Share this
Staying Curious with 3D Printing: How Failing Leads to Winning!
by Ellie Pritchard on Nov 24, 2023 11:31:01 AM

“An expert is a person who has made all the mistakes that can be made in a very narrow field.” - Niels Bohr, Nobel Prize Winner for Physics.
In all aspects of life, mistakes facilitate growth. We learn to walk by falling, or master a new language by saying the wrong words. Progress is rarely linear because we’re often side-stepping, testing the ground in different places before finding the best path forward. The mistakes we make are the result of curiosity and asking ourselves “What if…?”
In the 3D printing industry, these “what ifs” are drivers of innovation, making space for new developments and processes. At 3devo, not only do we recognize the importance of curiosity, we build machines to enable it. With our Filament Maker, users can transform plastic waste and failed prints into fresh opportunities, crafting their own materials for new endeavors.
But we also knew that our Filament Maker had room to grow. Conceived in 2016, the concept was solid, but real-world testing and invaluable customer feedback have since revealed untapped potential. So we asked ourselves, “What if…” and developed a plan to understand precisely what our customers need and how we could harness our technology to optimize their projects.
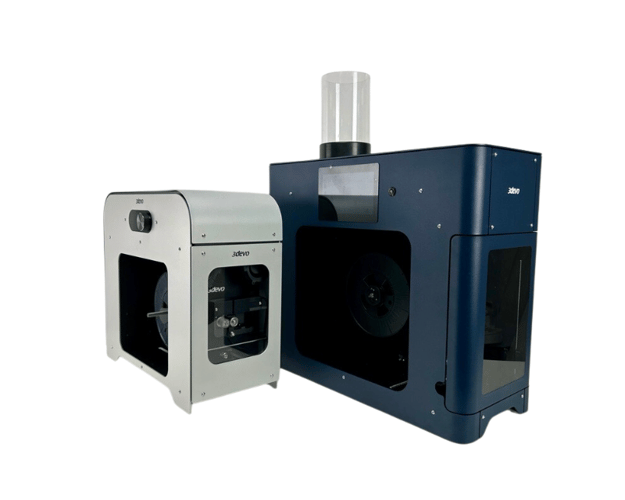
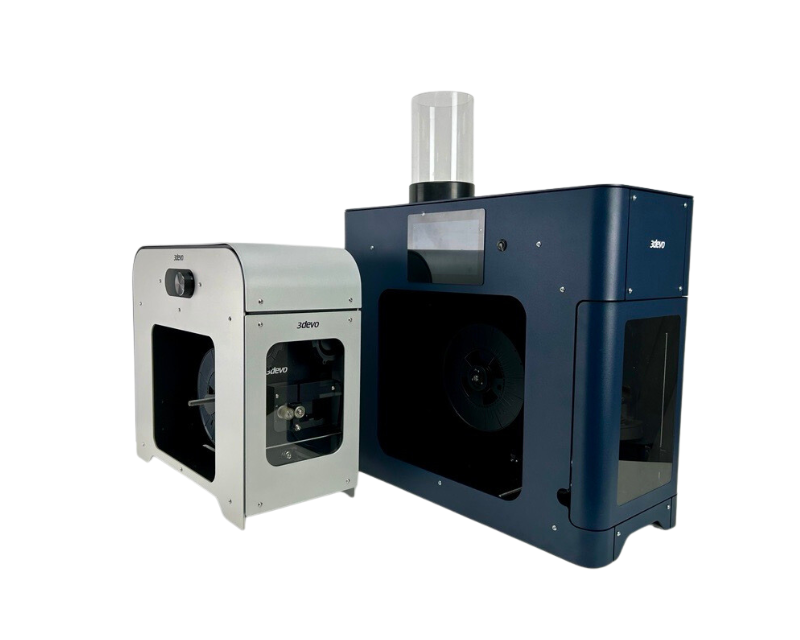
Customer-driven insights
The 3D printing industry thrives on a willingness to experiment and make mistakes. The technology that underlies 3D printing is relatively new and continues to evolve, bringing with it opportunities for complex problem-solving, materials development, and adaptation to market demands. As 3devo R&D Manager Floris Wardennier tells us, “this industry is still developing. To innovate, you need to look and reach for limitations in order to go beyond what is already possible or available.”
So how did we incorporate this into our own culture? Two of our core values as a company are courage and openness; we believe that it takes bravery and determination to pursue new opportunities and that every failure has the potential to lead to success. But we also believe in being transparent and open, both within our team and towards our customers. With these values in mind, Floris’s team began searching for the limitations of the Filament Maker, conducting interviews with customers and embracing the longstanding relationships we’ve cultivated over years of trust and collaboration.
“As part of this cooperative process, we learned about the challenges our customers faced and about their unique experiences using our technology,” says Floris. “We listened carefully and discussed ways in which we could make improvements to better support their projects. This is a really important step in the evolution of our Filament Maker.”
Our team sought feedback by encouraging our active user base to complete surveys and we established open lines of communication through account management calls, allowing us to conduct in-depth interviews with our clients. Engaging with our customers directly at industry events such as Formnext and other exhibitions also provided us with invaluable insights and perspectives.
Internally, our team embraced a culture of experimentation and research by investing hours of use on the Filament Makers ourselves. “The whole company is made up of naturally curious people, so this practice has been ingrained in our process for years,” says Floris.
What did we learn?
The outcome of our years of research (generated by hours spent on the machine and listening to user experiences) is a clear set of target points translated into ideas. We learned that the user needs more room for mistakes and experimentation. The Filament Maker is a tool for creating materials, but if something unexpected happens, customers need to be able to access certain parts of the machine quickly to minimize downtime. The feedback highlighted the importance of autonomy in research projects, and how accessibility of parts (for cleaning or repair) can encourage experimentation and innovation. Given more control over the extrusion process, users would be able to explore new possibilities and refine their creations. Two such examples of how we’ve addressed certain issues are:
- Nozzle Redesign: The nozzle of the Filament Maker was initially designed in a way that it could pop out of the system in the event of high pressure. The nozzle was redesigned with a more complex shape to remove a loose part from the equation, making sure the nozzle can no longer accidentally pop out of the system
- Screw Redesign: The screw rotation is controlled by a motor, a gearbox, and an encoder disk. The initial design was quite unforgiving because, in cases of high pressure inside the barrel, there was a small chance the screw could slide back by a few millimeters, crushing the encoder disk. The screw was redesigned as two separate pieces, to leave just enough room for the encoder and prevent the crushing issue.
%20-%20instasize%20(1).png?width=625&height=500&name=IMG_6811%20(1)%20-%20instasize%20(1).png)
Further potential
As we delved deeper into the evolving needs of our users, further opportunities for development became evident. These are focal points for our ongoing efforts to enhance our Filament Maker for the future.
We discovered that users require advanced data monitoring with more reliable and data-driven results, making their research more valuable. This would enable the collection of more data elements, an improved data accuracy through more advanced sensors, and better data insights via visualizations tailored to the user. On this particular point, one trusted customer expressed the need for more sensors across the entire machine, to recognize voltage spikes on motors, or lack thereof, as well as the temperature of coils and fans: “By comparing sensor material with the results in the database, it would be possible to improve the quality of the product in real time, and not only by firmware updates.” A further suggestion was to make all information accessible in an app for users to conduct their own research and improve the lifecycle of their creations.
Future-proofing is also a crucial consideration in the 3D printing industry to ensure longevity and relevance of technology. Rapid technological advancements necessitate adaptable solutions. We acknowledge our responsibility to anticipate the evolving needs of our customers, keep in mind the compatibility with emerging technologies, and take into account compliance with evolving standards. Our Filament Maker would benefit from a higher capacity for updates, giving room for it to evolve over time and build a robust, adaptive ecosystem for its users. A more scalable hardware would see advanced features being added over time through several firmware updates.
Our Customer Success Manager, Louis Rinaldo, expresses 3devo’s ambitions for Filament Maker developments of the near future: “We continuously strive to improve the hardware itself, by making the design smarter and more forgiving, allowing users to explore a range of increasingly difficult materials.” Louis also points out that while the Filament Maker's hardware is robust, occasional challenges arise due to the need for enhanced knowledge transfer from 3devo to our customers. “We’ve identified this as an area we need to improve. The key to making filament extrusion accessible is really about transfering the right knowledge at the right moment in the process, and that’s why we are focusing on crafting customized guided workflows.”
Shared goals, collective vision
“3devo is a strong and innovative company. But at the end of the day we are just a passionate group of people who share a goal, purpose, and values,” says Floris. “Through our purpose we are figuring out how we want to accomplish our ambitious goal: Enabling 1 million 3D printing innovations.”
By staying curious, we are strengthening our partnership with customers, actively seeking their input to make sure that our technology and hardware are exactly what they need. “This collaborative effort ensures that we are sincerely contributing to an innovative community,” Floris confirms. “We want to be a part of the progress and the success stories of our customers, and that means recognizing our own areas for improvement.”
Conclusion
In the ever-evolving landscape of 3D printing, 3devo's journey with the Filament Maker has been a testament to the transformative power of mistakes and continuous improvement. Rooted in a culture of courage and openness, we've embraced user feedback as a guiding force, translating years of research into tangible enhancements. The redesigned nozzle and screw mechanisms exemplify our commitment to empowering users with more room for experimentation. Looking ahead, our focus extends to advanced data monitoring and future-proofing, envisioning an ecosystem that adapts to industry advancements.
Check Out Our Expertise in Filament Extrusion
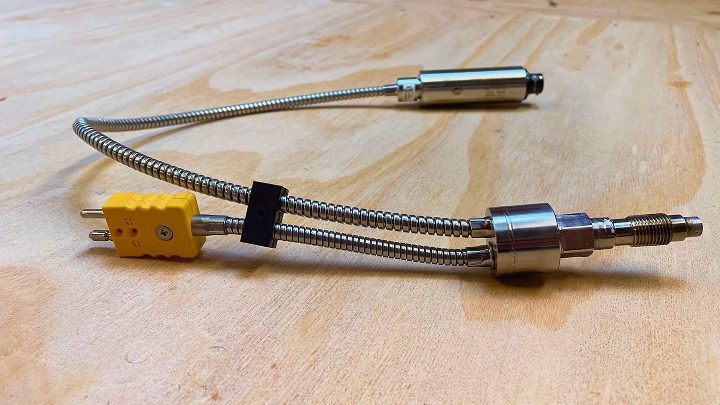
How We're Developing a Pressure Sensor for the Extrusion Process
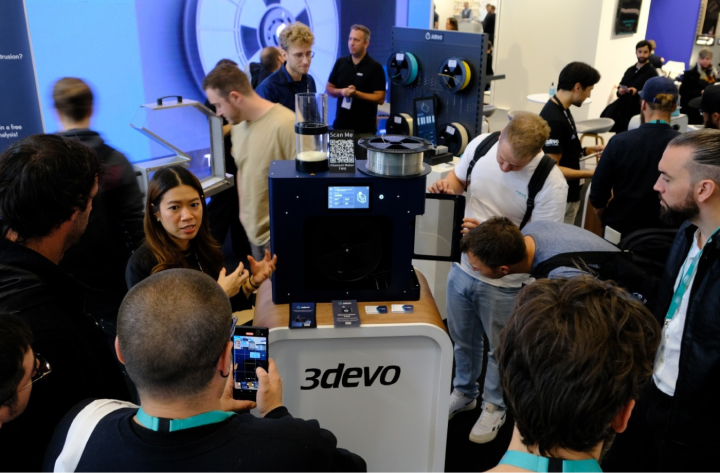
Filament Maker TWO vs. Alternatives: Compare Filament Extruders
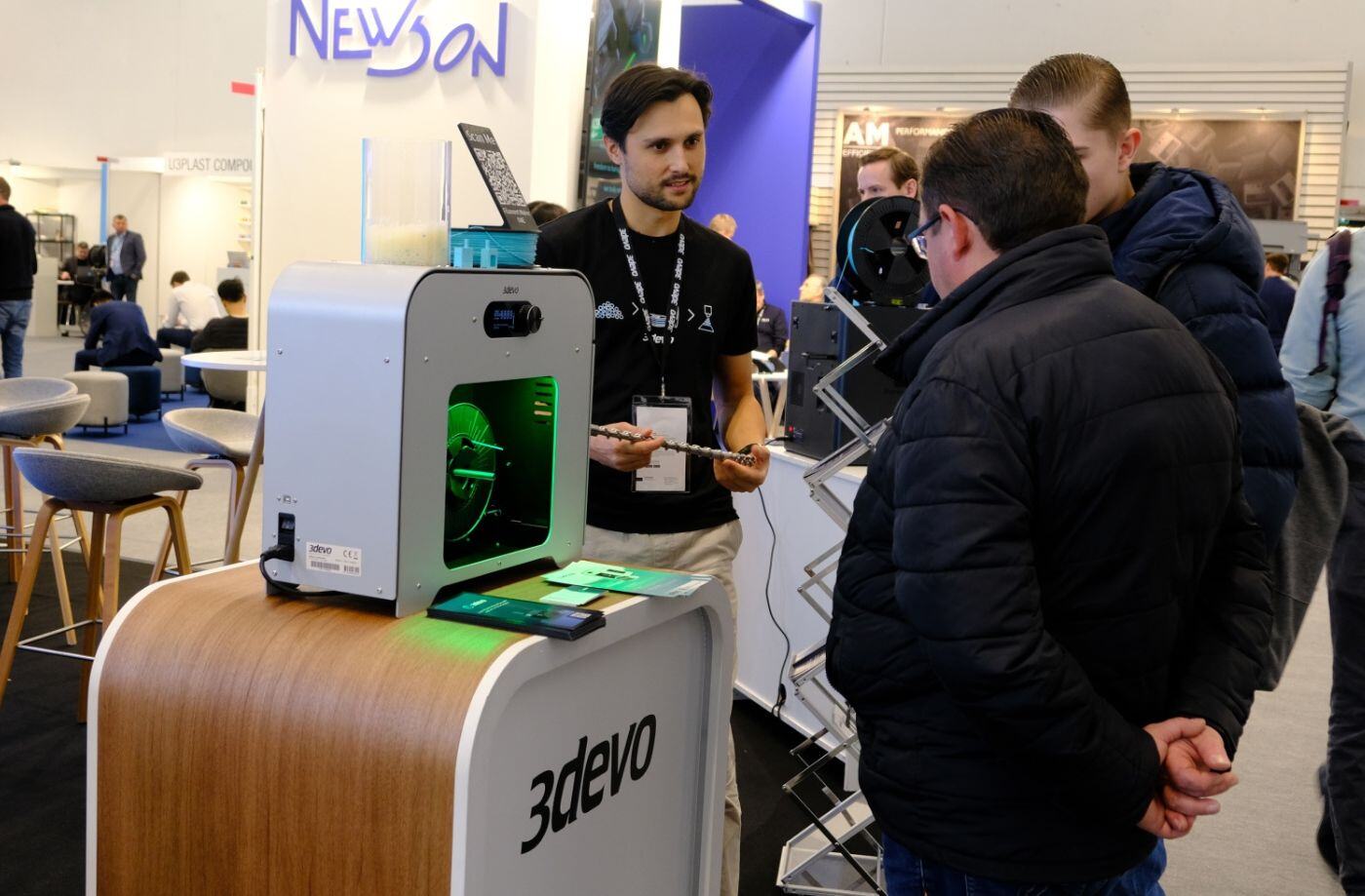
3devo 2024 Highlights: Reflecting on a Year of Growth and Change
Share this
- March 2025 (1)
- January 2025 (1)
- December 2024 (2)
- November 2024 (3)
- October 2024 (4)
- September 2024 (2)
- August 2024 (3)
- July 2024 (6)
- June 2024 (3)
- May 2024 (2)
- April 2024 (1)
- March 2024 (1)
- January 2024 (1)
- November 2023 (2)
- October 2023 (5)
- September 2023 (2)
- August 2023 (1)
- July 2023 (1)
- May 2023 (1)
- December 2022 (3)
- August 2022 (1)
- June 2022 (1)
- May 2022 (2)
- April 2022 (2)
- March 2022 (7)
- February 2022 (2)
- January 2022 (3)
- December 2021 (3)
- November 2021 (3)
- October 2021 (2)
- September 2021 (3)
- August 2021 (3)
- July 2021 (2)
- June 2021 (1)
- March 2021 (1)
- October 2020 (1)
- June 2020 (1)
- May 2020 (1)
- April 2020 (4)
- November 2019 (1)
- July 2019 (2)
- June 2019 (1)
- May 2019 (1)
- March 2019 (1)
- November 2018 (1)
- September 2018 (1)
- January 2018 (1)
- October 2017 (1)
- September 2017 (1)
- July 2017 (1)
- June 2017 (1)
- May 2017 (1)
- January 2017 (1)
- December 2016 (3)
- November 2016 (2)
- October 2016 (1)
- May 2016 (2)
- August 2015 (2)
- July 2015 (1)