Share this
Testing PAEK - Is It Any Good?
by 3devo on Jul 19, 2017 11:18:00 AM
Here at 3devo, we really enjoy testing a variety of different filaments. So now, it was time to try PAEK. As you may or may not know, PAEK is a family of semi-crystalline thermoplastics with high-temperature stability and high mechanical strength. We were lucky enough to test some AvaSpire AV-621 from Solvay (provided by ALBIS Plastique France). Catchy name, but is it any good? This article will cover all you need to know about PAEK and how it performed in our tests.
General Information
As mentioned PAEK, or polyaryletherketone, is a family of semi-crystalline thermoplastics. In this family you will find:
- Polyetherketone (PEK)
- Polyetheretherketone (PEEK)
- Polyetherketoneketone (PEKK)
- Polyetheretherketoneketone (PEEKK)
- Polyetherketoneetherketoneketone (PEKEKK)
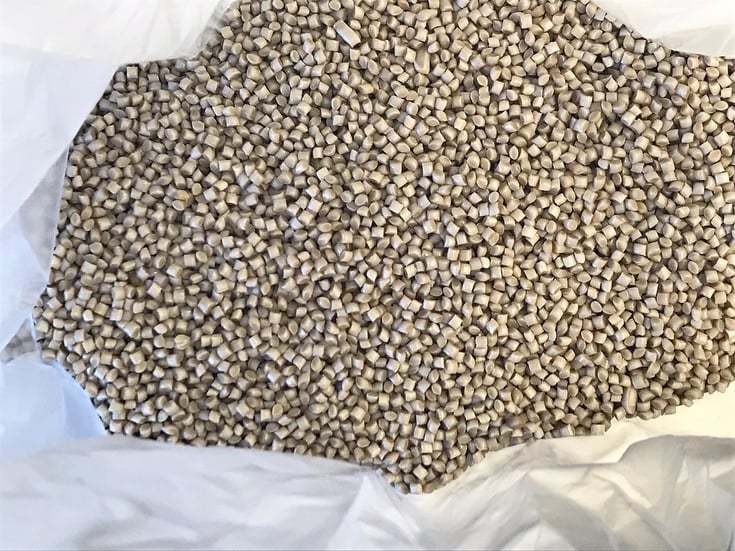
PAEK pellets provided by ALBIS Plastique France
Polyaryletherketone (PAEK) was first prepared in the early 1970s, but the results and the overall process were somewhat limited. PEEK was the first thermoplastic to go large scale in 1977, where ICI used polyesterification reactions to create the polymer. In 1981, Victrex of Lancashire, England, introduced PEEK resins commercially. Next came PEK, introduced by BASF AG, the giant German plastics company, which attempted to gain the total market share, eventually stopping all production of PEKEKK resins. This left Victrex as the only supplier of PEK resins in the world.
In the end, PEEK’s growth rates started to soar, mainly due to its high mechanical strength and chemical resistance. From vehicles to aircrafts to most electronics and medical applications, more and more suppliers entered the market. These suppliers include:
- Victrex (UK)
- Solvay Speciality Polymers (Belgium and US)
- Panjin Zhongrun High-Performance Polymers (China)
- Jida Evonik High-Performance Polymers (China)
Below is a list of some of the advantages and disadvantages of using PAEK:
Advantages
- Highly fire-resistant
- Good chemical resistance
- Can be used for high temperature applications
- Excellent mechanical and dielectric properties
Disadvantages
- Relatively high cost material
- Anisotropic
- High temperature molding and extrusion required
PAEK Extrusion Test
In our first attempt to create PAEK filament, we used the AV-621 NT grade produced by AvaSpire with a melting point of 340°C, which we pre-dried at 150°C for 4 hours. The first step in the extrusion process was using PX2 cleaning purge (with a temperature range of 280-420°C) as a transition material to raise the temperature of all heaters to 380°C.
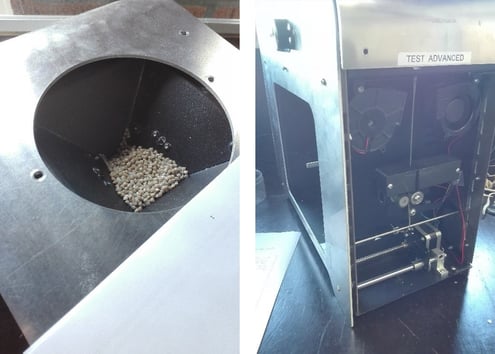
Filling up the Composer 450, then running the test
The first thing we noticed while extruding with an overall temperature of 380°C was many air bubbles in the filament. This could mean two things: the granulate was not dry enough, or the overall temperature was too high. Lowering the overall temperature by 10°C improved the quality a lot, but now we faced nozzle lip buildup, as you can see in the picture below.
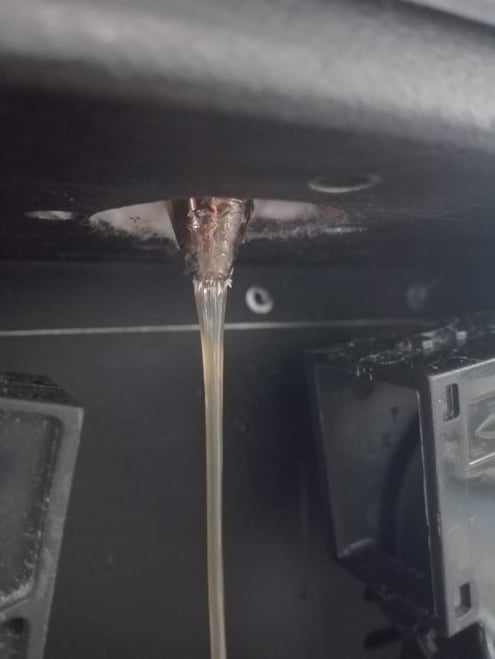
Nozzle lip buildup
Some polymers tend to have this problem, and it causes significant surface roughness of the filament. In this case, the buildup was reduced by increasing the temperature of the front heater.
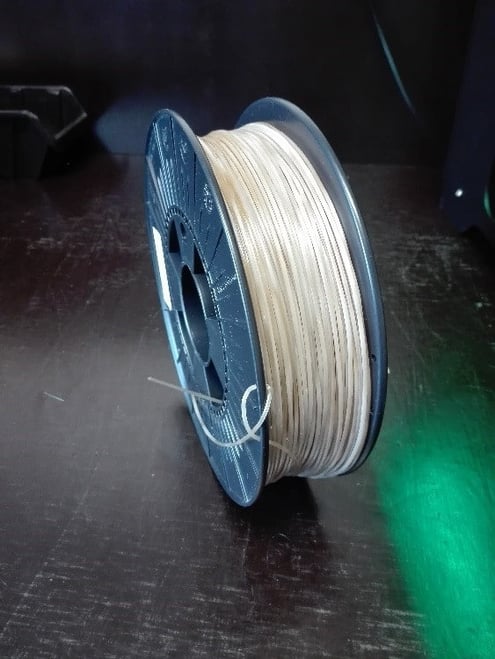
The final spool of extruded PAEK, a little rough around the edges
In the end, we managed to create a spool of PAEK with a filament thickness of 1.75mm, but the surface of the filament was still on the rough side. This means we will keep looking for better settings on the Composer 450, but at least the machine has now proven its ability to create PAEK filament. This adds up in the list of successfully tested high-end polymers, along with materials such as PEEK and PEKK.
Share this
- March 2025 (1)
- January 2025 (1)
- December 2024 (2)
- November 2024 (3)
- October 2024 (4)
- September 2024 (2)
- August 2024 (3)
- July 2024 (6)
- June 2024 (3)
- May 2024 (2)
- April 2024 (1)
- March 2024 (1)
- January 2024 (1)
- November 2023 (2)
- October 2023 (5)
- September 2023 (2)
- August 2023 (1)
- July 2023 (1)
- May 2023 (1)
- December 2022 (3)
- August 2022 (1)
- June 2022 (1)
- May 2022 (2)
- April 2022 (2)
- March 2022 (7)
- February 2022 (2)
- January 2022 (3)
- December 2021 (3)
- November 2021 (3)
- October 2021 (2)
- September 2021 (3)
- August 2021 (3)
- July 2021 (2)
- June 2021 (1)
- March 2021 (1)
- October 2020 (1)
- June 2020 (1)
- May 2020 (1)
- April 2020 (4)
- November 2019 (1)
- July 2019 (2)
- June 2019 (1)
- May 2019 (1)
- March 2019 (1)
- November 2018 (1)
- September 2018 (1)
- January 2018 (1)
- October 2017 (1)
- September 2017 (1)
- July 2017 (1)
- June 2017 (1)
- May 2017 (1)
- January 2017 (1)
- December 2016 (3)
- November 2016 (2)
- October 2016 (1)
- May 2016 (2)
- August 2015 (2)
- July 2015 (1)