Share this
Common Filament Defects: Your Guide to Troubleshooting
by Louis Rinaldo on Sep 18, 2023 3:49:09 PM
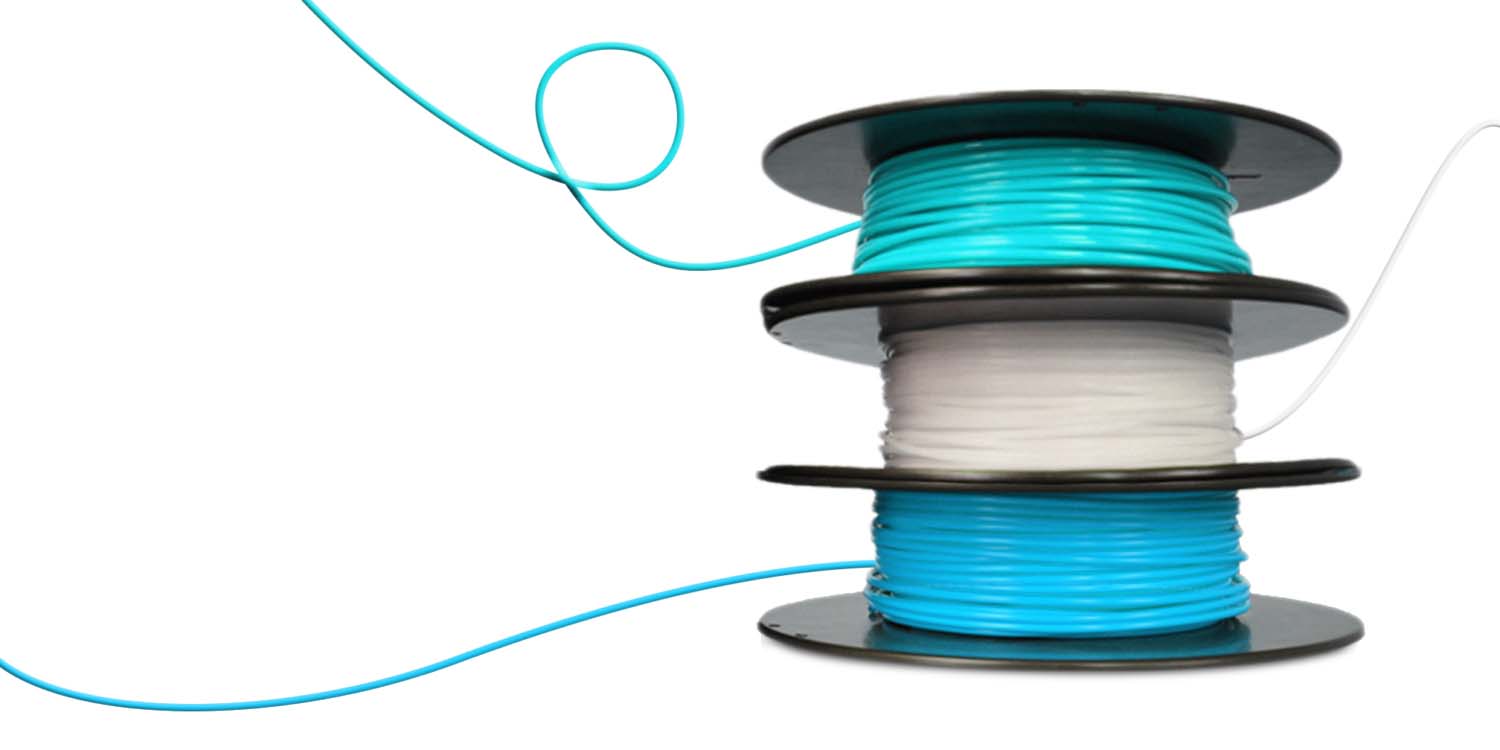
Introduction
When it comes to 3D printing, the quality of your filament can make all the difference between a successful print and a frustrating failure. But what exactly defines "good filament," and how can you ensure that your 3D printing material meets these standards? In this comprehensive guide, we'll delve into the fundamentals of filament quality from a processability perspective.
Let’s look at what defines good or bad filament, what the most common quality issues are, and how to solve them. Be prepared to learn a lot about the technical depths of the extrusion process.
What is Filament
In 3D printing technology, filament serves as the critical raw material utilized to fabricate intricate three-dimensional objects. This thermoplastic medium is methodically melted and layered by the 3D printer, adhering to precise design specifications inputted into the system. Available in a variety of compositions, each type of filament offers distinct properties that dictate the final product's attributes, such as durability, texture, and resilience.
As a cornerstone in the 3D printing process, selecting the appropriate filament is essential in achieving optimal results, underscoring its pivotal role in advancing innovations in additive manufacturing. To delve deeper into the intricacies of choosing the right material, you might find our blog on "The Fundamentals of Material Selection | 3devo extremely insightful. It guides you through the vital aspects to consider when embarking on a 3D printing project, ensuring that your creations not only come to life but thrive in their intended applications.
%20(1).png?width=800&height=640&name=silver-extruder-1%20-%20instasize%20(1)%20(1).png)
Material Compatibility and Selection
Selecting the right material is a critical step in the 3D printing process. Different materials offer unique characteristics that can significantly influence the outcome of your project. For instance, PLA is known for its ease of use and environmental friendliness, making it a popular choice for beginners and those looking to create less complex models. On the other hand, ABS offers higher strength and flexibility, which can be beneficial for more advanced projects.
Understanding the nuances of different materials and how they interact with your 3D printer is essential. It helps in achieving the desired results and avoiding common pitfalls such as warping or inconsistent textures. Therefore, taking the time to research and select the most compatible material for your project can set the foundation for a successful 3D printing experience.
What does ‘good’ Filament mean?
Let’s start with the essentials. So what is considered 'good' Filament? Extrusion aims to produce filament that will not cause any printing issues. In this article, we’re not going over end-application properties but rather looking at the filament quality from a processability standpoint. Let’s list it! Good filament should be:
- Homogeneous in composition - This implies the absence of contamination. For blends or composites involving multiple substances, homogeneity also means proper mixing. For instance, in the case of PEEK + Carbon Fiber, the distribution of CF should be equal throughout the whole PEEK matrix. In other words, this means that multiple filament samples extracted from different portions of the spool should be identical.
- Round in cross-section - Ovality is a form of thickness instability. More than a fixed diameter, the 3D printer’s head expects a certain constant volume of plastic to function normally.
- Chemically preserved as much as possible - 3D printing and extrusion both degrade the molecules of polymer, mainly via a mechanism called “chain scission.” It is impossible to preserve 100% of the molecular integrity during extrusion, but the goal is to maintain most properties as much as possible or at least avoid major degradation (plastic burning).
- Constant enough in diameter - It is impossible to produce a spool of filament, guaranteeing that 100% of its points are exactly 1.75mm or 2.85mm. Thickness fluctuation is unavoidable but must be minimized.
The Ideal Extrusion Process
To manufacture premium quality filament, the extrusion process must be executed flawlessly. Each minute aspect of the filament creation process significantly influences the ultimate quality of the filament and necessitates meticulous control.
Let's delve deeper into the intricacies of the extrusion process, distinguishing between the internal mechanisms of the extruder and the subsequent external procedures.
Inside the Extruder: The Barrel and Screw
At the heart of the extruder lies a sophisticated mechanism involving a rotating screw housed within a barrel. This core component serves two primary functions: facilitating the seamless melting of the plastic and propelling it forward in a consistent manner. The process relies heavily on two heat sources: the conductive heat generated by external heaters and the frictional heat produced internally as the screw rotates within the plastic material.
The barrel of the extruder operates through three distinct zones, each playing a crucial role in the transformation of the plastic:
- Feeding Zone: Here, solid plastic is introduced from the hopper, initiating the forward movement and setting the stage for the subsequent phases.
- Transition Zone: In this phase, the plastic gradually transitions from a solid to a liquid state, setting the stage for the final extrusion.
- Metering Zone: At this stage, the plastic attains a fully liquid state, ready to be extruded smoothly through the nozzle.
Maintaining a harmonious flow through these zones is vital. The plastic should undergo a gradual melting process, neither rapid nor too delayed, to ensure a stable pressure that guarantees uniform filament thickness.
Outside the Extruder: Cooling, Diameter Control, and Spooling
Once a stable flow is achieved at the nozzle exit, several additional steps are essential to transform the raw output into high-quality filament:
- Cooling: This step involves solidifying the output before pulling and spooling. Effective cooling, often facilitated by fans, requires a balanced approach to prevent insufficient cooling or excessive vibration.
- Diameter Control: Regular monitoring of the filament diameter is essential, particularly once the filament has undergone shrinkage post-cooling, to maintain uniformity.
- Spooling: During this phase, the spool functions as a collector of the filament without exerting any pulling force. A specialized component known as the "puller" is entrusted with the task of pulling the filament at a consistent rate.
By adhering to these structured processes, one can produce superior-quality filament, fostering innovation and excellence in 3D printing.
Elevate Your Filament Quality
Unlock the potential of your 3D printing projects with 3devo's Filament Maker. Experience unmatched filament quality and innovation at your fingertips.
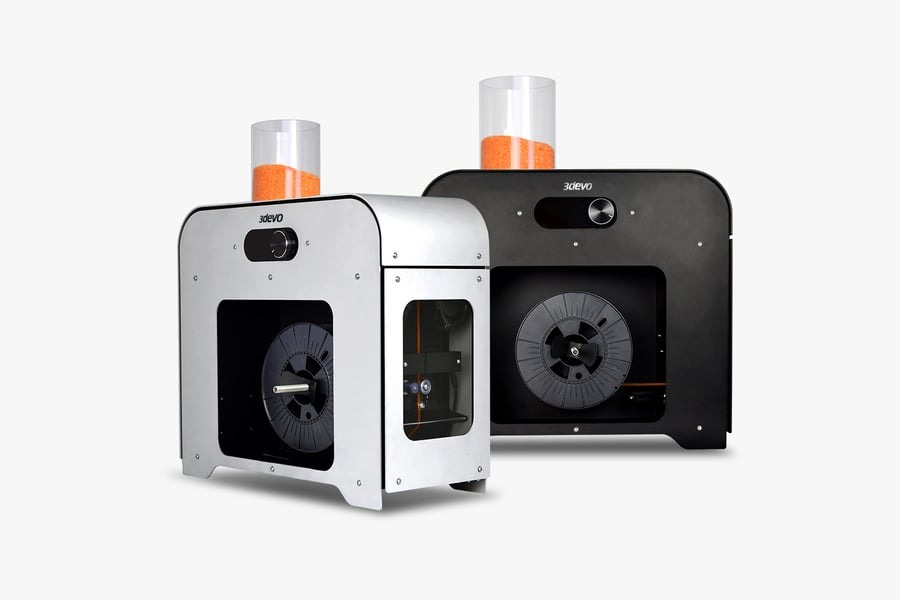
Countless Factors Influence Filament Quality
Every step in the extrusion process matters when making high-quality filament. To get the best results, everything needs to work together perfectly, especially when we focus on two main factors:
- Heater Temperatures
- Screw Speed
But here's the tricky part: these factors are closely linked, which means tweaking them can be a bit of a balancing act.
For instance, when we talk about adjusting the temperatures, it's not just about cranking up the heat. We need to think about which heaters to adjust - the ones closer to the hopper or maybe the ones near the nozzle. Our Filament Maker comes with four heaters, giving us a lot of room to experiment, even though it might make things a bit more complex.
Imagine if we decide to increase the temperature of the first heater, the one near the hopper at the start of the barrel. This means the plastic will carry more heat as it moves through the other heaters, and we'll need to make further adjustments to keep everything balanced.
And here's another thing to consider: what happens if we increase the speed of the screw? On one hand, the material spends less time in the barrel, so it absorbs less heat. But on the other hand, the faster speed creates more friction, which heats up the material. So, changing one setting can have different effects, making the adjustment process a bit challenging.
The key to mastering this process is patience. Since all these settings are interconnected, sometimes we need to make several adjustments to understand the effect of one change. And remember, any change in speed or temperature might also mean we need to tweak the fan cooling settings.
It's all about trial and error and slowly knowing how each adjustment affects the final product. With time and patience, we can fine-tune the process to produce the best possible filament.
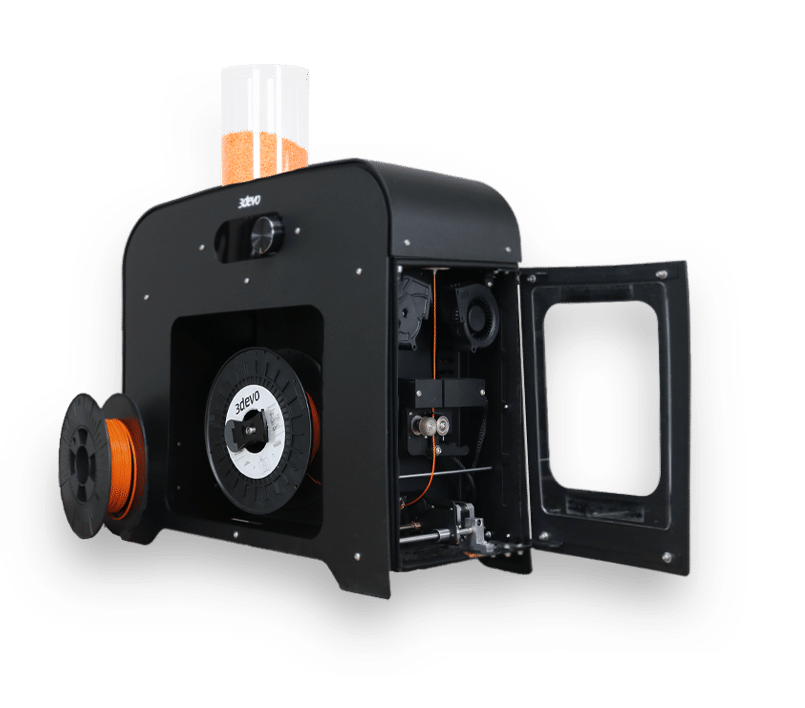
The Role of Environmental Factors
Environmental factors can have a significant impact on the quality of your filament. Elements such as humidity and temperature can alter the properties of the filament, potentially causing issues like brittleness or moisture absorption. These factors can affect the filament both during the printing process and while in storage.
To preserve the quality of your filament, it's essential to store it properly. Consider investing in a dry storage solution to protect your filament from adverse environmental conditions. Additionally, being aware of the optimal printing conditions for different materials can help achieve consistent and high-quality results.
Special factor of influence: the material itself
Some materials are suitable for extrusion, naturally causing fewer extrusion issues. Extrusion grades of polymers often have one property in common: a high viscosity. Others are tricky or even sometimes impossible to shape into filament, typically low-viscosity grades or injection-molding grades.
Choosing the right polymer grade can sometimes prevent issues altogether.
Issue 1: Thickness deviation
This is the most common filament quality issue but also the hardest to troubleshoot. This issue is often resolved last, as filament thickness stability is the ultimate result of the ideal process once all issues have been resolved. Solving excessive thickness deviation is first to solve all other issues and then finetune even more.
Every single box must be ticked:
- Consistent feeding
- Uncontaminated input
- Selecting a polymer grade suitable for extrusion
- Optimal settings
- Good hardware to handle the thickness measurement
- Stable pulling
- Spooling with the right tension
- Proper maintenance and cleaning of the hardware
When speaking of thickness deviation or diameter fluctuation, a key term is “tolerance.” It raises the question: how much can the filament thickness fluctuate and still be considered acceptable? Or how much do you allow your filament thickness to fluctuate?
The most common standard in the industry is +/- 50 micrometers. However, this value is arbitrary. Not all printers require such a tight tolerance. All 3D printers are able to operate without any noticeable negative impact within a certain filament thickness tolerance. +/- 50 micrometers, or 100 micrometers, … It depends on the printer. The reason is that a small melt pool forms itself inside the printhead, acting as a flow buffer. The correct filament thickness average and the absence of huge bumps, however, are essential.
With a research mindset, when exploring numerous novel materials, a small sample of a filament slightly outside tolerance can still be good enough to move forward and run a printing trial.
Issue 2: Bumps or Unmelted Particles
Sometimes, you might notice little bumps or particles that haven't fully melted appearing on the surface of your filament. These tiny troublemakers can cause big headaches during 3D printing, mainly by clogging up the works.
Now, the first thing we need to figure out is what these bumps are made of. Are they bits of the material you're using, or are they something else that's snuck in there?
These "intruders" could be a bunch of things: leftovers from a previous session, bits of plastic or other contaminants, additives, or even small particles that have degraded because they've been in the barrel too long. Sometimes, it might just be a case of the new material still mixing with the old one. If that's the case, it's not a melting issue but more of a cleanliness problem. What is the best way to fix it? Give the barrel a good clean, and start your extrusion test again with nothing but pure, fresh material.
Now, there's a special scenario we need to talk about: additives. Sometimes, tiny fillers like carbon nanotubes can clump together to form small balls. This isn't a melting or purity issue but more about making sure these additives are evenly spread out.
If the bumps are just bits of the material that haven't melted properly, then it's time to play around with the settings. To encourage better melting, you might try upping the temperature for more heat or increasing the rotation speed to create more friction. It's all about finding that sweet spot to get your filament right.
Issue 3: Bubbles in the Filament
Bubbles in the filament can be a significant hindrance, creating voids that lead to failed prints and clogged printheads. The primary cause of these bubbles is inadequate drying before the extrusion process. Many plastics are hygroscopic, absorbing water readily. When these undried plastics are extruded, the internal water content boils, forming bubbles. Moreover, heating plastic in the presence of water can initiate hydrolysis, a chemical process that breaks down the molecules and alters the plastic's properties. Different plastics require varying drying durations, with nylons needing extensive drying time compared to other polymers. The moisture content can be measured using specialized devices to ensure optimal drying.
Another cause of bubbles is degradation during extrusion, which can occur even with hydrophobic polymers or adequately dried hygroscopic polymers. Overheating can lead to symptoms like excessive fluidity, nozzle dripping, sticky output, and discoloration. If you notice these signs, it's time to lower the temperatures to prevent bubble formation.
Issue 4: Insufficiently Liquid Extrusion Output
Sometimes, the filament doesn't melt adequately before exiting the nozzle, leading to potential clogs and other complications. If the output is too solid, it becomes challenging to manage and control its dimensions accurately. To remedy this, consider increasing the process temperatures slightly. However, be cautious, as excessive heat can introduce other issues, including a foggy appearance or buildup at the nozzle tip. In extreme cases, the Filament Maker might clog, sometimes irreversibly. Therefore, monitoring metrics like motor current is essential to prevent excessive pressure in the system.
Special note on fillers: they can exhibit unusual behavior during the process. In a composite material, the polymer melts and acts as a liquid, while the additive remains solid, creating a hybrid output with both liquid and solid components.
Issue 5: Overly Liquid Extrusion Output
On the other hand, the filament can sometimes be too liquid, a characteristic often intrinsic to the material grade. Some grades, designed primarily for injection molding, are naturally more fluid. If you find the output too liquid, a viable strategy is to gradually reduce the processing temperatures. This approach is generally safer compared to dealing with an excessively solid output, which can result in clogs.
A special note on recycling: Each time a polymer undergoes processing, it degrades slightly, becoming more fluid due to a decrease in molecular weight. This means the processing conditions might vary for different cycles of the same material, typically requiring a reduction in temperatures with each recycling occurrence.
I hope this version is more to your liking. Let me know if there are any other adjustments or additions you'd like to see.
The Importance of Regular Maintenance
Regular maintenance is crucial in the filament production process. It goes beyond just keeping the equipment running smoothly; it's about ensuring the consistent quality of the filaments you produce. From keeping an eye on the granulation process in the GP20 Shredder to optimizing the performance of the Filament Extruder, every detail counts.
At 3devo, we've crafted our Filament Maker to be a reliable tool in this process, offering a user-friendly platform where maintaining the quality of your filaments is as simple as creating them. Regular upkeep helps prevent defects and inconsistencies in the filament, leading to better results in the final products.
Remember, maintaining your filament production setup is not just about extending the life of your equipment; it's about encouraging innovation and advancing the possibilities in 3D printing. Experience the difference with 3devo's Filament Maker, your ally in achieving top-notch filament quality.
Conclusion
In conclusion, understanding and troubleshooting common filament defects are essential skills for anyone involved in 3D printing and filament production. Ensuring that your filament meets the criteria of being homogeneous, round in cross-section, chemically preserved, and constant in diameter is fundamental to achieving successful 3D prints.
We've explored various filament quality issues, including thickness deviation, unmelted particles or bumps, bubbles, extrusion output issues, and the influence of the material itself. While these challenges can be complex and interconnected, they are not insurmountable. With patience, experimentation, and a research-oriented mindset, you can identify the root causes of these issues and implement effective solutions.
It's important to remember that filament quality is a multifaceted process that involves careful control of extrusion parameters, material selection, and equipment maintenance. As you delve deeper into 3D printing and filament production, you'll discover that attention to detail and a thorough understanding of each process component will lead to consistent and high-quality results.
In future articles, we'll delve into each of these filament quality issues in greater detail, providing you with practical guidance and solutions to help you overcome them. Whether you're a novice or an experienced 3D printing enthusiast, the journey toward mastering filament quality is a rewarding one, as it opens the door to limitless possibilities in the world of additive manufacturing. Stay tuned for more insights and expert tips to enhance your 3D printing experience.
FAQ
When we say a filament is "homogeneous in composition," we mean that it is consistent throughout, without any impurities or variations in its structure. This ensures that the filament will melt evenly during the 3D printing process, resulting in a smoother and more reliable print. If you're experimenting with blends or composites, the different components are mixed thoroughly, providing uniform properties throughout the filament.
Regular maintenance is crucial to ensure the consistent quality of the filaments you produce. It helps prevent defects and inconsistencies in the filament, which can lead to issues during 3D printing. By maintaining your equipment properly, you can extend its lifespan and encourage innovation in 3D printing, achieving better results in your final products.
Selecting the right material is a vital step in achieving successful 3D prints. Consider the properties of different materials and how they align with your project requirements. For instance, PLA is a popular choice for beginners due to its ease of use and environmental friendliness, while ABS offers higher strength and flexibility for more advanced projects. Understanding the nuances of different materials and their compatibility with your 3D printer can help in achieving the desired results.
Signs of filament degradation can include changes in color, increased brittleness, or a noticeable difference in the texture of the filament. If you suspect your filament has degraded, test it on a small scale before using it for a significant project to avoid potential issues during printing.
Recycling failed prints or leftover filament scraps is a sustainable practice that can help you reduce waste. You can use devices like a filament recycler to grind down the scraps and remold them into new filament. However, remember that each recycling cycle might alter the material properties slightly, so adjustments to your printing settings may be necessary.
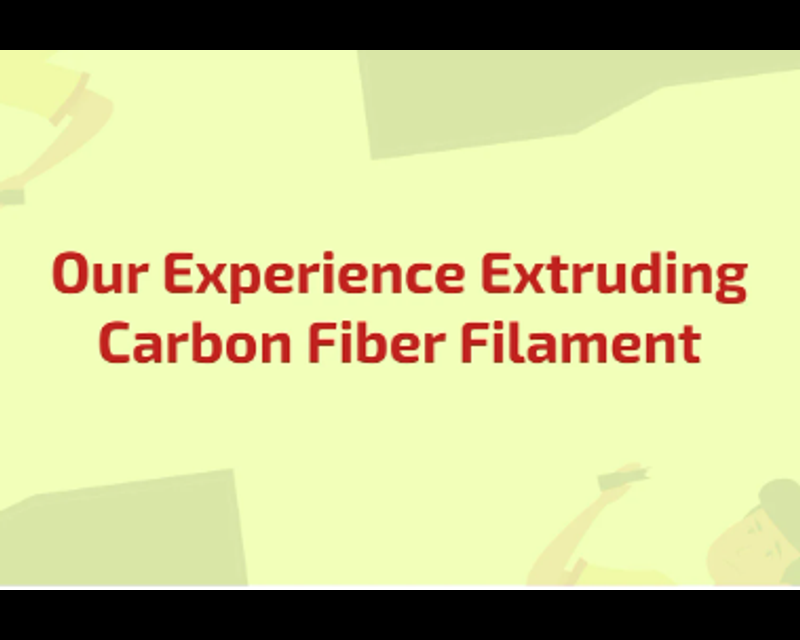
Dive Deeper into Carbon Fiber Extrusion
Ready to embark on your carbon fiber filament journey? Discover valuable insights and guidance from our recent exploration into the realm of carbon fiber filament extrusion.
%20-%20instasize%20(1)%20-%20instasize%20(1).png?width=800&height=640&name=PETG-e1494958102567%20(1)%20-%20instasize%20(1)%20-%20instasize%20(1).png)
Unlock the Secrets to Material Selection
Dive into our Complete Material Selection Guide to find your perfect fit hassle-free. Get started with your innovation journey here!
%20-%20instasize%20(2).png?width=800&height=640&name=MicrosoftTeams-image%20(39)%20-%20instasize%20(2).png)
Navigate the World of Polymers with Expert Guidance
Ready to elevate your project with the perfect material? Our Polymer Pyramid is designed to help you pinpoint the right polymer with ease.
Share this
- March 2025 (1)
- January 2025 (1)
- December 2024 (2)
- November 2024 (3)
- October 2024 (4)
- September 2024 (2)
- August 2024 (3)
- July 2024 (6)
- June 2024 (3)
- May 2024 (2)
- April 2024 (1)
- March 2024 (1)
- January 2024 (1)
- November 2023 (2)
- October 2023 (5)
- September 2023 (2)
- August 2023 (1)
- July 2023 (1)
- May 2023 (1)
- December 2022 (3)
- August 2022 (1)
- June 2022 (1)
- May 2022 (2)
- April 2022 (2)
- March 2022 (7)
- February 2022 (2)
- January 2022 (3)
- December 2021 (3)
- November 2021 (3)
- October 2021 (2)
- September 2021 (3)
- August 2021 (3)
- July 2021 (2)
- June 2021 (1)
- March 2021 (1)
- October 2020 (1)
- June 2020 (1)
- May 2020 (1)
- April 2020 (4)
- November 2019 (1)
- July 2019 (2)
- June 2019 (1)
- May 2019 (1)
- March 2019 (1)
- November 2018 (1)
- September 2018 (1)
- January 2018 (1)
- October 2017 (1)
- September 2017 (1)
- July 2017 (1)
- June 2017 (1)
- May 2017 (1)
- January 2017 (1)
- December 2016 (3)
- November 2016 (2)
- October 2016 (1)
- May 2016 (2)
- August 2015 (2)
- July 2015 (1)