
Gaining Control Over Acoustic Development
Introduction
Maximizing efficiency,
while reducing development times
Sika Automotive, a preferred partner for leading OEMs and automotive component suppliers, needed to streamline prototyping and pre-series production for their innovative heat-expandable acoustic inserts. 3devo’s Composer 350 Filament Maker, capable of extruding heat-reactive, low-temp materials, has helped Sika switch to in-house 3D printing.
Background
Sika Automotive is a global leader in automotive bonding, sealing, damping and reinforcing solutions. The company develops lightweight, robust and customized chassis components for prominent German, French and U.K. OEMs. Sika’s state-of-the-art acoustic inserts are engineered using a proprietary material called SikaBaffle®. 3devo’s Composer 350 allows them to process this heat-reactive, highly expandable thermoplastic into 3D printable filament, thus paving the way for efficient and streamlined in-house prototyping and pre-series production.
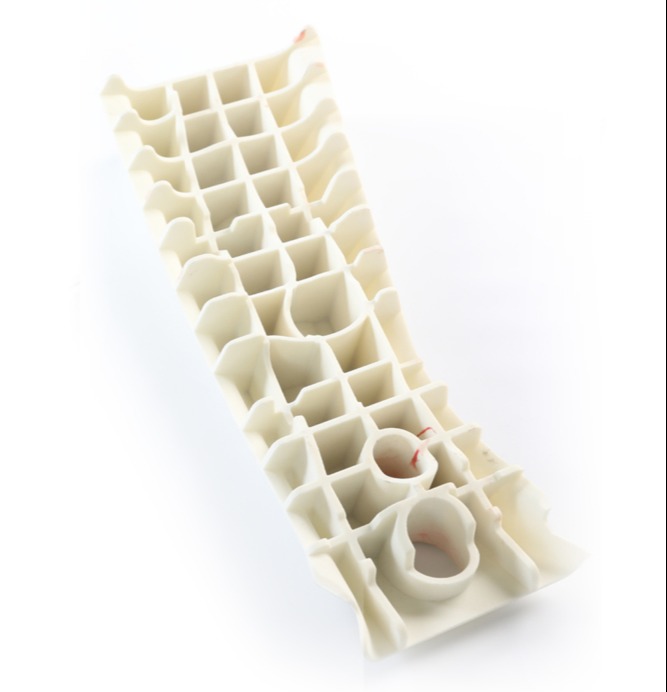
The Challenge
Sika’s complex expandable cavity sealers for vehicle body-in-white are made using SikaBaffle®, a highly expandable, heat-reactive thermoplastic. A typical cavity sealer requires 5-10 design iterations. Injection molding these prototypes was a lengthy and resource-intensive process, prompting Sika to consider in-house 3D printing as an alternative. For this, they required a cost-effective filament extruder that could process medium melt flow index polymers like SikaBaffle® without changing its chemical composition.
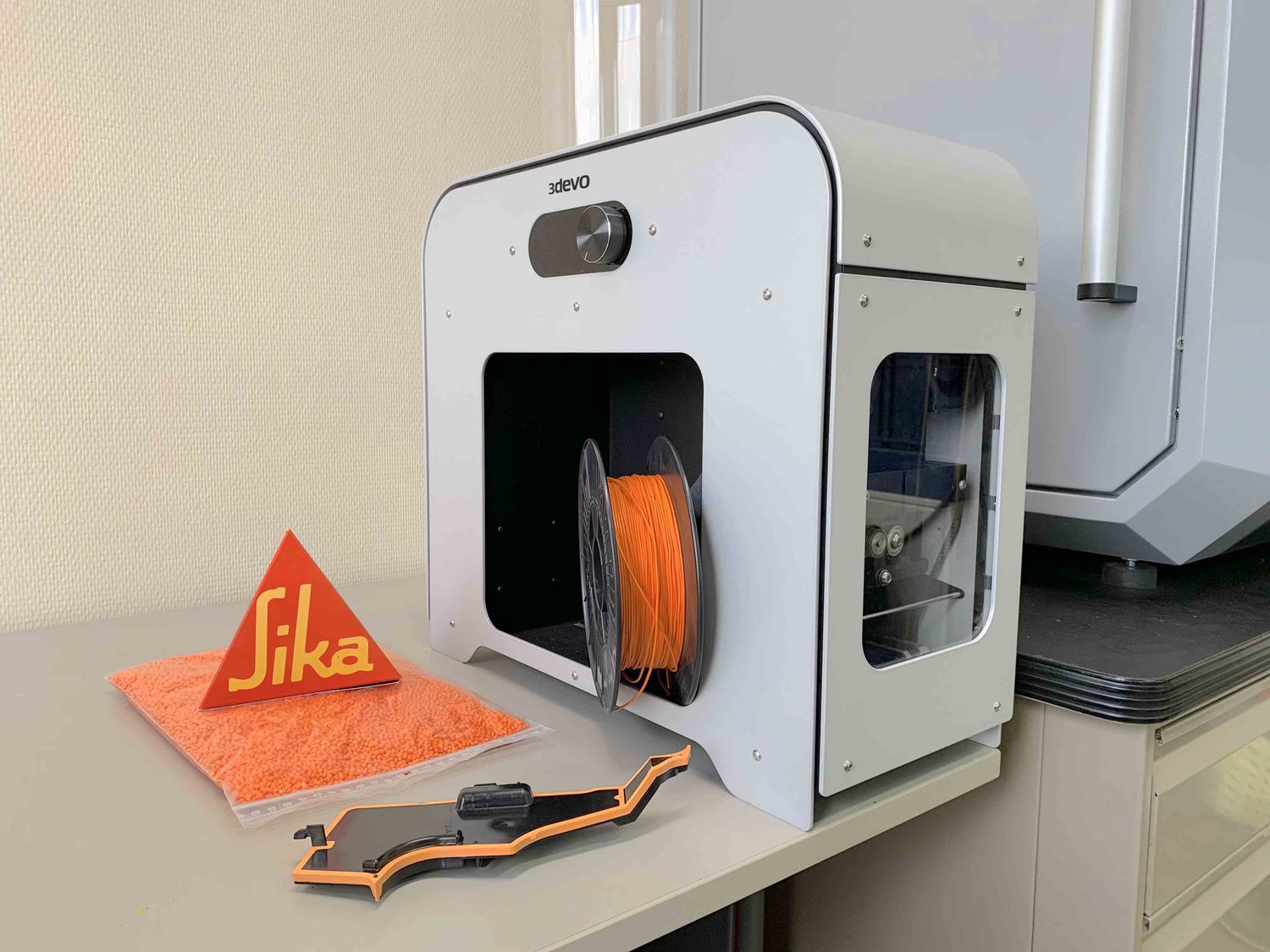
The Solution
In order to 3D print their cavity sealers, Sika needed a filament maker that could successfully process SikaBaffle®, a material that had already been tested and was available in pellet form. A low melting point of 90°C made SikaBaffle® incompatible with most extruders. The 3devo Composer 350, however, was able to successfully extrude the material. It joined Sika’s manufacturing facility in December 2018, along with the German RepRap 3D printer.
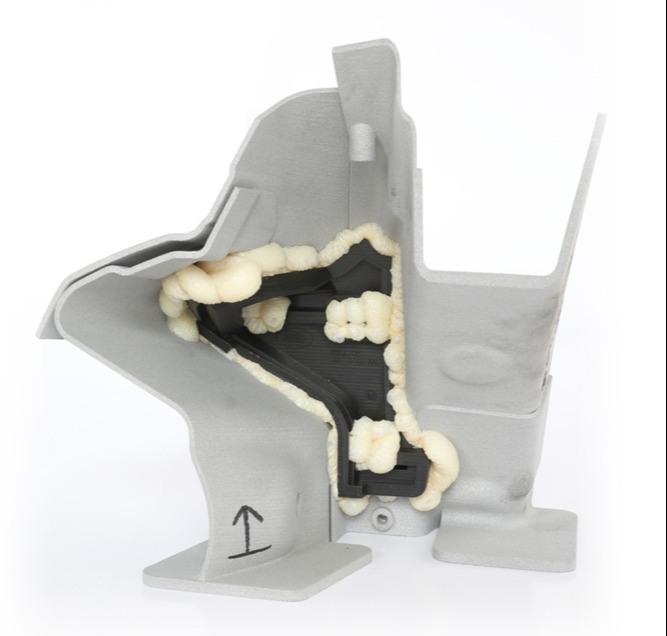
Get the Full Sika
Customer Story
Customer Story
“With the support of a reliable filament extruder trimmed to our proprietary materials, we’ve been able to accelerate the introduction of 3D printing applications for our acoustic sealing solutions, thus enabling our automotive OEM customers to reduce development time and efforts.”

Jose Bautista
Global Product Manager (Acoustic and Sealing Foams)
Workflow Highlights
- Complete control over component modifications and improvements
Sika’s new in-house 3D printing setup facilitated by the Composer 350 allows prototypes to be physically tested and modified – offering more accuracy and freedom than on-screen calculations. - Reduced dependence on tooling or third-party suppliers
By choosing in-house 3D printing over third-party injection molding, Sika enjoys a high degree of autonomy over prototyping and production. The company’s pre-series production schedules are no longer dependent on tooling or external sources. - Lead times reduced by 90% for SikaBaffle® components
Thanks to the freedom, efficiency and control offered by in-house filament extrusion and 3D printing, lead times for SikaBaffle® cavity sealers have dropped from 4-8 weeks to 2-5 days.
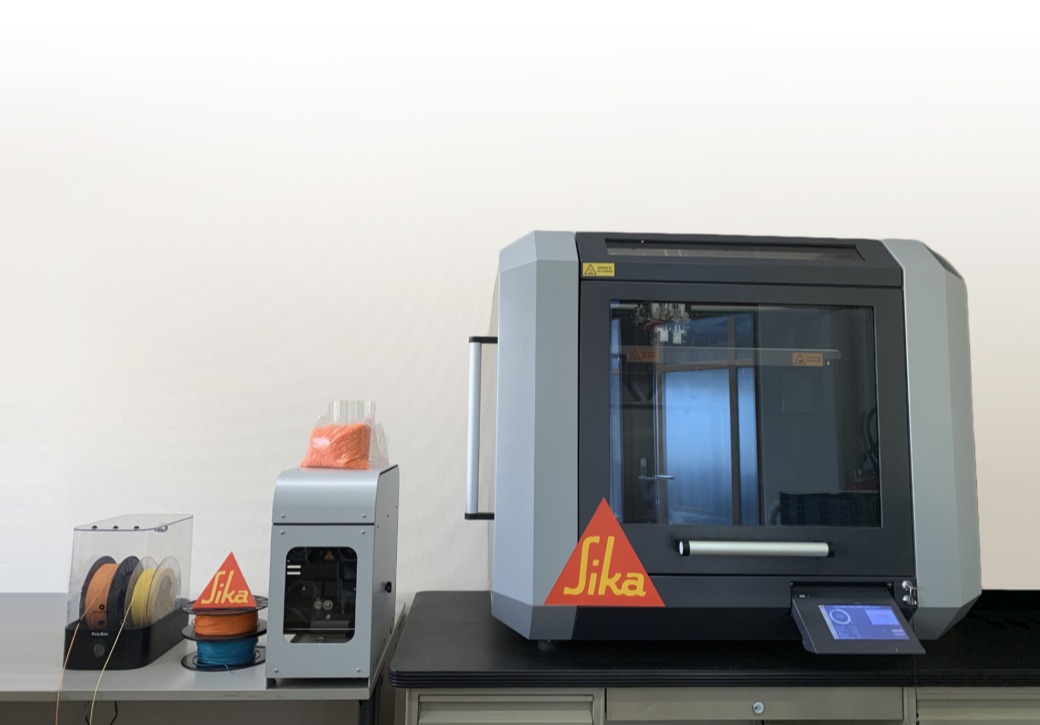

More Success Stories
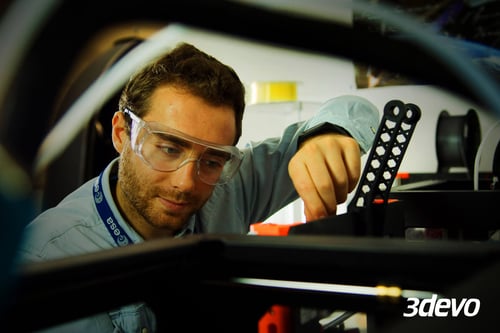
European Space Agency
How do researchers at ESA have the freedom to innovate – without wasting resources in the process.
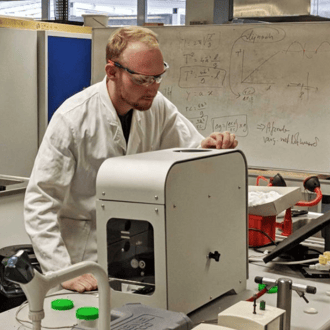
Fontys University
How Fontys gained the ability to expand their polymer development studies – at a fraction of the cost.