Share this
How to Recycle PS Spools into 3D Prints: A DIY Guide
by Louis Rinaldo on Oct 6, 2023 2:31:13 PM
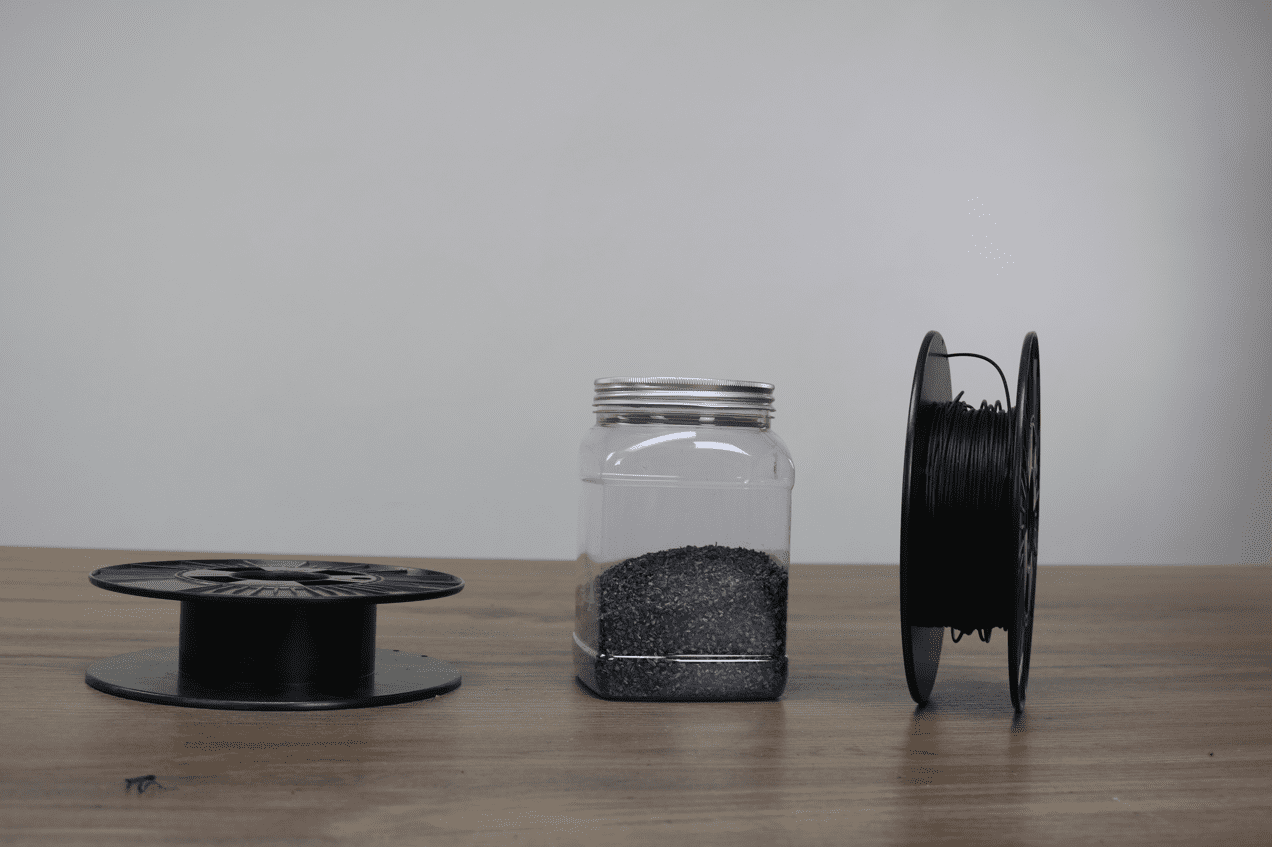
Introduction
Did you know that the empty PolyStyrene (PS) spools from your 3D printing projects are actually hidden treasures waiting to be unlocked?
3D printing filament spools are the unsung heroes of the 3D printing ecosystem, especially the PolyStyrene (PS) spools that we primarily use at 3devo. These spools not only hold the filament but also represent an untapped goldmine for recycling. From support structures to failed prints, there's a lot of material that can be turned back into valuable filament. But have you ever stopped to think about the spools themselves? They often end up as waste, and that's what we're tackling head-on. We've found that these PS spools can be transformed into high-quality filament, opening up a whole new avenue for recycling.
Embark on this technical journey with us as we navigate the complexities of turning empty PS spools into reusable filament and, eventually, 3D-printed items. We'll cover every step of the process, from shredding and filament-making to troubleshooting and printing. Get ready to absorb in just 5-15 minutes what took us several days of rigorous experimentation. So, buckle up and dive into this exciting adventure of giving new life to what would otherwise be waste.
Part 1: About the Input Material
The Diversity of 3D Printing Spools
3D printing filament spools are like the unsung heroes of the 3D printing world. They come in a variety of materials, including cardboard, metal, polypropylene, and PolyStyrene (PS). Each material has its own set of advantages and disadvantages, but for the purpose of this guide, we're zeroing in on PS spools. These are the spools we predominantly use at 3devo, and they're abundant wherever 3D printing filament is used. Surprisingly, these omnipresent spools can be transformed into filament of exceptional quality. So, let's embark on a journey to create a "spool of spools."
What's Special About PS?
It's important to note that not all PS is created equal, and understanding the nuances is crucial for successful recycling. Solid PS, the material from which these spools are made, is a thermoplastic polymer known for its rigidity, excellent electrical insulation, and ease of injection molding. This sets it apart from Styrofoam, which is a type of expanded PS. Styrofoam is filled with air and has a foam-like structure, making it unsuitable for recycling due to its high air content. In contrast, solid PS offers a range of mechanical properties, including strength and durability, that make it an intriguing candidate for our recycling project. It's this form of PS that we've focused on to unlock its potential for a second life as high-quality filament.
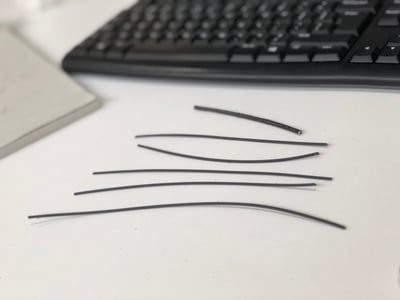
The Challenge of Injection-Molded PS
Now, let's talk about the elephant in the room: the injection molding process. PS spools are usually injection-molded, a process that, in theory, makes them unsuitable for extrusion. Why? Because the fluidity of the material used in injection molding is different from that used in extrusion. Injection-molded grades are designed to be more fluid so they can quickly and accurately fill fine molds. Extrusion grades, however, are more viscous, allowing the filament to hold its shape and withstand the tension of spooling.
%20(1).png?width=800&height=640&name=silver-extruder-1%20-%20instasize%20(1)%20(1).png)
How We Made It Work
On paper, it looks like you can't use this kind of PS for extrusion. But we like a challenge! We've figured out how to do it, and we're excited to share that with you. So, even if something seems like it won't work, sometimes you can find a way.
Part 2: Preparing for Extrusion
Preparation can be divided into sub-steps. No detail should be overlooked since the smallest mistake might result in the clogging of the 3D printer.
Secure Storage for PS Spools
The moment a spool runs out, it should be immediately stored in a clean, sealed container. The aim is to prevent any contamination from dust and foreign particles. Contaminants like plastic and non-plastic particles can severely compromise the recycling process. For instance, different polymers like PLA or ABS won't melt properly and could cause issues. Even spools from different brands or other grades of PS can introduce unwanted variability. The goal is straightforward: store only one specific, controlled type of PS spools to maintain material consistency.
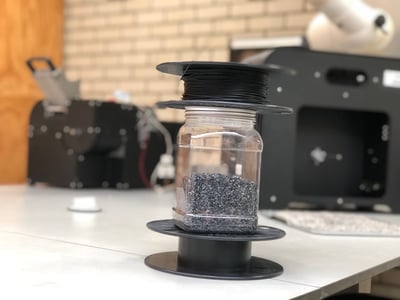
Thorough Cleaning: Remove Stickers and Adhesives
Cleaning is a critical step that should not be overlooked. Stickers, glue, and other impurities must be completely removed before the shredding process begins. If you skip this step, you'll find it nearly impossible to remove these impurities later, especially glue residues. These residues can burn inside the barrel of the Filament Maker, leading to a clogged 3D printer. It's essential to use cleaning agents that are compatible with PS. For example, acetone should be avoided as it dissolves PS. Ethanol is also not recommended. Stick to soapy water for best results. After cleaning, make sure the spools are stored in a way that prevents further contamination.
Pre-chopping and Shredding with the GP20 Plastic Shredder
Not all shredders can handle full-sized spools, especially those designed for laboratory-scale operations. Pre-chopping the spools into smaller pieces (around 7-10cm) is often necessary. Our GP20 Hybrid Shredder is particularly effective for this, reducing the pre-chopped spools first to 8mm and then to 3.5mm particles. It's vital that all particles are uniformly smaller than 4mm, the maximum input size for the Filament Maker. The GP20 Hybrid accomplishes both shredding and granulating in one seamless step.
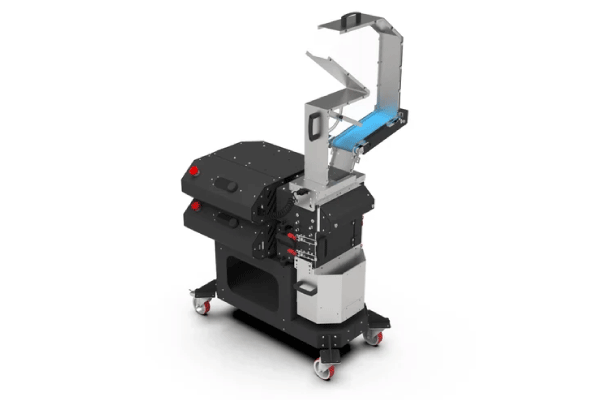
Drying: An Essential Step for Most Polymers
While many polymers are hygroscopic and absorb moisture, PS is an exception. It's hydrophobic, meaning it doesn't absorb significant amounts of moisture. However, any water introduced during the cleaning process should be allowed to evaporate in a "normal" environment before proceeding to the shredding step.
Final Preparations for Extrusion Testing
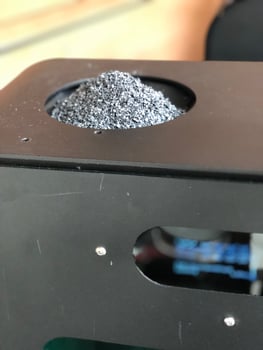
After following these detailed steps, you should have a batch of PS regrind that is dry, clean, and homogeneous, making it ready for extrusion testing.
Join Us at Formnext 2023 for an Exciting New Product Launch!
Join us Nov 7-10 in Frankfurt at booth 12.1 G129 for an exclusive new product reveal. Don't miss out!
.png?width=1200&height=675&name=MicrosoftTeams-image%20(27).png)
Part 3: The First Extrusion Test
When you're introducing a new material like PS into the Filament Maker for the first time, the stakes are high. The goal isn't necessarily to achieve perfect filament quality right off the bat. Instead, the initial objective is to get an output that, while imperfect, doesn't clog the barrel. This gives you the breathing room to fine-tune the settings over time. Think of this phase as exploratory research, where you're gathering data to refine your process.
Setting the Right Temperature: Start Hot, Then Adjust
One of the biggest questions is how to ensure that the PS melts smoothly during its first run through the Filament Maker. A good rule of thumb is to start with a slightly higher temperature than what you think you'll need. After some quick online research, we found that 210°C is generally on the higher end for most grades of PS. Starting hot is a safer bet than starting too cold, as it reduces the risk of clogging and allows for easier adjustments later on.
Other Key Parameters: Screw Speed and Fan Cooling
When it comes to other settings, it's often best to start with average conditions and adjust from there. For instance, a screw speed of 5 RPM is a good starting point. Through our experience, we've found that a range of 3.0-6.0 RPM is generally effective for producing stable 1.75mm filament with the Filament Maker.
Fan Cooling: The Quick-Adjust Parameter
Fan cooling is another crucial parameter, and we usually start with it set at 50%. This is merely a starting point, as fan cooling is the quickest parameter to adjust. It's worth noting that this setting can be influenced by external factors like room temperature and humidity, so keep an eye on those as well.
The Iterative Nature of First-Time Extrusion
The first extrusion test is all about learning and adapting. You start with settings that are safe and give you room to maneuver. Then, as you gather more data, you can fine-tune these parameters to get closer to your ideal filament quality. It's an iterative process that combines both art and science, and it's a critical step in mastering the recycling of PS spools.
Part 4: Filament Extrusion
Transitioning from one material to another in the Filament Maker is a nuanced process that requires a deep understanding of both materials involved. This phase is critical for ensuring a smooth and efficient extrusion process, especially when you're working with complex materials like PS. Let's delve into the intricacies of this crucial step.
The Never-Empty Barrel: A Primer
One of the unique aspects of the Filament Maker is that its barrel is never truly empty, unless you disassemble the entire system and remove the screw. This is because the feeding mechanism is what generates pressure inside the barrel. The moment the hopper runs out of material, the forward conveyance of the molten material comes to a halt. This sets the stage for what we call "transition," which is the process of pushing out one material by feeding in another.
The Art of Transition: Material Compatibility
Transition isn't as simple as just feeding in a new material. Both materials—what's already in the barrel and what you're feeding in—need to have overlapping thermal processing windows. This is because both materials will be melting inside the same barrel simultaneously. At 3devo, we primarily use two purge materials for this purpose: Devoclean MidTemp and HDPE. Both of these materials are compatible with PS due to their wide thermal window, ranging from 190-300°C.
The Ideal Temperature for Transition
Depending on how you concluded your previous extrusion run, your barrel will most likely be filled with either Devoclean MidTemp or HDPE. The good news is that transitioning from either of these materials to PS can be smoothly done at 210°C. However, transitioning from HDPE tends to be a bit easier compared to Devoclean MidTemp, which is more resilient and takes a bit more effort to flush out.
The Real Deal: When PS Takes the Stage
The actual extrusion process kicks off when you see PS material emerging from the nozzle. This is the moment where all your preparation and transition work pays off, and you can begin to focus on fine-tuning the extrusion parameters for optimal PS filament quality.
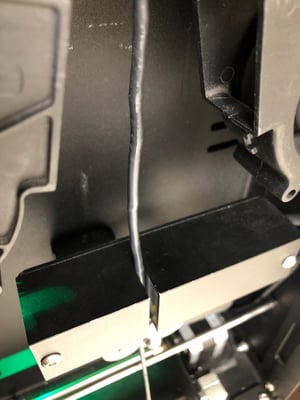
The Iterative Process Continues
Just like the initial extrusion test, the transition phase is also an iterative process. It's about understanding the nuances of material compatibility, thermal windows, and optimal transition temperatures. Mastering this phase is crucial for a seamless and efficient recycling process, especially when dealing with materials like PS.
Part 5: Troubleshooting
Troubleshooting is an inevitable part of any experimental process, and filament extrusion is no exception. When you're working with a material as unique as PS, you're bound to encounter some challenges that require a bit of problem-solving. This section is dedicated to helping you navigate those challenges, offering insights into how to fine-tune the extrusion process for optimal results.
First Observations and Initial Challenges
Once the transition phase is complete, which usually takes around 20 minutes, you might find that the first output isn't quite up to snuff for spooling. While the flow may appear stable, fully molten, and free of impurities and bubbles, you could face issues with the extrudate's consistency. Specifically, it might be too liquid when it reaches the puller, causing it to flatten between the wheels. This is a common issue, especially when working with new materials, and it's crucial to address it promptly to avoid further complications.
The Role of the Filament Sensor in Troubleshooting
The Filament Maker comes equipped with an optical sensor that plays a crucial role in troubleshooting. This sensor measures the filament's thickness every second and calculates a 20-second average. It then compares this average to the setpoint, which could be 1.75mm, 2.85mm, or any other diameter of your choosing. Based on this comparison, the sensor adjusts the stretching speed and repeats this loop continuously. This real-time feedback mechanism allows for quick adjustments and helps in achieving a stable and consistent filament output.
Achieving Optimal Extrusion Settings
The primary objective here is to find the optimal extrusion settings with the help of the filament sensor. Because the flow was very stable, the challenge was to ensure that the extrudate was fully solidified before reaching the puller without disturbing the flow or creating instabilities. This is a delicate balance and may require several iterations to get right. But with the real-time data from the filament sensor, you're well-equipped to make these fine adjustments.
By following these troubleshooting steps and understanding the role of each component in the Filament Maker, you should be well on your way to achieving a dry, clean, homogeneous, and fine-enough batch of regrind that's ready for extrusion testing.
Part 6: Filament Extrusion: Fine-Tuning
Fine-tuning your filament extrusion process is akin to a craftsman perfecting their art. It's not just about getting the machine to work; it's about optimizing every little detail to achieve a masterpiece. In this part, we'll explore how to meticulously fine-tune your Filament Maker settings to produce top-notch PS filament.
The Role of Fan Speed in Filament Quality
Fan speed is a crucial parameter when it comes to filament quality. After several tests, we found that a fan speed of around 100% was optimal for achieving the best quality. This high speed ensures that the filament is adequately cooled as it exits the extruder, contributing to its overall structural integrity.
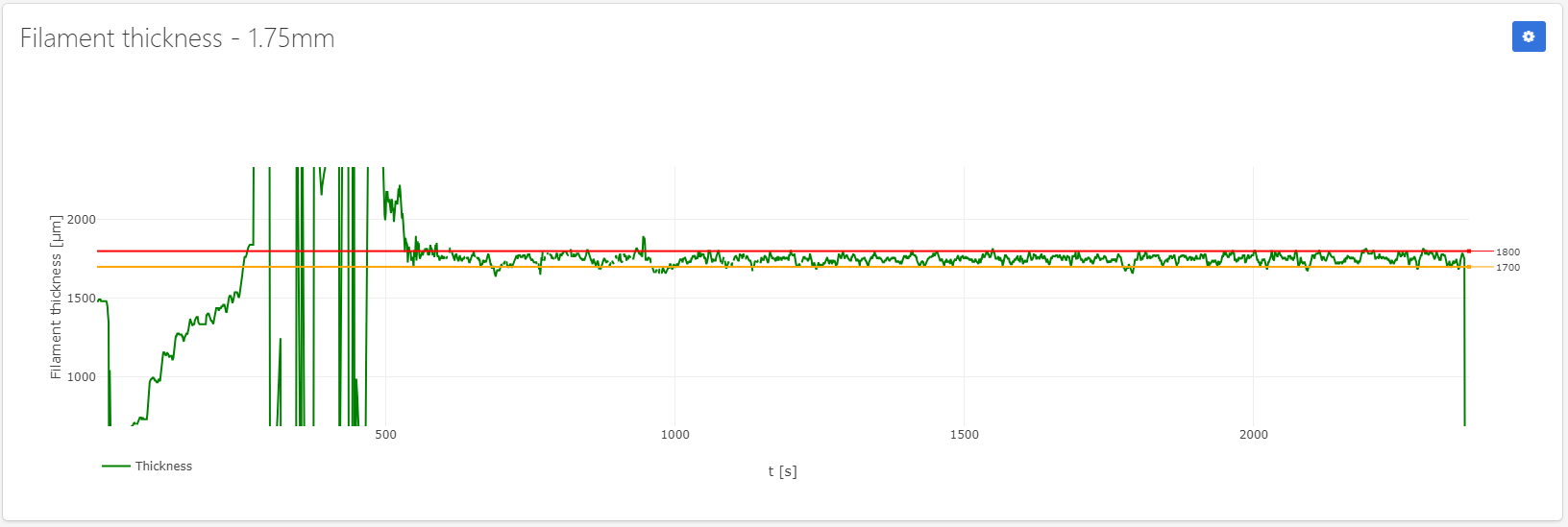
The Importance of Screw RPM
Screw RPM is another key factor that affects the flow rate and internal pressure of the barrel. We found that slightly reducing the screw speed to 4.5 RPM was beneficial. This adjustment allows the extrudate more time to be cooled by the fans, leading to a more stable and high-quality filament.
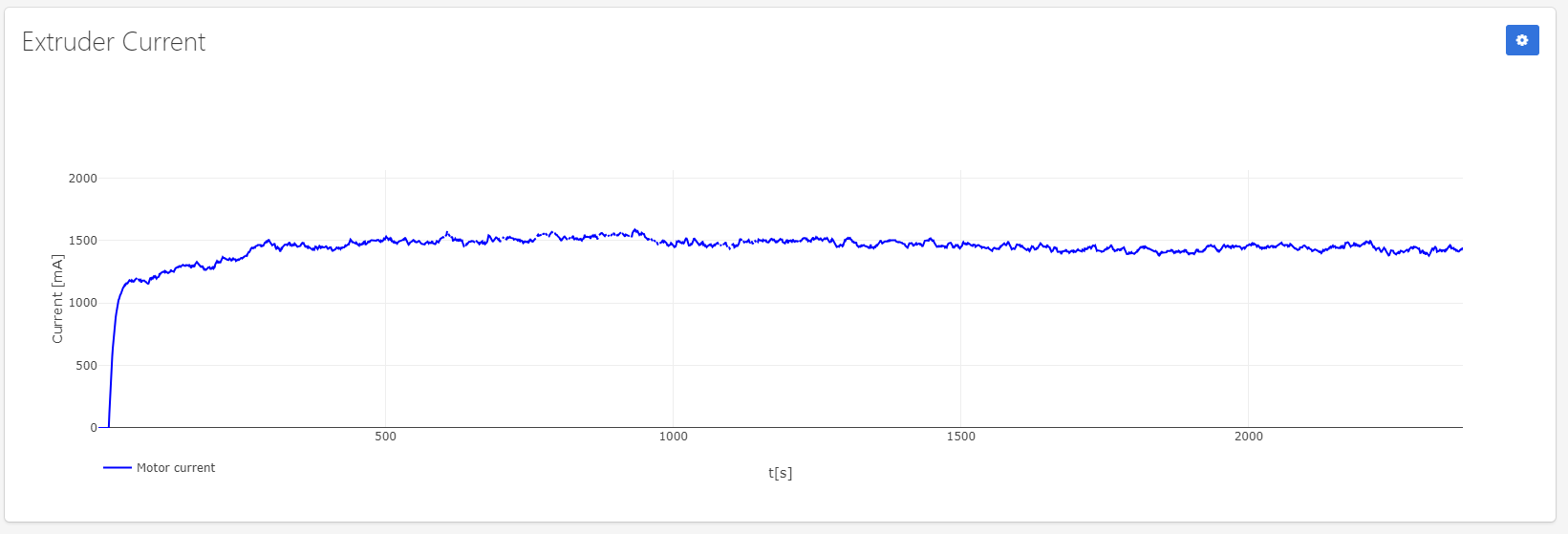
Temperature Management: A Delicate Balance
Temperature plays a critical role when working with PS. It's essential to maintain high enough temperatures to prevent clogging but not so high that it compromises the filament's quality. We slightly lowered the temperatures by 5°C to 10°C to facilitate easier cooling of the filament. Additionally, we used an ascending thermal profile ranging from 200°C to 210°C to enhance the flow's stability and allow for a gradual build-up of pressure inside the barrel.
Real-Time Monitoring with DevoVision
Throughout the fine-tuning process, we closely monitored various parameters using our data-logging software, DevoVision. We paid special attention to the motor current, puller speed, and filament thickness to ensure stability and make quick adjustments as needed.
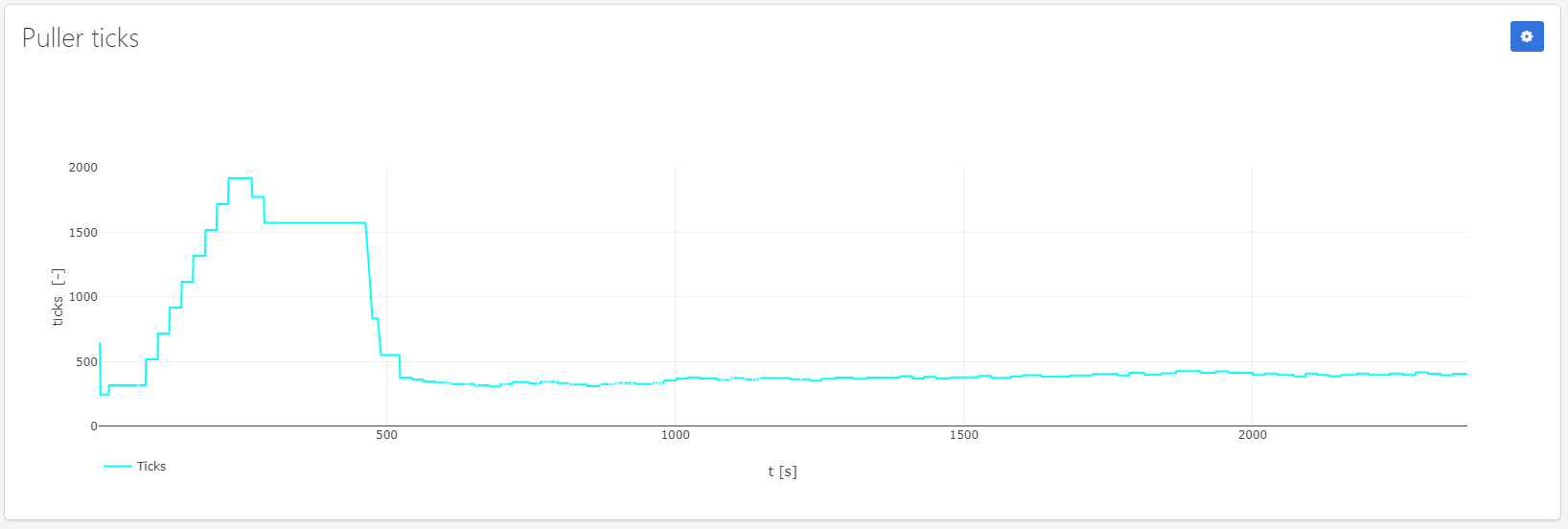
Initiating the Spooling Process
Once we were confident that the filament quality was stable for over 30 minutes, we initiated the spooling process. This involves following the spooling wizard, manually guiding the filament through the spool's hole, and adjusting the spool tension for a neat, tight wind.
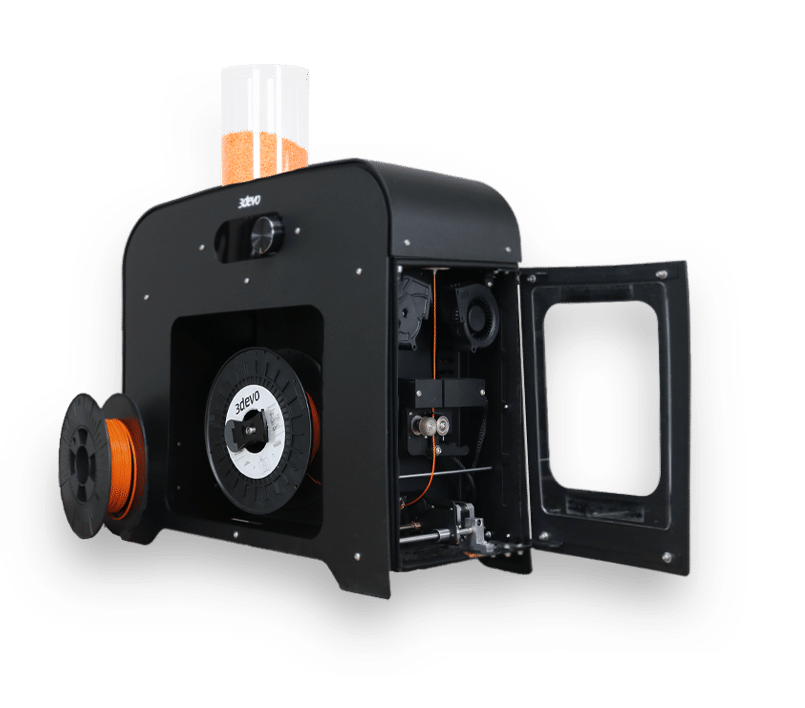
Part 7: Maintenance and Quality Checks
Maintaining your Filament Maker is not just about cleaning and storing; it's about ensuring that the machine performs optimally every time you use it. In this section, we'll guide you through the essential maintenance steps to keep your Filament Maker in top condition.
Purging: An Essential End-of-Session Task
Purging the Filament Maker at the end of each extrusion session is a non-negotiable step for two primary reasons:
- Contamination Removal: Over time, unmelted particles and contaminants can accumulate inside the barrel. Purging helps to remove these elements, ensuring a cleaner extrusion process in future sessions.
- Polymer Degradation Prevention: When you shut down the extruder, it takes over an hour to cool down to room temperature. Most polymers degrade when exposed to heat for such extended periods. Purging with a transition material like Devoclean MidTemp helps to avoid this degradation, setting the stage for successful extrusions in subsequent sessions.
Monthly Quality Checks: The Filament Maker's Health Report
It's advisable to conduct a standard quality check (QC) on your Filament Maker every month. This involves producing a spool of standard PLA filament using standard settings and pellets. If the machine struggles to produce a perfect spool under these basic conditions, it's an indicator of a deeper, underlying issue that needs attention.
Spare Parts: The Unsung Heroes
While the Filament Maker is built to last, wear and tear are inevitable over time. For instance, the nozzle may get partially clogged, or the rubber puller wheel might show signs of grooving or roughness. Fortunately, these parts are easily replaceable, ensuring that you can quickly get back to producing high-quality filament.
By adhering to these maintenance practices, you not only extend the lifespan of your Filament Maker but also ensure consistent, high-quality filament production.
Part 8: The 3D Printing Journey
3D printing, much like extrusion, is an experimental process that often involves a bit of trial and error. In this final section, we'll share our experiences and insights into achieving optimal 3D print quality using the filament you've just created.
The Initial Hurdles: Setting the Stage
We initially started with "standard" PS printing settings that we found online, which included a printhead temperature of 230°C and a bed temperature of 90°C. However, we encountered an issue with poor bed adhesion.
Problem-Solving: Adjustments and Tweaks
To tackle the adhesion issue, we took the following steps:
- Temperature Adjustment: We increased the printing temperature to enhance the filament's adhesion to the bed.
- Cooling Shutdown: We turned off all cooling mechanisms to ensure that the filament adhered better to the bed.
- Glue Galore: We applied a generous amount of glue to the build plate to further improve adhesion.
These adjustments were sufficient to successfully print a small, simple item.
The Iterative Process: Continuous Improvement
The quality of 3D printing can always be refined and improved. The key is to be willing to invest the time and effort into trying out various settings combinations. Don't be afraid to experiment; each trial brings you one step closer to perfecting your 3D print settings.
By following this guide, you'll be well-equipped to navigate the complexities of 3D printing with your newly created filament. Remember, the journey to perfection is iterative, and each step you take brings you closer to achieving your 3D printing goals.
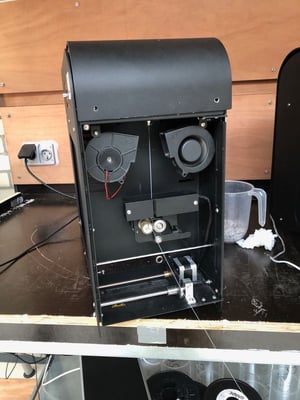
Conclusion: High-Quality PS Filament for 3D Printing
In this comprehensive guide, we've journeyed through the intricate process of converting PS spools into high-quality 3D printing filaments. From the initial steps of preparation and extrusion testing to the nitty-gritty details of fine-tuning and 3D printing, this exploration has been both enlightening and rewarding.
Key Takeaways: Lessons Learned
We've learned some important lessons along the way:
- Meticulous Preparation: The importance of thorough preparation to avoid contamination cannot be overstated.
- Material Transition: Understanding and executing material transition is crucial for continuous and smooth extrusion.
- Parameter Fine-Tuning: Adjusting parameters meticulously is essential for achieving optimal filament quality.
- Maintenance and Quality Checks: Regular upkeep and quality assessments are vital for ensuring consistent results over time.
Practical Tips: Your To-Do List
Here are some specific tips to keep in mind:
- Keep the temperature around 205°C for the best filament quality.
- Always purge the machine before and after extrusion. This helps to avoid any contamination or mixing of materials.
- When you're switching materials, make sure to use Devoclean MidTemp. It makes the transition smoother and avoids any issues.
Warnings: Things to Watch Out For
And a few warnings:
- You might need to adjust the fan speed, especially if you're working in a room that's particularly hot or cold.
- If the filament is coming out too soft and getting squished, you'll need to adjust the machine's speed.
- Never leave any PS in the machine when you're done. The only material that should be left in a machine that's not in use is Devoclean MidTemp.
Final Thoughts: The Next Steps
So, what's next? This guide is just the beginning. With some attention to detail and a willingness to get your hands dirty, you can turn everyday PS spools into high-quality 3D printing filament. It's a rewarding process that not only saves money but also opens up new possibilities for 3D printing projects. Keep experimenting, keep refining, and most importantly, keep printing.
FAQ
Recycling PS (PolyStyrene) spools is not just an eco-friendly practice but also a cost-effective way to source material for 3D printing. PS is a thermoplastic polymer known for its rigidity and excellent electrical insulation properties. It's often used in injection molding, making it abundant in the form of 3D printing spools. By recycling these spools, you can create a closed-loop system in your lab or R&D facility, reducing waste and material costs. Moreover, PS has a unique set of mechanical properties, including high tensile strength and durability, making it an intriguing candidate for various applications.
Certainly! Blending PS with other polymers opens up a world of possibilities for material innovation. By carefully selecting compatible materials, you can create custom filaments with tailored mechanical and thermal properties that meet specific application needs. While it's true that different polymers have varying melting temperatures and mechanical characteristics, this diversity is actually an advantage. It allows you to fine-tune your filament for optimal performance in specialized applications.
The key to successful blending lies in understanding material compatibility. By conducting comprehensive material characterization tests, such as rheological and tensile tests, you can unlock the full potential of blended filaments. These tests ensure that you achieve consistent extrusion, strong layer adhesion, and enhanced mechanical strength, setting the stage for groundbreaking applications in your R&D projects or academic research.
So, if you're considering blending PS with other polymers, you're essentially stepping into an exciting realm of material science, one that offers endless opportunities for innovation and customization.
Recycled PS filament can achieve comparable mechanical properties to commercial filament if processed correctly. The key factors include ensuring the material is free from contaminants, optimizing extrusion parameters, and conducting post-extrusion annealing if necessary. Material characterization tests such as tensile strength, elongation at break, and impact resistance can be conducted to compare the recycled and commercial filaments. It's also advisable to use techniques like Differential Scanning Calorimetry (DSC) to assess the material's thermal properties.
Recycling PS spools contributes to sustainability by reducing the need for virgin material production, which involves petrochemical processes. It also minimizes waste going into landfills. PS is not biodegradable and can take hundreds of years to decompose. By recycling, you're effectively reducing the carbon footprint of your operations. For institutions and companies with sustainability goals, this can be a significant contribution.
Yes, there is a growing market for recycled filament, especially in niche sectors that value sustainability and material traceability. However, selling recycled filament comes with its own set of challenges, including quality assurance and regulatory compliance. It's essential to have a robust quality control system in place, complete with material characterization and batch-to-batch consistency checks. Certifications may also be required, depending on the industry you're targeting (e.g., medical, aerospace).
Explore More: Your Guide to Sustainable Recycling
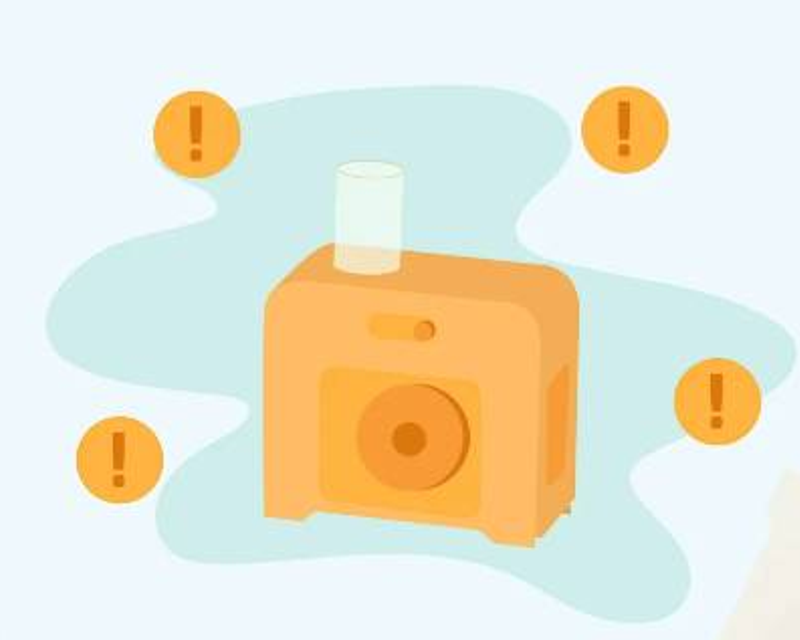
Extrude Plastic Waste Into Filament
Learn How to Extrude Plastic Waste into Filament Now!
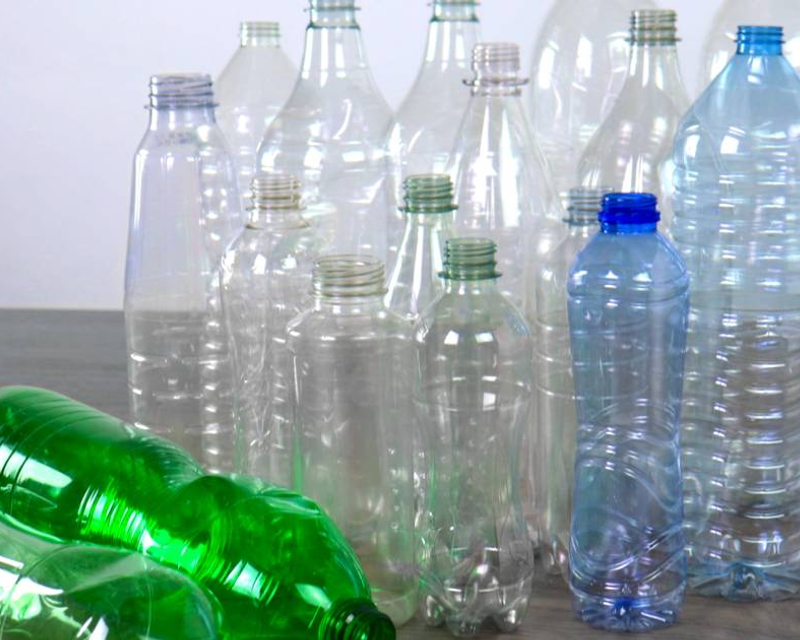
PET Recycling - From Bottle to Filament
From Bottle to Build: Discover the Journey of PET Recycling into 3D Filament!
%20-%20instasize%20(2).png?width=800&height=640&name=MicrosoftTeams-image%20(39)%20-%20instasize%20(2).png)
Navigate the World of Polymers
Unlock the Perfect Material for Your Project: Dive into Our Polymer Pyramid Today!
Share this
- March 2025 (1)
- January 2025 (1)
- December 2024 (2)
- November 2024 (3)
- October 2024 (4)
- September 2024 (2)
- August 2024 (3)
- July 2024 (6)
- June 2024 (3)
- May 2024 (2)
- April 2024 (1)
- March 2024 (1)
- January 2024 (1)
- November 2023 (2)
- October 2023 (5)
- September 2023 (2)
- August 2023 (1)
- July 2023 (1)
- May 2023 (1)
- December 2022 (3)
- August 2022 (1)
- June 2022 (1)
- May 2022 (2)
- April 2022 (2)
- March 2022 (7)
- February 2022 (2)
- January 2022 (3)
- December 2021 (3)
- November 2021 (3)
- October 2021 (2)
- September 2021 (3)
- August 2021 (3)
- July 2021 (2)
- June 2021 (1)
- March 2021 (1)
- October 2020 (1)
- June 2020 (1)
- May 2020 (1)
- April 2020 (4)
- November 2019 (1)
- July 2019 (2)
- June 2019 (1)
- May 2019 (1)
- March 2019 (1)
- November 2018 (1)
- September 2018 (1)
- January 2018 (1)
- October 2017 (1)
- September 2017 (1)
- July 2017 (1)
- June 2017 (1)
- May 2017 (1)
- January 2017 (1)
- December 2016 (3)
- November 2016 (2)
- October 2016 (1)
- May 2016 (2)
- August 2015 (2)
- July 2015 (1)