Share this
How We're Developing a Pressure Sensor for the Extrusion Process
by Gigi Palczer on Mar 6, 2025 1:43:23 PM
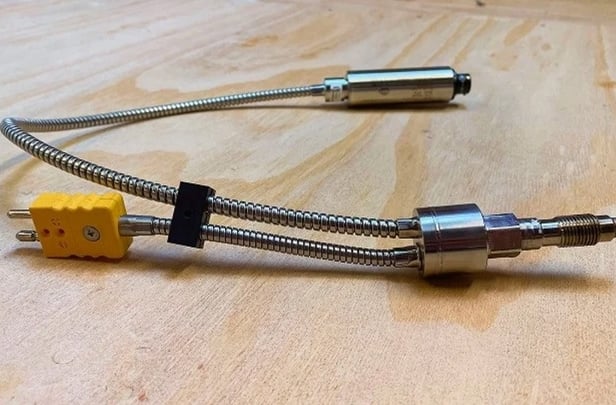
If you’ve ever experimented with making your own 3D printing filament, you know that even the tiniest changes can have a big impact. Sure, on paper, it’s just melting plastic and pushing it through a nozzle. But in reality? The extrusion process is a balancing act.
Small adjustments in temperature, screw speed, and material composition can be the difference between a perfect filament and a tangled, inconsistent mess. But here’s where things get interesting - filament diameter fluctuations don’t always have an obvious cause. Even when all visible settings remain stable, unexplained variations still occur.
So what’s happening inside the extruder?
The Hidden Variable in Filament Extrusion: Pressure
When dialing in filament settings, most people focus on temperature, screw speed, and nozzle diameter. But what often goes unnoticed is the fact that all of these settings influence an even more critical factor: pressure inside the extruder.
The extruder doesn’t just melt plastic and push it through the nozzle—it does so under pressure. That pressure fluctuates depending on how smoothly the material flows, and those fluctuations can have a direct impact on filament quality. If the pressure suddenly spikes or drops, filament diameter can change unexpectedly, leading to under-extrusion, inconsistent thickness, or even clogs.
The problem is, until now, these pressure fluctuations were invisible. You could have a seemingly perfect setup, with stable temperature and screw speed, but still experience unexplained inconsistencies in your filament. That’s because the missing piece of the puzzle has always been pressure.
The extruder forces molten plastic through a tiny opening, generating resistance. If that resistance - or pressure - fluctuates, the filament diameter fluctuates too. A sudden drop can cause under-extrusion or voids in the material, while a spike can lead to jams or irregular flow.
Before the pressure sensor, the only way to understand why filament inconsistencies happened was through trial and error. If filament diameter suddenly changed, we could adjust temperature, screw speed, or another setting and see if it improved—but we couldn't directly see the pressure shifts happening inside the extruder in real-time.
Now, with the pressure sensor, we can track the immediate effect of each setting change. If you lower the temperature and see a drop in pressure, you know exactly what caused it. If you increase the screw speed and pressure suddenly spikes, there's no second-guessing. Every change has a direct and measurable impact, making troubleshooting and fine-tuning far more precise.
In this image, we can see the difference between a stable and unstable pressure signal:
What We Learned From The HDPE Experiment
Our tests with HDPE highlighted why pressure monitoring is so important. HDPE is known for its challenging flow behavior, and when we ran it through our extruder, we saw unexpected pressure drop-offs - even when the temperature remained stable.
By pulling the screw at different moments, we discovered why:
- Stable pressure = full screw flights (consistent material flow through the extruder).
- Pressure drop = half-filled screw flights (poor material conveyance leading to inconsistencies).
The images below showcase the two scenarios:
The issue? The material was melting too early, before the second heating zone, leading to incomplete conveyance and inconsistent flow. This was only confirmed because the pressure sensor allowed us to track changes in real time.
This experiment reinforced an important takeaway: stable pressure = stable filament. Even if everything else seems fine, fluctuations in pressure inside the extruder will result in inconsistencies. The only way to truly understand and control this is through real-time pressure monitoring - a critical tool for achieving a consistent extrusion process.
Why We Didn't Need This Before (And Why We Do Now)
With the Filament Maker ONE, we had a clever but indirect way to track extrusion resistance: the DC motor. DC motors naturally adjust their current draw based on how much resistance they encounter - more resistance = higher current, less resistance = lower current. This meant that if you were paying attention to the motor's current draw, you could sometimes spot extrusion issues before they became major problems.
Of course, this method was far from perfect. It was an indirect signal, and interpreting it required experience and guesswork. It wasn’t an exact science.
Now, with the Filament Maker TWO, we’ve made a huge improvement by switching to a stepper motor, which provides precise speed control and allows for more consistent extrusion overall. However, that means we lost our only way to detect resistance changes indirectly.
That’s why the pressure sensor is such a game-changer. It doesn’t just restore the ability to monitor extrusion resistance - it gives us a far more accurate and real-time measurement of what's happening inside the extruder.
Why Pressure Fluctuations Impact the Extrusion Process
A pressure sensor continuously measures the force inside the extruder in real time. Think of it as X-ray vision for filament extrusion - giving you instant feedback on what’s happening beneath the surface.
Schematic of how melting in the barrel can be shifted:
Here’s what that means for you:
- Instant troubleshooting: No more guessing why your filament is coming out inconsistent. If the pressure is spiking or dropping, you’ll know exactly when and where the problem is happening.
- Better material insights: Want to work with a tricky material like PEEK or a recycled polymer blend? The pressure sensor shows you how it reacts under extrusion conditions, so you can fine-tune your settings.
- Next-level control: By understanding pressure variations, you can dial in the perfect combination of temperature, screw speed, and nozzle size for your material.
Basically, it’s the difference between flying blind and having a real-time dashboard for your extrusion process.
Filament Extrusion Just Got Smarter
So, is a pressure sensor absolutely necessary for making filament? No. People have been making filament for years without one.
But here’s the thing: once you have real-time pressure data, you’ll never want to go back.
It’s like the difference between cooking with an old-school oven versus one with a built-in thermometer and digital controls. Sure, you can make it work with just a timer and a little intuition - but once you start cooking with precise temperature feedback, you wonder how you ever lived without it.
This is especially true for people working with experimental or high-performance materials. When you’re developing composites, recycled plastics, or high-temperature filaments, every little variation in pressure affects the final product. Instead of running endless trial-and-error tests, you’ll have the data to make smart adjustments instantly.
What This Means for R&D and Material Development
For researchers, engineers, and material scientists, real-time pressure monitoring opens up new possibilities.
- Testing a new polymer? Now you can see how it reacts under extrusion conditions.
- Working with a bio-based or recycled material? Track pressure trends to understand flow stability and degradation.
- Developing a specialty composite? Monitor how fillers and additives influence extrusion behavior.
In short, a pressure sensor doesn’t just make filament better - it makes material development smarter.
What's Next?
Right now, we’re deep in the testing phase, developing the pressure sensor and testing it with different materials to ensure it provides useful, actionable insights. While it’s not yet a standard product if you're interested, reach out to our sales or support team - you may be able to access an early version with a special offer!
In the meantime, we’re really excited to see how this will impact the way people approach filament extrusion. Because at the end of the day, this isn’t just about adding a sensor -it’s about making filament extrusion smarter, more predictable, and way more fun to experiment with.
Final Thoughts
Filament extrusion has always been part science, part intuition - but the more precise our tools become, the less we have to rely on guesswork. Every experienced filament maker knows that even when you think you’ve nailed down the perfect settings, filament inconsistencies can still creep in for unexplained reasons.
That’s exactly why the pressure sensor isn’t just an extra feature - it’s a fundamental shift in how we approach extrusion. By making pressure visible in real-time, it allows us to take full control over the process, ensuring that filament diameter remains stable and extrusion remains consistent.
Whether you’re an R&D professional experimenting with new polymers, an engineer working with recycled materials, or someone pushing the boundaries of filament development, understanding pressure in the extrusion process could be the key to achieving better filament consistency. As we continue refining this technology, we’re excited to see how it will transform filament production.
So, if you’ve ever wondered what’s really happening inside your extruder, get ready - because soon, you won’t have to guess anymore. You’ll know.
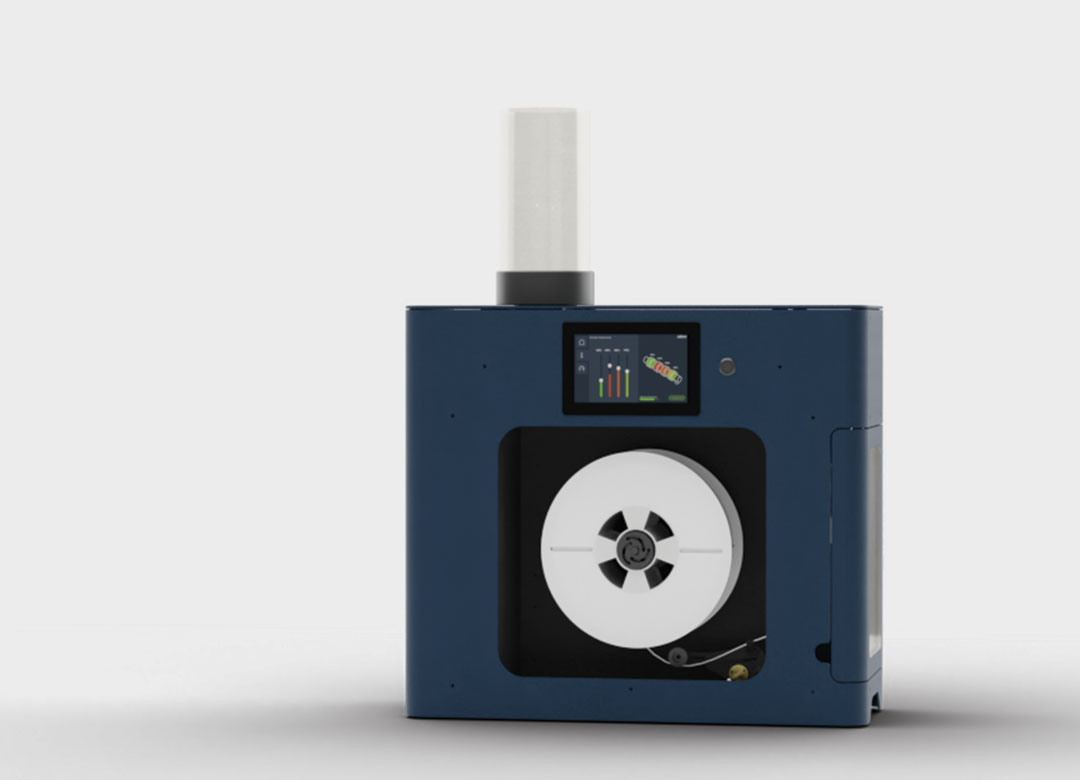
Discover our new Filament Maker TWO
Learn more about our new FM2 - a powerful filament extruder and filament research platform in one machine.
Discover Filament Maker TWO
Frequently Asked Questions (FAQs)
We are currently developing the pressure sensor, and it is not a standard product yet. However, if you're interested, please reach out to our sales or support team - you may be able to access an early version with a special offer!
By providing real-time data on pressure fluctuations, the sensor helps users understand exactly how extrusion conditions are affecting filament diameter. Instead of relying on trial and error, you can pinpoint the cause of inconsistencies and adjust temperature, screw speed, or other settings with confidence. The result? More stable, reliable, and high-quality filament.
Anyone working with new, experimental, or recycled materials will gain a huge advantage from pressure monitoring. Researchers, engineers, and filament makers who deal with high-performance materials like PEEK, composites, and bio-based plastics will especially benefit, as they require fine-tuned control over extrusion settings.
No, the Filament Maker ONE is not designed for this add-on. The main reason is that its die-head design is not built to accommodate a pressure sensor. Additionally, since it uses a DC motor, it already provides an indirect way to monitor extrusion resistance through current draw, making the sensor less necessary.
Share this
- March 2025 (1)
- January 2025 (1)
- December 2024 (2)
- November 2024 (3)
- October 2024 (4)
- September 2024 (2)
- August 2024 (3)
- July 2024 (6)
- June 2024 (3)
- May 2024 (2)
- April 2024 (1)
- March 2024 (1)
- January 2024 (1)
- November 2023 (2)
- October 2023 (5)
- September 2023 (2)
- August 2023 (1)
- July 2023 (1)
- May 2023 (1)
- December 2022 (3)
- August 2022 (1)
- June 2022 (1)
- May 2022 (2)
- April 2022 (2)
- March 2022 (7)
- February 2022 (2)
- January 2022 (3)
- December 2021 (3)
- November 2021 (3)
- October 2021 (2)
- September 2021 (3)
- August 2021 (3)
- July 2021 (2)
- June 2021 (1)
- March 2021 (1)
- October 2020 (1)
- June 2020 (1)
- May 2020 (1)
- April 2020 (4)
- November 2019 (1)
- July 2019 (2)
- June 2019 (1)
- May 2019 (1)
- March 2019 (1)
- November 2018 (1)
- September 2018 (1)
- January 2018 (1)
- October 2017 (1)
- September 2017 (1)
- July 2017 (1)
- June 2017 (1)
- May 2017 (1)
- January 2017 (1)
- December 2016 (3)
- November 2016 (2)
- October 2016 (1)
- May 2016 (2)
- August 2015 (2)
- July 2015 (1)