Share this
How To Start Extruding Carbon Fiber Filament
by 3devo on Mar 3, 2022 11:31:00 AM
Carbon fiber is set to take over the manufacturing industry, and the 3D printing sector is no exception. This paradigm shift is a result of the many advantages carbon fibers offer in their composites with polymeric materials. Adding short carbon fibers to polymers improves mechanical properties and reduces post-3D-printing woes like inter-layer temperature differences, warping and cracking. Moreover, filaments of short-carbon-fiber-reinforced polymers are easily printable with general purpose 3D printers without the need for specialized equipment.
At 3devo, we have experimented extensively with filaments extruded from short-carbon-fiber-reinforced polymer composites. In this article, we draw on our experiences to guide you on how to start your odyssey with carbon-fiber-based filaments, what to be mindful of, what challenges to expect, and how to resolve those challenges.
How to Start:
To extrude a filament that contains carbon fibers, you must start with selecting a matrix material (base polymer). You can browse through our material selection guide that we have prepared specifically to help you in this process. Keep in mind the requirements of your final printed object – mechanical strength, heat resistance, flexibility requirements, and so on. It also helps to be aware of any known challenges associated with the 3D printing of the selected polymer.
Finding the Right Extrusion Settings
Having chosen the base polymer and the size of the carbon fiber, you now need to optimize the extrusion settings. We recommend that you start extruding filament with just the base polymer, without adding any carbon fibers. This will help you to easily determine the optimal extrusion settings for your base polymer without wasting any carbon fibers.
Proceeding with Carbon Fiber
Once you find the perfect extrusion parameters for the base polymer, you can start adding carbon fibers in small amounts. Our recommendation is to use 1 w% carbon fibers in the beginning. Use this composite to determine the right extrusion parameters and then move on to higher carbon fiber concentrations.
As you move on, we recommend that you keep increasing the amount of carbon fiber in increments of 5 w%. Increasing carbon fiber content in small steps as opposed to large jumps allows for finetuning of parameters. This is particularly important because the relationship between carbon fiber content and filament features (diameter, extrusion rate, or mechanical strength) is not always linear. For example, very high carbon fiber content increases the chances of void formation in the filament, compromising its mechanical integrity.
Cross section of carbon fiber filament with 5w% and 1w%
Challenges to Prepare for:
Extruding short-carbon-fiber-reinforced polymers into filament can be challenging when you enter the process without prior experience. Using our experiences, we have summarized the challenges associated with extruding short-carbon-fiber-reinforced polymers, and how you can overcome them.
Sifting Segregation
Sifting segregation occurs when there is a large difference between the particle sizes of the materials in a mixture. We are using carbon fibers in the 100 µm size range, while polymer pellets are typically larger than 5 mm.5 So, there is at least a 50-fold size difference between the two particles we are mixing. In such cases, the smaller particles (carbon fibers) can move through the voids between the larger particles (polymer pellets) and segregate. We have shown this in the figure below.
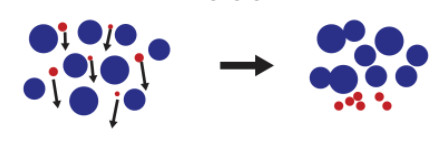
Segregation of particles means that the starting material for the filament is not mixed homogeneously inside the filament maker’s hopper. As such, the carbon fibers will not be evenly distributed along the length of the resulting filament. We recommend two techniques to prevent this from happening. Firstly, you should restrict the amount of starting material you put in the hopper. Consequently, the material will spend lesser time in the hopper and not have enough time to sieve through the pellets. Secondly, you should use opt for a smaller particle size. This will reduce the void space between the particles, preventing the carbon fibers from moving through and segregating.
Filament Stretching and Nozzle Clogging
When using high carbon fiber content, you may encounter an issue when the material is leaving the filament maker’s nozzle. The most used nozzle in filament makers is 4mm in size. This means that the resulting filament is also 4 mm thick when it leaves the nozzle. Thus, the filament has to be stretched using puller wheels to get it to the desired thickness, as diagrammed below.
Higher carbon fiber content hinders this stretching of the filament material since the fibers do not stretch with the polymer. In this situation, the material tends to break between the nozzle and the puller wheels. One way out of this is to use a nozzle with a smaller diameter. This will reduce the extent to which the filament has to stretch to get to the desired diameter.
On the other hand, working with a smaller nozzle increases the risk of clogging. Remember to monitor the extruder current and take predictive measurements in case the filament maker shows any signs of nozzle-clogging.
Brittle Filament
Another issue we encountered during our early experiments with extrusion of short-carbon-fiber-reinforced filaments was the formation of small gaps. These gaps (or voids), visible in the photograph below, make the filament brittle. We figured out that these voids were due to moisture present on the surface of the carbon fibers. Drying the fibers before using them reduced the formation of these voids and the extruded filament was no longer brittle.
Leverage Our Experiences
At 3devo, we regularly experiment with old and new filament materials and thoroughly document our results. Our experiences with extruding filaments of short-carbon-fiber-reinforced polymers have equipped us to guide you through your own experiments with them. We hope that the steps, challenges and solutions we have discussed above will help you work with this fantastic (yet somewhat challenging) material.
Share this
- March 2025 (1)
- January 2025 (1)
- December 2024 (2)
- November 2024 (3)
- October 2024 (4)
- September 2024 (2)
- August 2024 (3)
- July 2024 (6)
- June 2024 (3)
- May 2024 (2)
- April 2024 (1)
- March 2024 (1)
- January 2024 (1)
- November 2023 (2)
- October 2023 (5)
- September 2023 (2)
- August 2023 (1)
- July 2023 (1)
- May 2023 (1)
- December 2022 (3)
- August 2022 (1)
- June 2022 (1)
- May 2022 (2)
- April 2022 (2)
- March 2022 (7)
- February 2022 (2)
- January 2022 (3)
- December 2021 (3)
- November 2021 (3)
- October 2021 (2)
- September 2021 (3)
- August 2021 (3)
- July 2021 (2)
- June 2021 (1)
- March 2021 (1)
- October 2020 (1)
- June 2020 (1)
- May 2020 (1)
- April 2020 (4)
- November 2019 (1)
- July 2019 (2)
- June 2019 (1)
- May 2019 (1)
- March 2019 (1)
- November 2018 (1)
- September 2018 (1)
- January 2018 (1)
- October 2017 (1)
- September 2017 (1)
- July 2017 (1)
- June 2017 (1)
- May 2017 (1)
- January 2017 (1)
- December 2016 (3)
- November 2016 (2)
- October 2016 (1)
- May 2016 (2)
- August 2015 (2)
- July 2015 (1)