Share this
MFI Testing Series: Understanding how MFI influences your filament extrusion
by Ellie Pritchard on May 7, 2024 11:57:28 AM
Introduction
As part of our MFI Testing Series, the following article details the ways in which a Melt Flow Index (MFI) test can bring clarity to how a material may respond in the filament extrusion process. Here, one of 3devo’s very own R&D Materials Specialists, Janus Barnard, shares expert insights from his wealth of materials science knowledge and his experience conducting MFI tests. Janus takes you through the various factors that can influence MFI results, the importance of accuracy when setting up the test and conducting the procedure, and what the MFI result can mean for the extrusion process and final filament.
The MFI test is just one of our Validation Services available to assess the success rate of your filament extrusion project. We also offer expert consultations with our Materials Specialist team, a comprehensive Filament Development Analysis, and various workshops, all designed to ensure a risk-free process and give autonomy to you and your teams. We encourage you to discuss the Validation Services with your Materials Specialist in your initial 15-minute consultation call.
And now let’s hand over to Janus, as he explains the value of the material test.
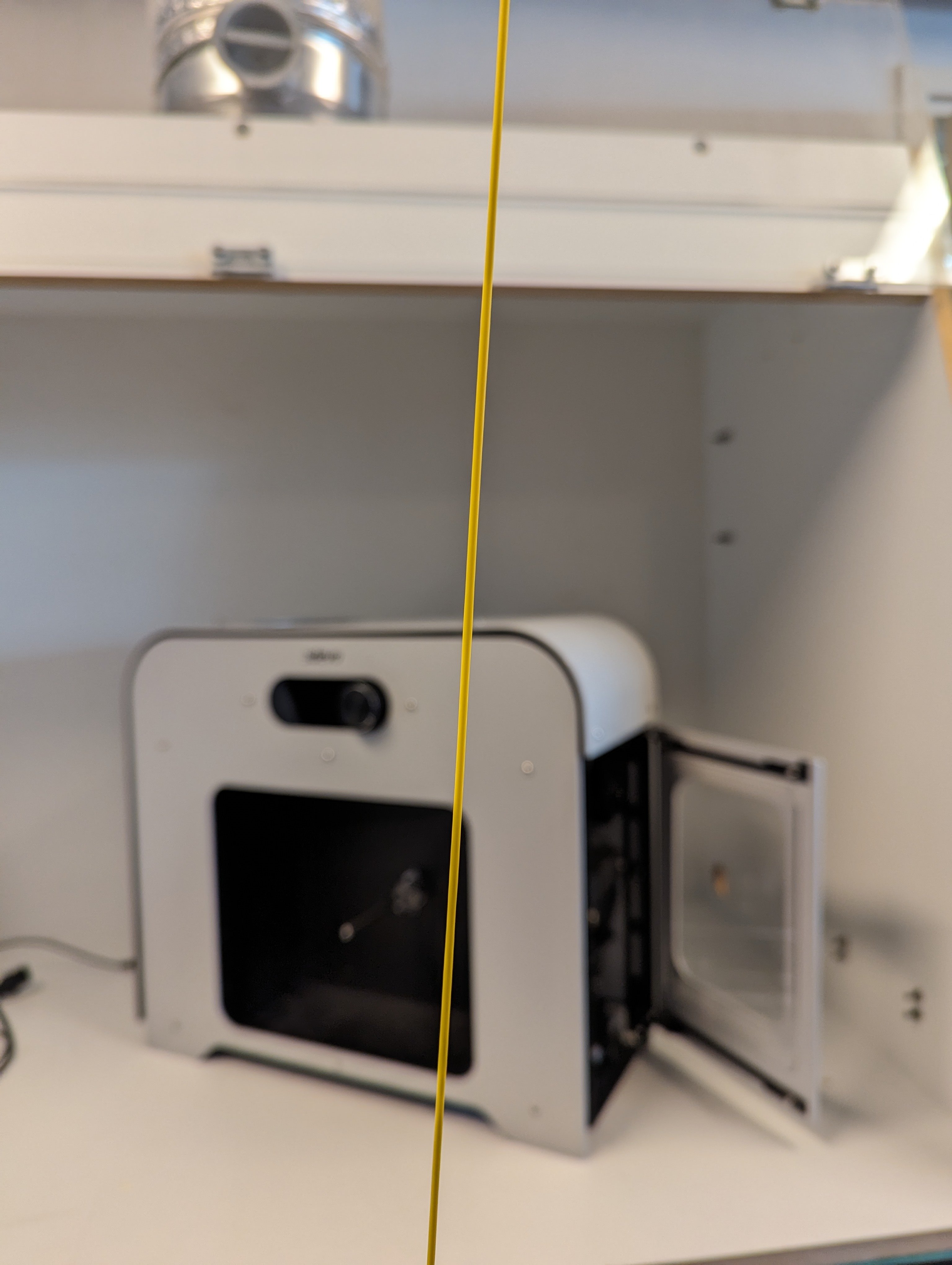
The Value of an MFI test
The purpose of an MFI test is to determine what the flowability is of your material at a given temperature. It’s a safe way to understand whether your material is fit for extrusion or if it’s rather meant for injection moulding. You can find out more about this on our post about MFI testing here. [1] What it essentially comes down to is that if your material consists of an MFI lower than 10 g/min it is usually perfect for extrusion. Materials in this MFI range produce more stable filament and are much easier to work with. If the MFI is too high, the material has a low viscosity and is therefore too liquid to work with. This type of material is generally used for injection moulding where a low viscosity is favoured in order to completely fill the mould. On the other hand, if the MFI is too low (< 1 g/min) the material is very stiff and too rigid to work with on the extruder and is more suited for blow moulding where a more rigid melt viscosity is critical. [2] Some materials, such as thermosets or crosslinked materials do not flow when melted and can therefore not be considered for FDM printing. [3]
Temperature Influence on MFI Readings
It is widely understood that the viscosity of a material varies with temperature. However, what might not be so obvious is that material viscosity changes at different rates with varying temperature. This is a crucial parameter and has a great impact on the processing window in which we can work. The processing window is the range of temperatures at which the material has the desired MFI for our goals. We would ideally like to work within this processing window to get the results we need.
The figure below illustrates this phenomenon. If a material’s MFI changes gradually over a wide temperature range, it has a wide processing window which means that it will be more forgiving when trying to extrude it. Conversely, if the MFI changes abruptly the material will instantly transition from a state of no flow to a state of high flow and can therefore prove more difficult to work with. Conducting an MFI test is therefore extremely helpful in order to know into which category your material falls and how careful you ought to be when selecting the temperatures on your extruder.
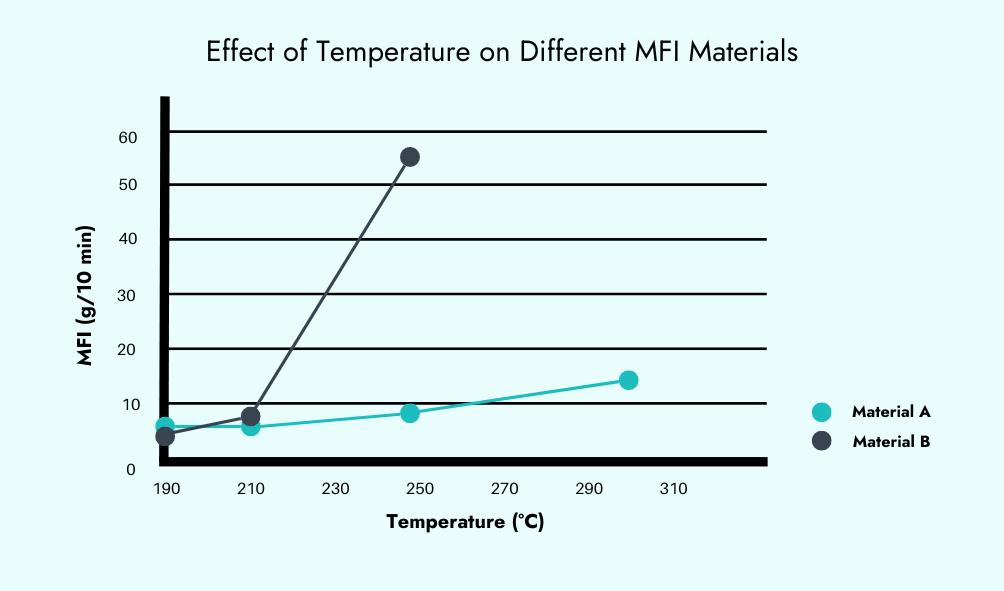
The Influence of Load on MFI Readings
Quite simply, by using higher loads in the test you get more material to flow. Similarly, higher screw loads will result in more material flow. This can be seen in the figure below where the same material was tested at different temperatures with a 2.16 and 10 kg weight respectively.
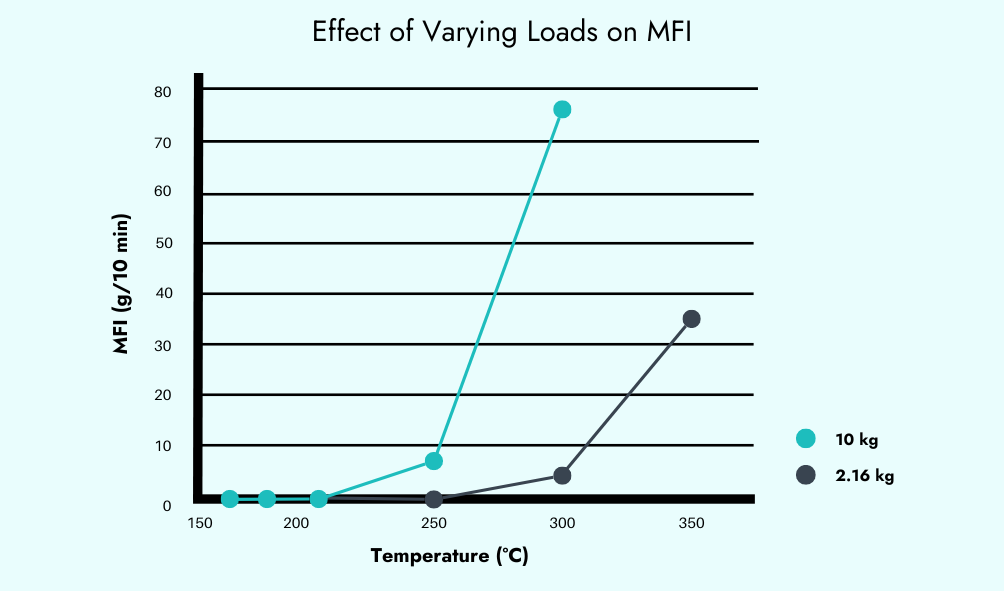
It is important to remember that the flowrate is only a representation of how the material behaves under these conditions. We are primarily interested in how the material behaves after it exits the die, so the load itself is therefore not as important to us as the temperatures. In the Filament Maker we need the material to cool down to a workable temperature and thus a workable consistency. MFI testing should therefore just be used as a gauge to try and predict how the material will behave in the filament making process. The following points will focus on how we can achieve that.
“MFI testing should [...] be used as a gauge to try and predict how the material will behave in the filament making process.”
Janus Barnard - 3devo R&D Materials Specialist
The Importance of Precision and Accuracy in MFI Testing
Before extrusion starts, it is highly important to gather as much information about the material as possible. MFI is a great tool for this purpose and can tell us a lot, not only about the material type of material but also about its state. Gauging the flow characteristics of the material can be very helpful to predict flowability within the extruder which could help to reduce any frustrations further along in the process. The type of material is assessed by how accurately the material falls within a given MFI range and the state of the material can be related to how precise these measurements are. The figure below illustrates this using four different scenarios. Example A resembles a material that is not accurate or precise, it does not fall within the targeted MFI range and the deviation between measurements is high. A bad extrusion result can be expected for this type of material and no amount of hardware manipulation can resolve this. This type of behaviour could be due to various factors and can quickly become quite complex. Some examples of this situation could include a blend of material that was used with varying MFI values or recycled polymer that has been degraded. Example B shows the situation where a material has a consistent/precise MFI, but the MFI is in the injection moulding range. This could be an example of a virgin grade of injection moulding material. Example C could be good for extrusion as it is in the lower MFI range but the variation in precision could result in a fluctuating filament diameter. Example D would be the ideal example of a virgin polymer that was synthesized for the purpose of extrusion. A good filament can be expected with a low filament diameter.
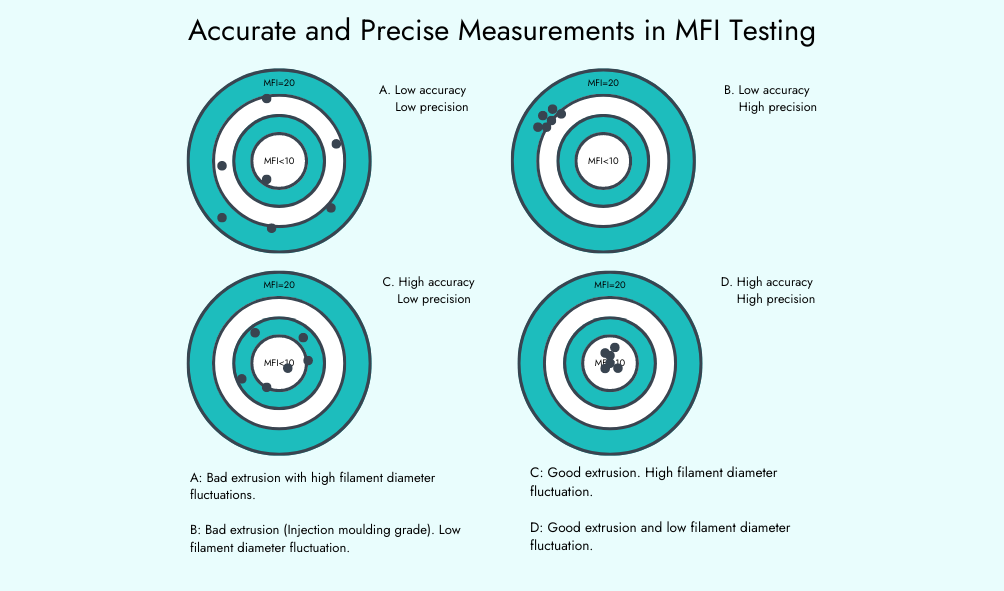
A low standard deviation in the measurements of MFI will ensure consistency in the flow and therefore the filament properties such as filament diameter. The more accurate and precise the MFI values that can be obtained from an MFI test, the more successful your filament extrusion will be. If you start outside of these parameters, you will be guaranteed a tough, but not impossible time on any Filament Maker or 3D printer.
What Are the Influential Factors for the MFI
To understand what factors influence the MFI, we should understand to which material property it relates. It is well known that the molecular weight (MW) and molecular weight distribution (MWD) are related to a material’s viscosity and in turn to its MFI. Generally, a higher MW means a higher viscosity and therefore a low MFI reading. The opposite is true for low MW material. [4]
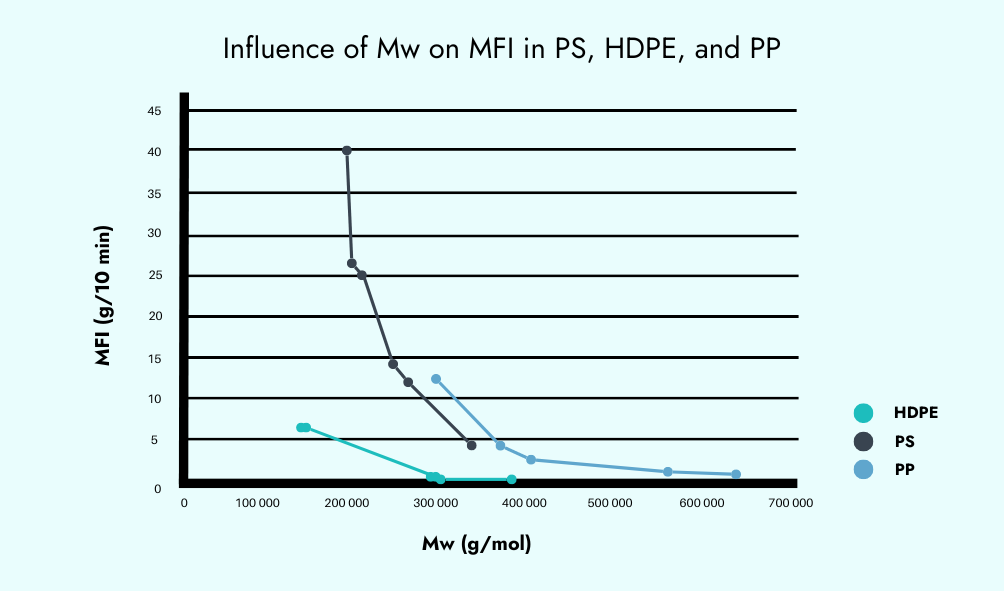
MW weight is dependent on the processing conditions used to synthesize the material. A virgin grade of material with tightly controlled processing parameters usually consists of a precise MW and narrow MWD. The MFI of these virgin material is therefore also very precise. One factor that can influence MW after production is degradation, which is one of the main causes of a decreased MW. There are several types of polymer degradation, each influenced by factors such as exposure to heat, light, oxygen, mechanical stress, and chemical substances. Additionally, degraded material will show an increase in MWD as the process of degradation is random and will therefore lead to a random dispersion in the length of chain segments. An increased MWD will decrease the precision of the MFI testing result and therefore ultimately lead to variations in filament diameter. Two of the main types of degradation that we come across is thermomechanical and hydrolysis. Thermomechanical degradation is due to over-recycled polymers which are continually exposed to the harsh processing conditions such as high temperatures and friction experienced during extrusion. Hydrolysed material is due to improper drying of hygroscopic materials such as PLA or Nylon. Luckily, there exists a few ways to narrow the MWD of recycled material back down to a reasonable range. The first of which is by incorporating more of the virgin material into the blend and, secondly, by introducing additives such as heat stabilizers or antioxidants which will prevent degradation in the recycling process or during the product lifetime. When incorporating virgin materials into blends the material should also be compatible and consist of a similar MFI. Emphasis should also be put on how MFI testing can be of value for the recycling industry. It is a fantastic way of gauging how much your material has degraded over its lifetime or if it is properly dried. [5]
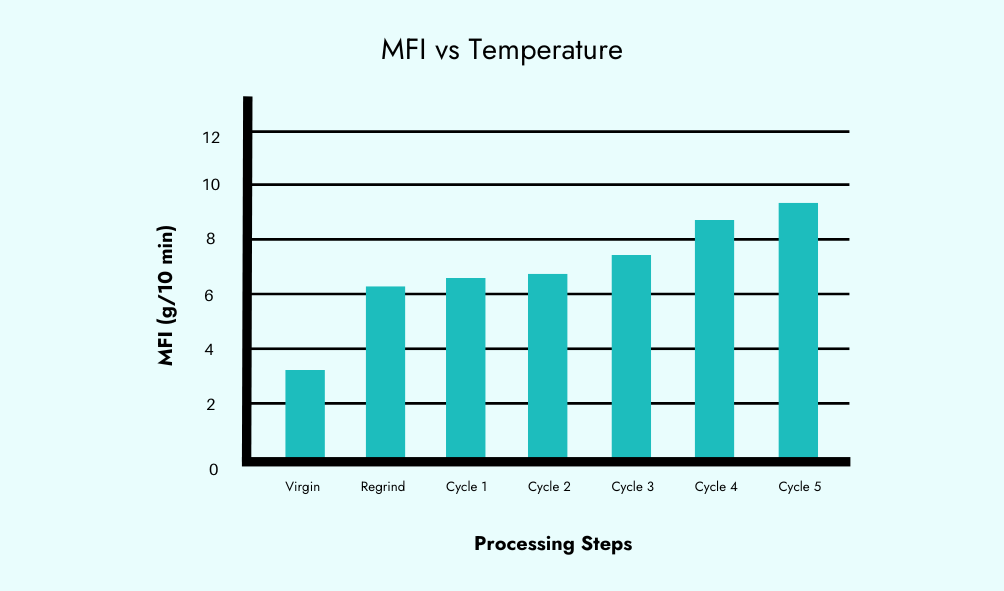
There are also ways to increase the molecular weight of a polymer in order to achieve a lower MFI or to renew the “health” of your recycled material. Examples of these include chemically binding the chains using crosslinker or extending the chain length using chain extenders. The amount by which the MFI is increased will be dependent on the type and concentration of additive used. [7] [8] Another way to manipulate the material viscosity is to incorporate fillers, the effect is depending on the size, shape, and concentration thereof. [9] Another key insight that MFI testing can give here is whether additives are homogeneously dispersed throughout the polymer matrix, as heterogeneous dispersions will lead to MFI discrepancies. One way that we can gauge this is by comparing the MFI of neat materials to that of the compounded ones.
In extreme cases, the material does not flow at all which is obviously detrimental for 3D printing. Moreover, these materials can also cause serious damage to the MFI instrument and Filament Makers. Materials which do not flow or that show very small MFI readings are materials that are crosslinked, thermoset or have filler loadings that are simply too high. Thermoset materials are a type of polymer that undergo irreversible chemical reactions, typically through crosslinking, when heated. Once they are set, they cannot be reshaped by heating. They have zero to low MFI values and can therefore not be considered for FDM printing. These materials can however be 3D printed using other processes available such as digital light process (DLP), stereolithography (SLA), and direct sound printing (DSP). [10]
Conclusion
In conclusion, understanding how the MFI influences filament extrusion is crucial for achieving successful 3D printing outcomes. The MFI test serves as a valuable tool for determining the flowability of a material at specific temperatures, guiding the selection of suitable processing conditions for extrusion. By assessing the MFI values, we can identify the optimal processing window for materials, ensuring consistent flow behaviour and filament properties. Additionally, the precision and accuracy of MFI testing play a significant role in predicting filament extrusion performance, highlighting the importance of gathering detailed information about the material's flow characteristics. Factors such as molecular weight, degradation, and additives can influence the MFI values, underscoring the need for thorough understanding and control of material properties. Ultimately, leveraging MFI testing effectively can lead to improved efficiency, quality, and reliability in filament extrusion processes, advancing the capabilities of 3D printing technology.
Reference List
[1] |
E. Pritchard, “MFI Testing: A key validation step for novel filament extrusion,” 18 March 2024. [Online]. Available: https://www.3devo.com/blog/mfi-testing-a-key-validation-step-for-novel-filament-extrusion. |
[2] |
F. Cogswell, “Chapter Two - Rheometry for Polymer Melts,” in Polymer Melt Rheology: A Guide for Industrial Practice, Sawston, UK, Woodhead, 2003, pp. 15-38. |
[3] |
R. B. Kristiawan, “A review on the fused deposition modeling (FDM) 3D printing: Filament processing, materials, and printing parameters,” Open Engineering, vol. 11, pp. 639-649, 2021. |
[4] |
T. BREMNER and A. RUDIN, “Melt Flow Index Values and Molecular Weight,” Journal of Applied Polymer Science, Vol. 41, 1617-1627 (1990), vol. 41, pp. 1617-1627, 1990. |
[5] |
L. M. M. M. R. Tanyaradzwa S. Muzata, “Challenges in the mechanical recycling and upcycling of mixed postconsumer recovered plastics (PCR): A review,” Current Research in Green and Sustainable Chemistry, vol. 8, p. 100407, 2024. |
[6] |
C. Aumnate, “Recycling of PP/LDPE Blend: Miscibility, Thermal Properties, Rheological Behavior and Crystal Structure,” in SPE ANTEC, Indianapolis, 2016. |
[7] |
M. Zhang, “Recent Advances in Environmentally Friendly Dual-crosslinking Polymer Networks,” Angewandte Chemie, vol. 1, pp. 12-15, 2024. |
[8] |
J. Mestry, “Superior glycidol-free chain extenders for post-consumer PET bottles and PET thermoform blends,” Resources, Conservation and Recycling, vol. 203, p. 107420, 2024. |
[9] |
J. Xu, “Mechanical properties, morphology, and creep resistance of ultra-highly filled bamboo fiber/polypropylene composites: Effects of filler content and melt flow index of polypropylene,” Elsevier, vol. 310, p. 125289, 2021. |
[10] |
Y. Sun, “3D printing of thermosets with diverse rheological and functional applicabilities,” Nature Communications, vol. 14, 2023. |
Share this
- March 2025 (1)
- January 2025 (1)
- December 2024 (2)
- November 2024 (3)
- October 2024 (4)
- September 2024 (2)
- August 2024 (3)
- July 2024 (6)
- June 2024 (3)
- May 2024 (2)
- April 2024 (1)
- March 2024 (1)
- January 2024 (1)
- November 2023 (2)
- October 2023 (5)
- September 2023 (2)
- August 2023 (1)
- July 2023 (1)
- May 2023 (1)
- December 2022 (3)
- August 2022 (1)
- June 2022 (1)
- May 2022 (2)
- April 2022 (2)
- March 2022 (7)
- February 2022 (2)
- January 2022 (3)
- December 2021 (3)
- November 2021 (3)
- October 2021 (2)
- September 2021 (3)
- August 2021 (3)
- July 2021 (2)
- June 2021 (1)
- March 2021 (1)
- October 2020 (1)
- June 2020 (1)
- May 2020 (1)
- April 2020 (4)
- November 2019 (1)
- July 2019 (2)
- June 2019 (1)
- May 2019 (1)
- March 2019 (1)
- November 2018 (1)
- September 2018 (1)
- January 2018 (1)
- October 2017 (1)
- September 2017 (1)
- July 2017 (1)
- June 2017 (1)
- May 2017 (1)
- January 2017 (1)
- December 2016 (3)
- November 2016 (2)
- October 2016 (1)
- May 2016 (2)
- August 2015 (2)
- July 2015 (1)