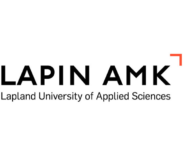
Taking Circular Economy from Theory to Practice
Introduction
Bringing Recyclability into Manufacturing
Lapland University of Applied Sciences (Lapland UAS), the testing ground for future-friendly technologies, needed a setup where old parts and prototypes were in storage shelves, rather than waste bins to stay on one of the core values within Lapland UAS, sustainability. 3devo’s full solution enabled Lapland UAS to manifest a circular economy within their 3D Printing lab.
Background
Lapland University of Applied Sciences (Lapland UAS), situated in northern Finland, was founded in 1992. Since then, it has expanded its reach to various fields of education, and evolved into a renowned institution that structures its curriculum and culture around innovation and eco-consciousness. With the establishment of their additive manufacturing laboratory on campus, students and researchers can now explore and experiment with more assignments, however, with the cost of large amounts of PLA 3D print waste. 3devo’s full solution makes for efficient processing of of the materials to create new.
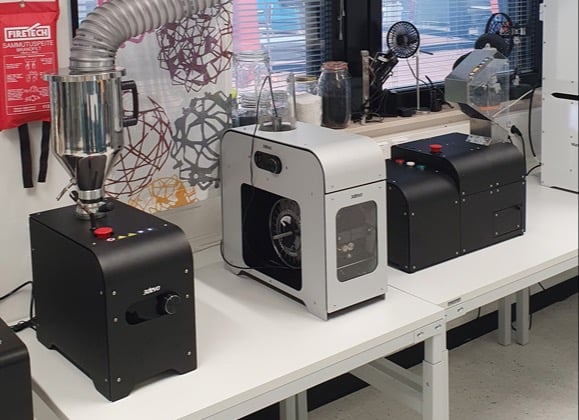
The Challenge
Students at the mechanical engineering wing of Lapland University of Applied Sciences were constrained by the amount of 3D printing they could perform in their laboratory. With materials being expensive, and 3D printing being a crucial part of engineering courses and research projects, the department was in need of a recycling solution for failed prints and an element of sustainability in the learning process.
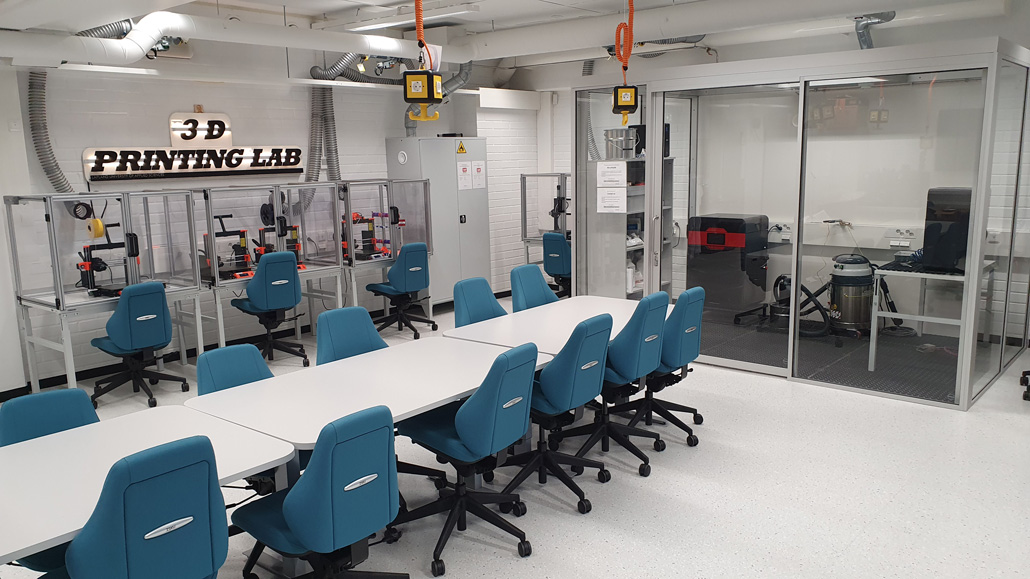
The Solution
One student was tasked with surveying the recycling landscape, comparing solutions available on the market and selecting a desktop extruder. The full set offered by 3devo, was selected to recycle commonly used materials into 3D printing filament, keeping with the university’s vision of bringing sustainability to educational practices.
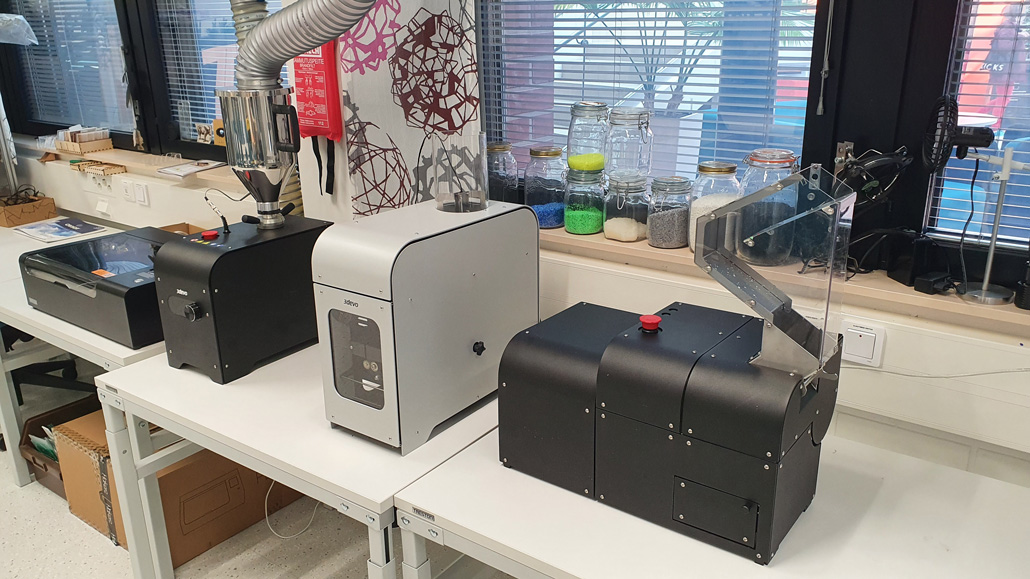
Download the Lapland
Case Study PDF
Case Study PDF
Workflow Highlights
- 100% Recycled PLA
The team at Lapland UAS, lead by Nicole’s research and experimentation has allowed for PLA to be recycled into 3D printing filament and 3d printable. ore accuracy and freedom than on-screen calculations. - Circular Economy in the Lab
Equipped with the 3devo machines, and the accompanying possibilities such as access to a material developers’ forum, Nicole and her supervisor were able to establish a working example of the circular economy within their laboratory.
- Minimizing Wastage
Now that PLA has been identified as a 100% recyclable material, they hope to arrive at similar results with PLA composites. In the long term, the entire effort is to establish a robust education system where the freedom to innovate stems from a determination to minimize wastage.
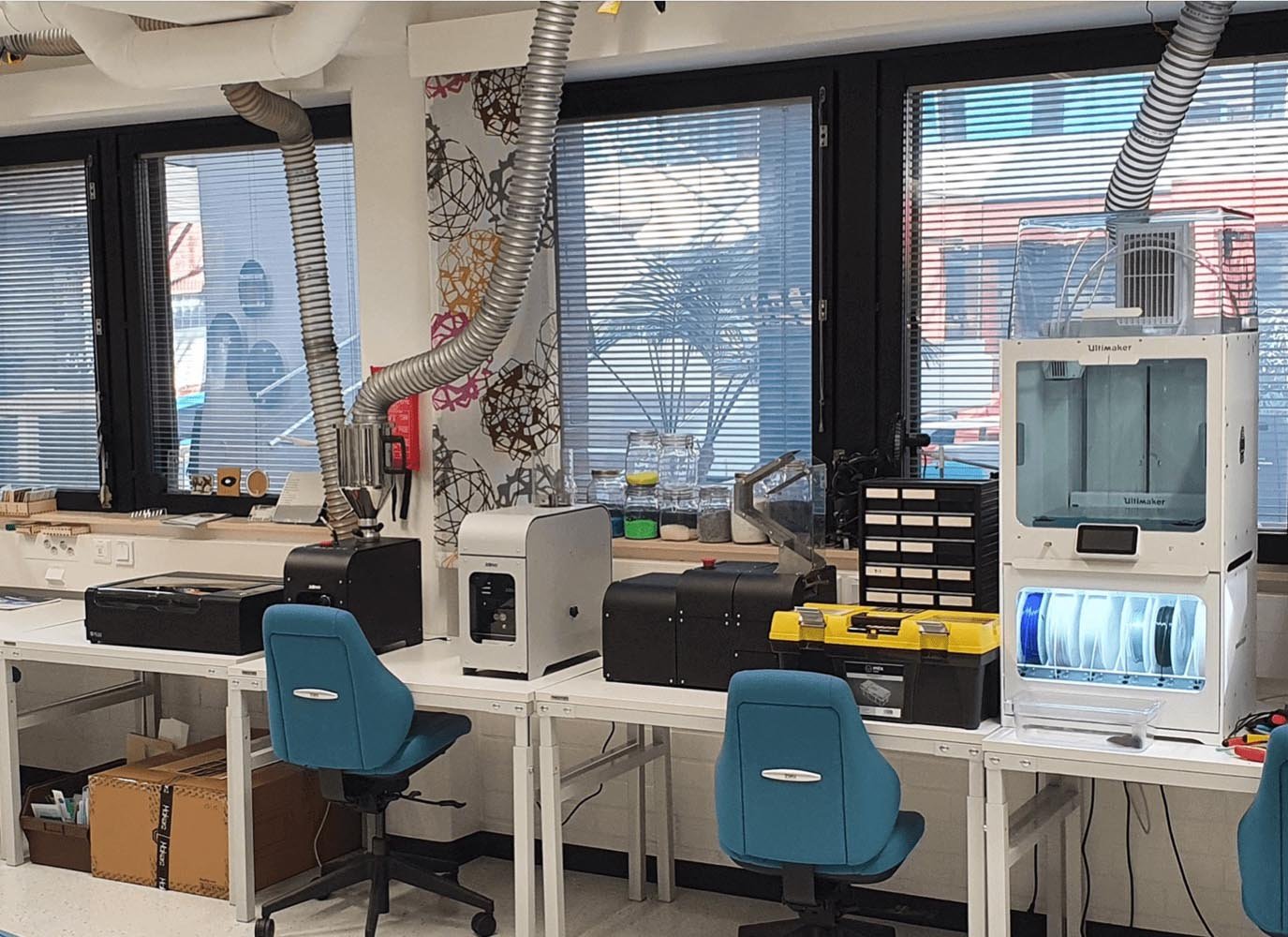
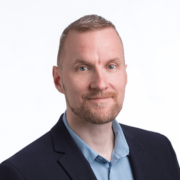
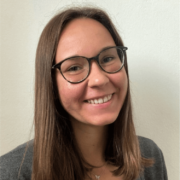
More Success Stories
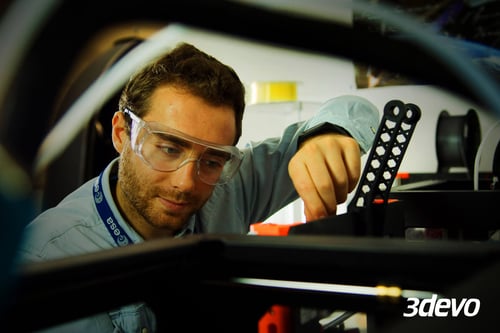
European Space Agency
How do researchers at ESA have the freedom to innovate – without wasting resources in the process.
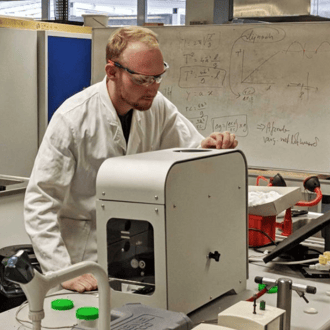
Fontys University
How Fontys gained the ability to expand their polymer development studies – at a fraction of the cost.
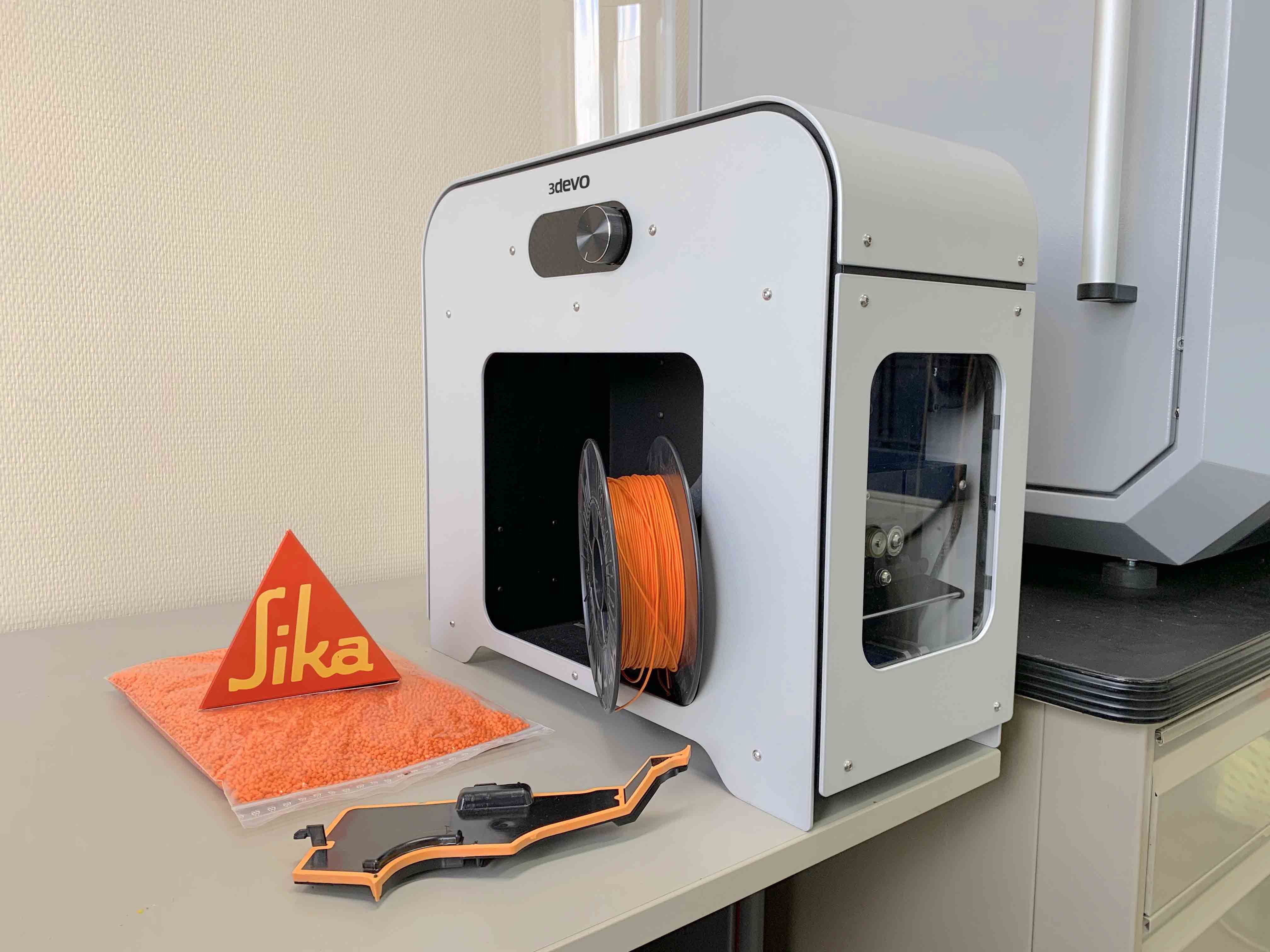
Sika Automotive
How Sika Automotive managed to reduce their production time – for their cavity sealers -from weeks to days.