 W
110 - 230 V
50 - 60 Hz
Spool holder
Spool size
1
Diameter 240 mm (9.4 inches)
Width 120 mm (4.7 inches)
Weight
19.2 x 8.5 x 17.6 inches
Extruder (Without box) 24.5 kg (54 lbs)
Extruder + box 27 kg (59.5 lbs)
Extrusion data analysis
Connectivity
DevoVision application
USB

Trusted by Innovators Since 2016
The Filament Maker ONE has earned its place in labs and research centers around the world. If you’re looking for a reliable, cost-effective way to start extruding, we’re here to help.