Share this
The Filament Maker Story: Past, Present, and Future
by Gigi Palczer on Oct 26, 2023 2:57:59 PM
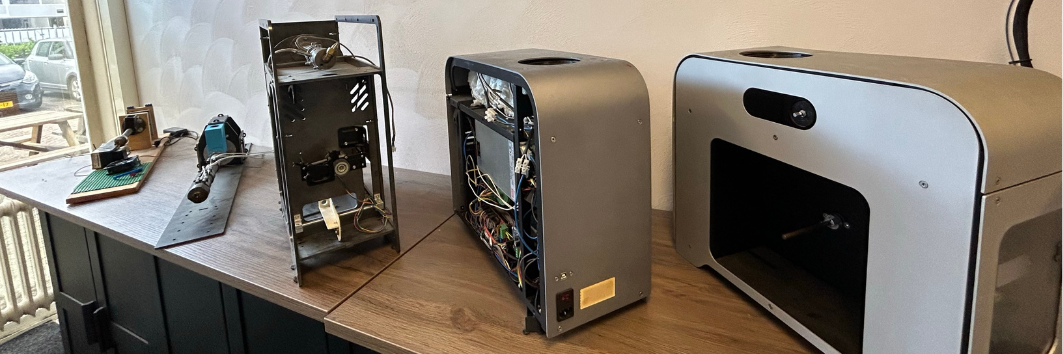
Introduction
Our clients are never content with the status quo; they're always on the hunt for the next big thing. To ensure we're keeping pace and aiding their innovative efforts, we continually update and refine our tools and methods.
In this blog post, you'll get a detailed look at how our Filament Maker has grown and adapted. We've listened to your feedback and made adjustments so that the Filament Maker can be an even more effective tool for your innovative projects. So, let's dive into the journey of our Filament Maker and see how it's been fine-tuned to help you achieve your goals.
2015: Where it all started
Our very first extruder prototype was hand-crafted by our CEO Tim Wesselink, in 2015. Can you guess what it was made of?
Wood. Cardboard. Toy bricks from our childhood favorite brand. Only one heater.
This humble beginning set the stage for what was to come. Tim believed in this proof of concept so much that he founded an entire company around it. Already then, we knew that 3D printing innovators were in dire need of a tool to make their own filament. This would become the only way to push the boundaries of how materials can traditionally be processed.
With a little more than this fragile prototype, innovators would soon achieve great things.
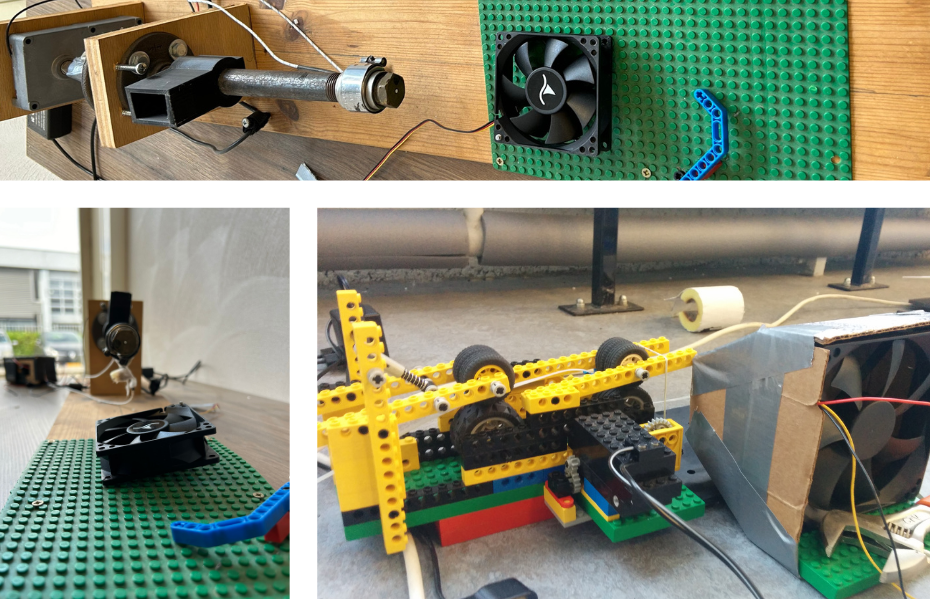
The flow
Conventional extrusion lines are segmented into a sequence of steps:
- Feeding
- Melting & Pushing
- Cooling
- Dimensional control (thickness sensor)
- Spooling
These steps are often organized as a horizontal line, spread over a long distance.
How can a filament production line be as compact as the Filament Maker? Thanks to the flow of the machine.
First, the material travels through a horizontal barrel. At the end of it, a knee transforms the horizontal melting flow into a vertical cooling path. A positioner then bends the product horizontally again, toward and onto the spool. The spool takes up the remaining central space of the apparatus.
The circular flow has always been the key design element.
The curve
The Filament Maker is renowned for its sleek design. Its all-in-one, compact process even includes the spooling step, when conventional machines would require very long cooling/spooling lines. The Filament Maker allows the user to walk through a complete sequence of research and manufacturing steps, in limited time and space.
This contained workflow translates into one cool detail: the curve of its hood.
This curve symbolizes how neatly the device is built and how smooth it makes the extrusion process. The story behind it is awesome, too. The curve happens to come from another device: a fire extinguisher. That’s right.
The first panel was manually bent around a fire extinguisher. Now more professionally crafted, the top hood of the Filament Maker retains the exact same original, smooth bend.
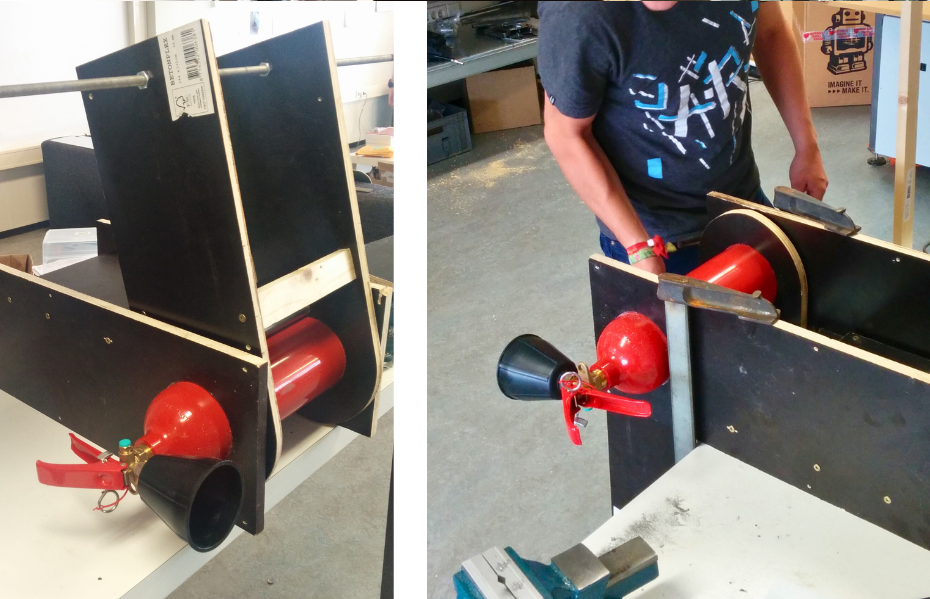
2016: From 3 to 4 heaters
In the last months of 2016, we proudly sold our first inaugural machine, marking a significant milestone in our evolution.
The Filament Maker was initially equipped with 3 heaters. This was enough to explore multiple materials. Delving deeper into material science, a fourth heater would soon be necessary to improve process stability and give more finetuning options.
The key to achieving stable filament thickness is not only melting the polymer but also controlling the melting and pressure inside the barrel. The material should neither melt too soon nor too late. Placing 4 heaters along a 30cm long barrel is the only way to ensure gradual melting in the different zones of the barrel (feeding, transition, metering).
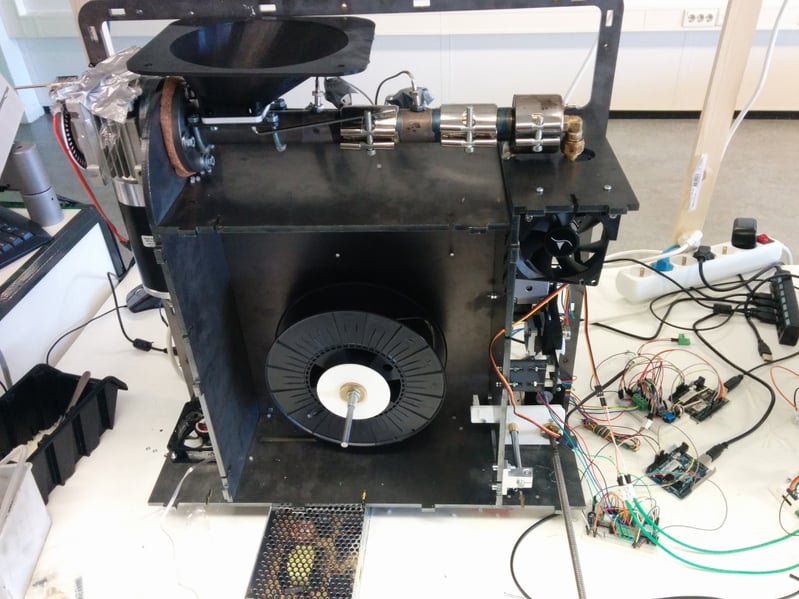
Insulation
Fancy heaters are of no use if the heat does not remain inside the barrel where plastic flows. For that reason, we worked hard on insulating the extrusion system with different types of insulation wools and bands.
One of the challenges is to insulate not only the core of the barrel but also the knee and nozzle at one end of it.
For ease of reparation and optimal heat insulation, our current design contains glass wool and metal tie wraps. Process stability is enhanced whereas risks of short-circuiting and heat loss are minimized.
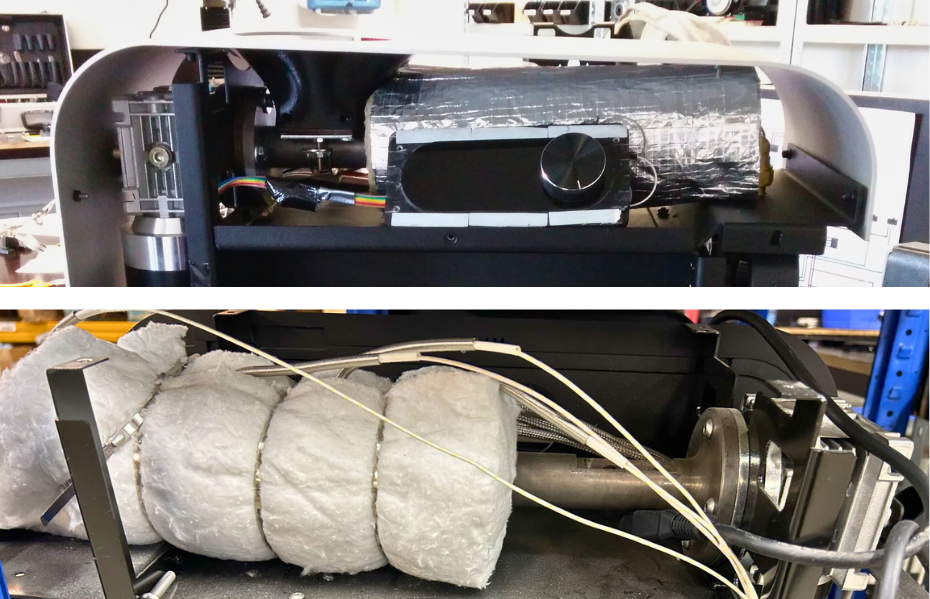
Speaking of panels, again
Not only should the Filament Maker be a potent tool, not only should it look nice and neat, but it should also do it all durably. We transitioned from anodized panels to the reliability of powder coating, ensuring a more resistant finish for all machines.
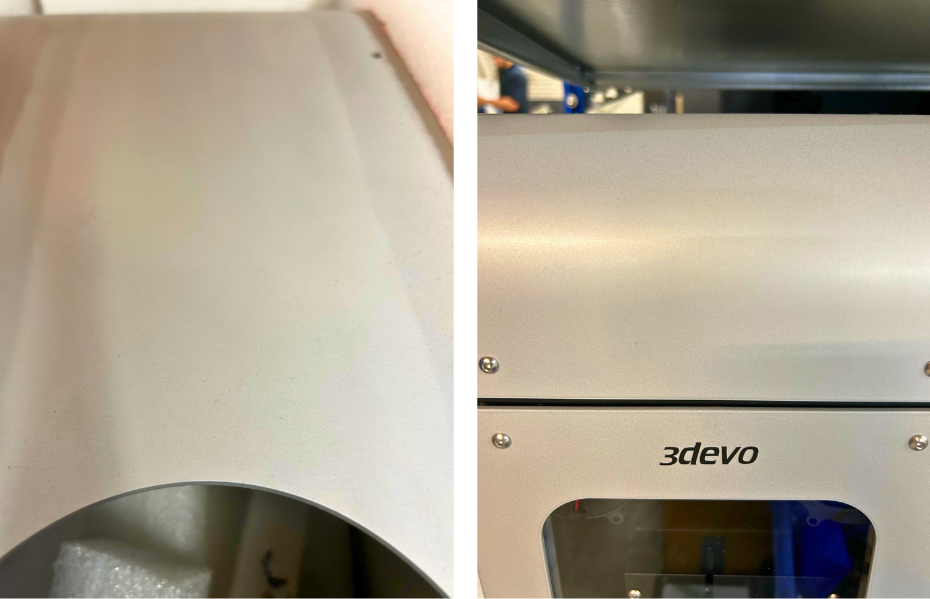
Sometimes, the user might need to remove a panel to troubleshoot an issue. The winder system is essentially a clutch controlling the slipping tension of the spooling process. It was intricately attached to the back panel, making it tedious but through innovative engineering.
We reconfigured it so that it operates detached from the back panel. This gives users easier access to the inside of the Filament Maker and lets us troubleshoot hardware issues more swiftly from a distance.
2018: From black to... black and silver
In 2018, we took a huge step forward. The NEXT 1.0 was divided into 4 versions:
- Filament Maker Precision (350 and 450)
- Filament Maker Composer (350 and 450)
The Precision series was shielded in black panels and equipped with a high-flow screw. Effective and reliable, it was suitable for processing most polymers.
The Composer series was clad in silver panels and came with a mixing screw. Specifically designed for compounding composites. The mixing tip of the screw induced a little bit of turbulence. A small sacrifice in flow stability allowed for a more homogeneous mixing of additives.
The numbers 350 and 450 correspond to the maximum temperature that can be reached with the Filament Maker. The 450 series are meant for processing high-temperature polymers such as PEEK.
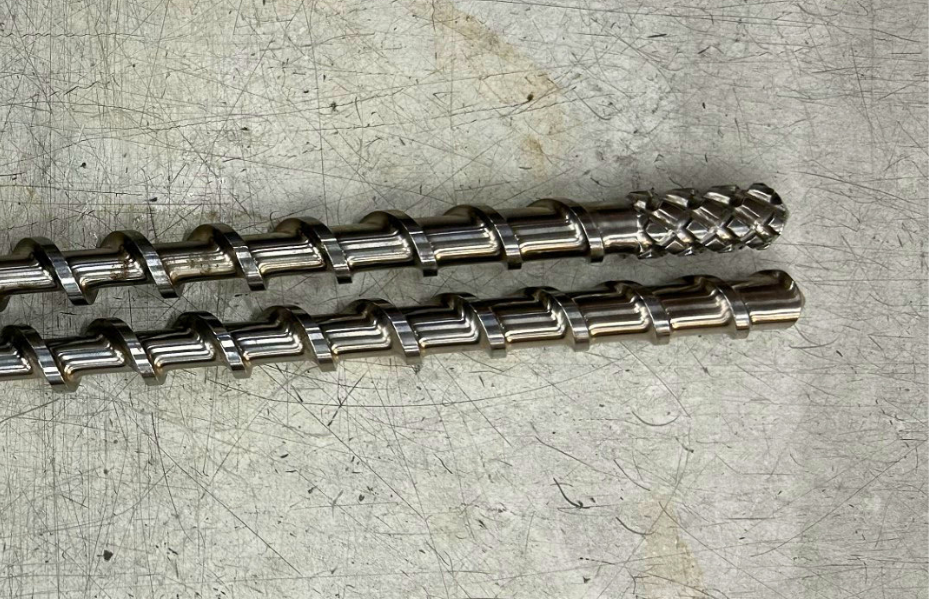
Swapping swiftness
With the creation of the Precision and Composer series, the idea is to offer more specific options for unique. In the spirit of tailoring the device to specific projects and applications, the chassis was redesigned to allow for easier replacements, swaps, and repairs between the different system versions.
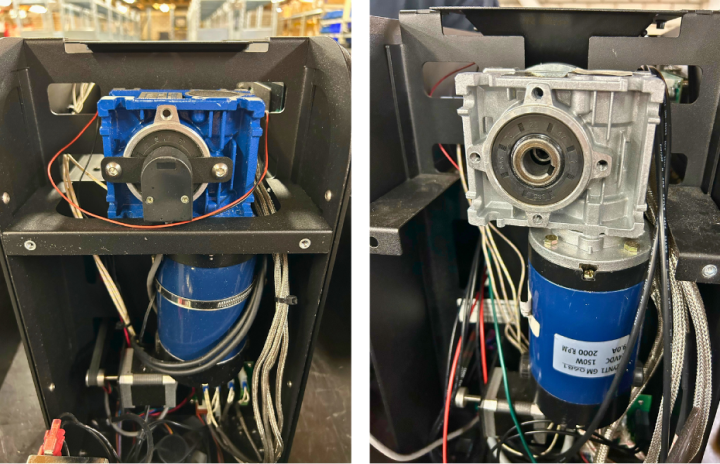
Birth of the Materials Team
We quickly realized that hardware without knowledge does not open many doors. We founded the Materials Team with two intentions:
- Acquiring knowledge about the process, materials, and our own equipment
- Transferring knowledge to our customers
Our team has had different names: Materials Team, 3devo Support, and Customer Success Department... What matters is that we bring the expertise that is required to unlock the machine’s potential. This is what distinguishes 3devo from other companies: we don’t just sell hardware. We enable 3D printing innovation by all means possible.
We started handling numerous support tickets, hosted online webinars, increased the technical knowledge of our Sales Team, and even organized in-person training days, with clients coming from around the world.
Through emails, calls, in-person training programs, YouTube videos, and our Support Platform, we teach, we give the tools, and we enable. Today, the Materials Team is officially the Customer Success Department, still growing, and always happy to help.
2020: Boosting recycling projects
Working with shredded flakes comes with a special challenge: feeding. Unlike round pellets, shredded particles tend to be more jagged and rough, grabbing each other and forming cohesive structures in the hopper of the Filament Maker. This can take two forms mainly: ratholing and bridging.
Either way, the result is poor feeding. After several minutes, gravity no longer suffices to force particles down, and the flow stops. Feeding being the origin of the pressure inside the barrel and the starting point of the whole filament-making process, producing stable filament becomes impossible. This issue had to be solved.
In 2020, the Feeder was born, a game changer that makes it easier to feed shredded flakes into the hopper. Its working principles are basic: placed in the hopper, this spider-looking device vibrates every few seconds. It continuously breaks down any cohesive structure formed between particles in the hopper, ensuring stable downward feeding.
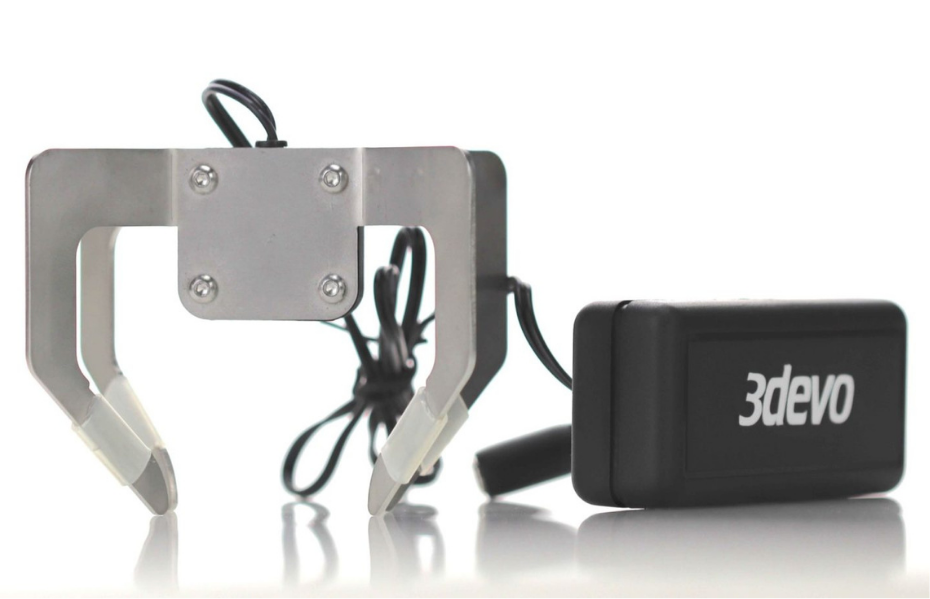
2021: Goodbye nozzle incidents
The nozzle is the most famous spare part of the Filament Maker. It comes in multiple diameters: 2mm, 3mm, and the default 4mm. The nozzle should be changed when damaged, partially clogged, or completely clogged, and for specific materials that don’t withstand the stretching of the puller.
Until 2021, the nozzle was attached to the knee of the Filament Maker thanks to two parts: a compression ring, and a nut. In the event of certain extreme conditions (such as the use of wrong settings), pressure would increase a lot inside the barrel. As a result, there were numerous cases where the nozzle could get pushed out. Even when the compression ring was tightened strongly, the nozzle could sometimes slip and pop out, causing panic.
The most hindered users were specifically innovators trying to push the limits of the technology. Bottlenecking these brave explorers was unacceptable. We heard the feedback, experienced it ourselves, and designed a new nozzle.
Its built-in compression ring made it literally impossible for the nozzle to pop out.
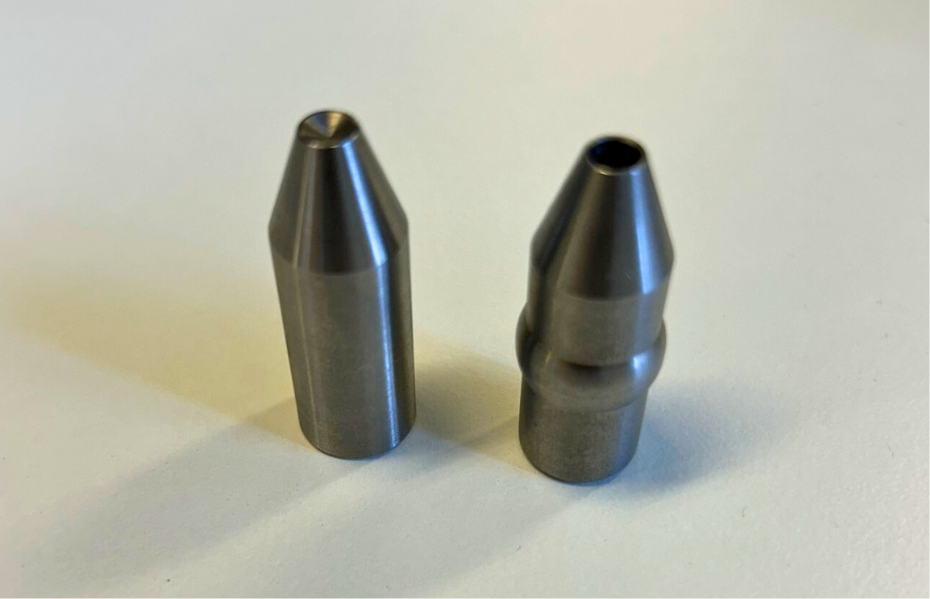
2022: A more forgiving screw design
Again, we know that our clients are innovators who push the boundaries, work with exotic materials, and step into unknown 3D printing territory.
When working with extreme compositions and when adjusting the settings a lot in the research phase, scenarios of high barrel pressure happen. This used to lead to cases where the screw would slide a tiny bit inside the barrel. Backward, by a few millimeters, due to high pressure. As a result, the encoder disk, a super thin fragile part ruling the screw RPM, was get crushed against its sensor.
This made the process unforgiving, as one process mistake could be fatal. We designed a new screw made of two separate parts, giving a tiny bit of room in between for the screw to slide without crashing into the encoder.
This quality-of-life improvement made the process more accessible, and more forgiving, without any downside.
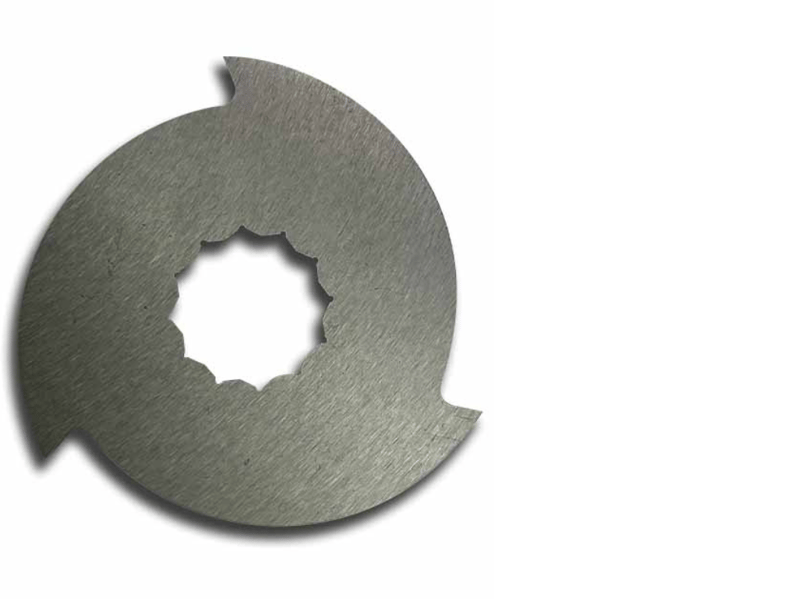
2023: Better hopper
A few high-temperature experiments resulted in paint peeling off from the hopper. The coating would then contaminate the barrel and lower the filament quality. By opting for a bare stainless steel hopper without any powder-coating, we ensured a cleaner process, bidding farewell to paint peeling concerns.
Nothing stands in the way of high-temperature experiments.
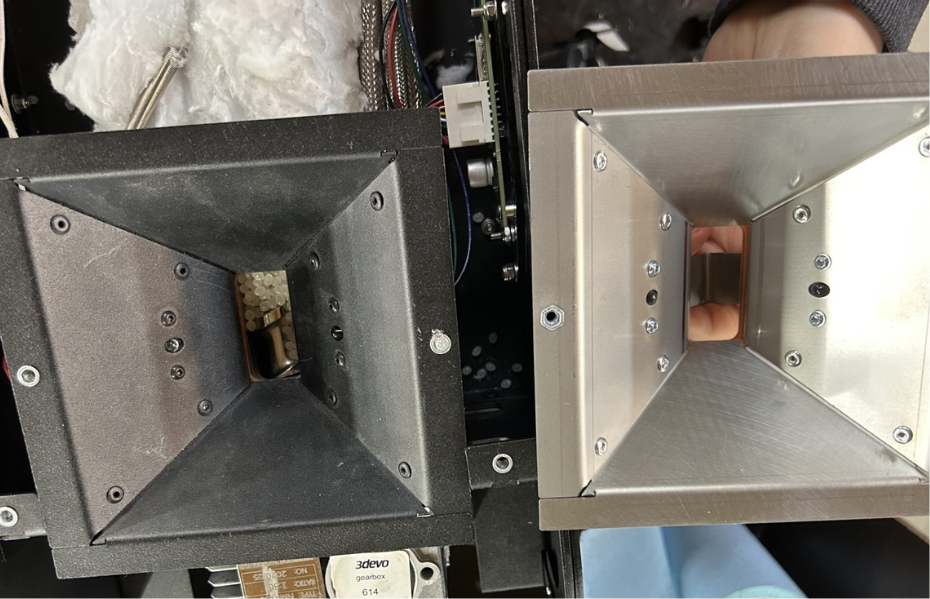
How about the firmware?
You probably noticed that we’ve only covered hardware changes so far in this article. A lot has happened on the firmware side in parallel, with 47 releases since 2016. An average of 7 firmware updates per year, to keep improving the process stability and ease-of-use.
Here are a few notable firmware changes:
2016 – After heating, the screw can now start rotating after a delay, not always immediately. Useful when you want to change the nozzle
2017 – More material presets in the menu, improved heater stability thanks to a smarter control loop, accurate error message for easier diagnostic
2018 – Improved heater stability (especially H4, which is the most subject to quick variations), and firmware ’lockups’ are avoided
2019/2020 – A lot of work was done to ease data logging with our software DevoVision. Since the Filament Maker measures numerous metrics, all the data must be transferred via USB and displayed in a comprehensible way
2021/2022 – Stability improvements to cope with all the hardware design changes, including with older models (NEXT 1.0). Rare, specific scenarios of firmware failure/lockup were fixed for good.
2023 – Without going too in-depth, certain changes, such as memory optimization, facilitate our in-house production of Filament Makers.
The Next Chapter in Our Journey: Introducing the Filament Maker TWO
.png?width=1501&height=1000&name=Banner%20Images%20(6).png)
As we reflect on the evolution of our Filament Makers, we're thrilled to announce the latest breakthrough in our lineup: the Filament Maker TWO Fusion and HighFlow Series. This new addition represents a significant leap in our commitment to innovation, directly influenced by the feedback and needs of our clients. The Filament Maker TWO brings enhanced capabilities in filament production, allowing for more precise, efficient, and diverse material processing right from your desk.
The Filament Maker TWO series is available for order, with shipping set to commence in May 2024. This cutting-edge equipment is not just another product; it's a testament to our dedication to providing tools that empower your creativity and efficiency in 3D printing. Read more about the new Filament Extruder and how the idea started. Order the Filament Maker TWO here and be among the first to experience its advanced features and capabilities.
Conclusion
In closing, our journey with the Filament Maker exemplifies our core values of Openness, Devotion, Courage, and Impact. From its humble beginnings to the sophisticated Filament Maker TWO, each step in our evolution has been driven by a desire to innovate and adapt. Our commitment goes beyond just creating advanced hardware; we strive to empower you, our community of innovators, with knowledge and tools that push the boundaries of 3D printing. As we look ahead, we remain excited about the endless possibilities and invite you to join us in this ongoing adventure. The best, as always, is yet to come.
Our journey in numbers
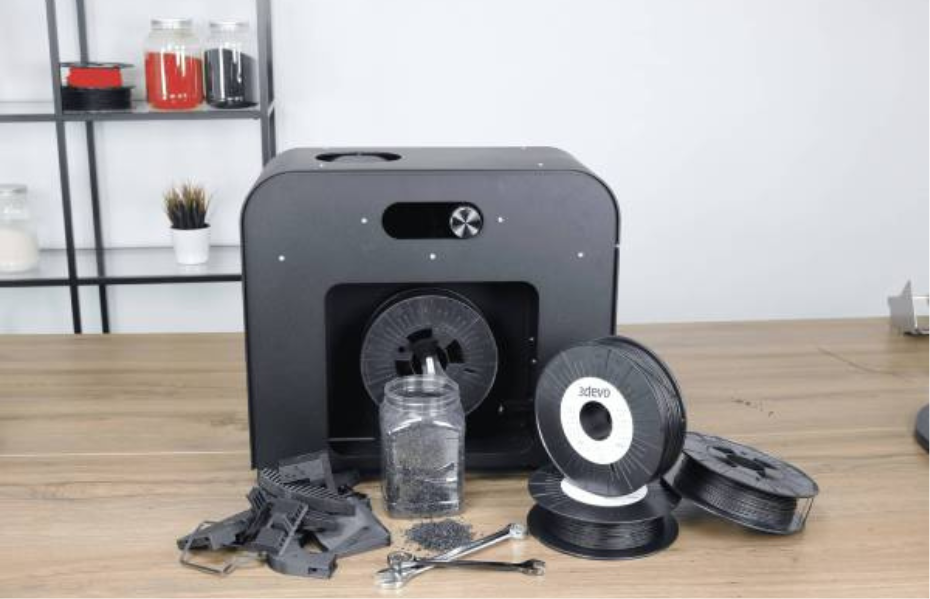
Hours of labwork
7000+
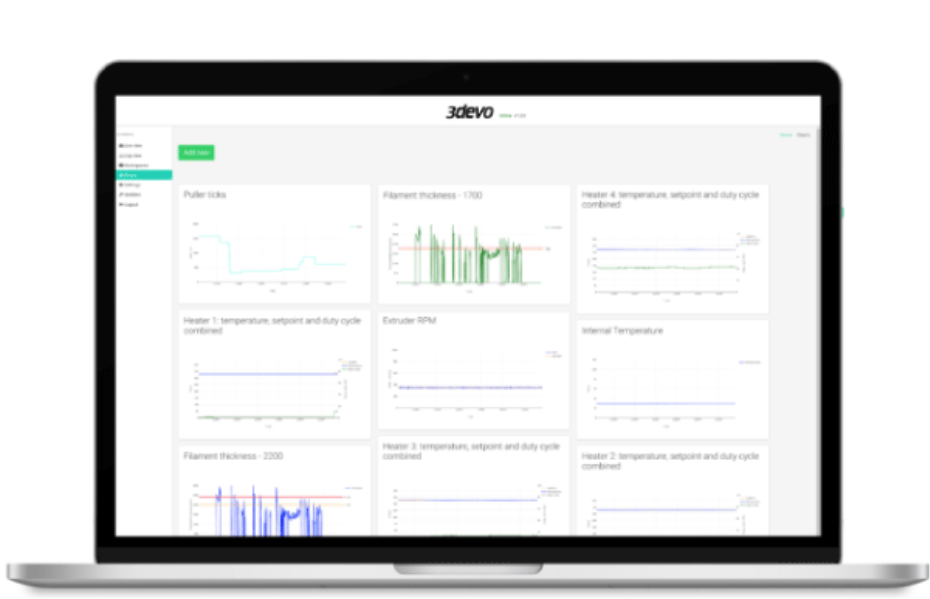
Firmware updates
47
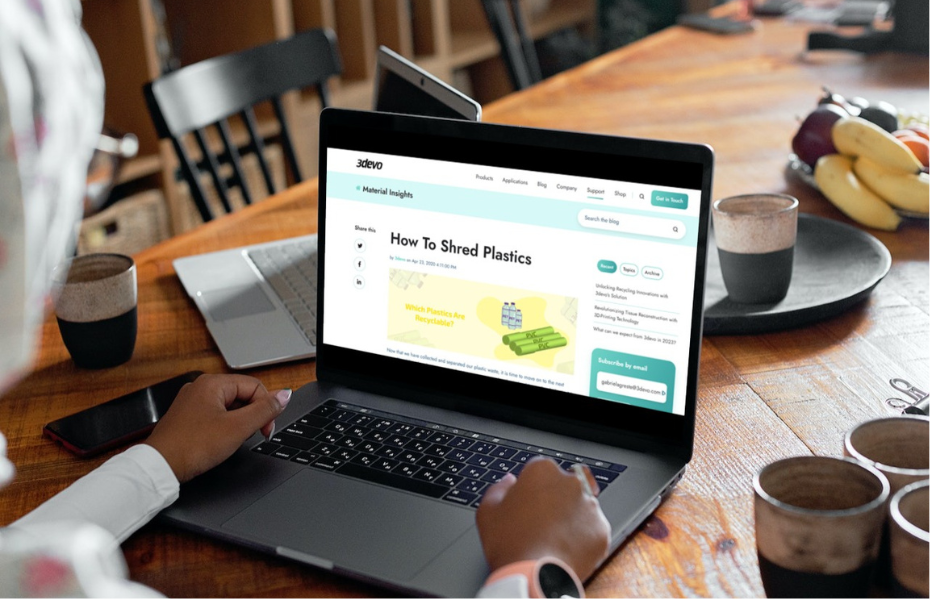
Support emails sent
9000+
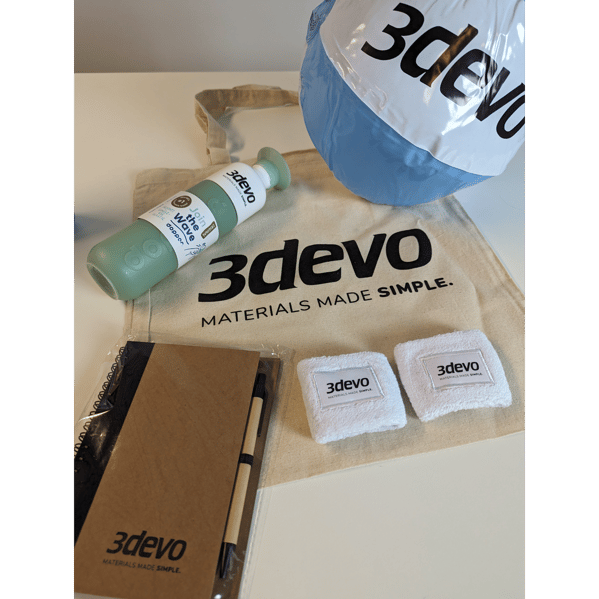
In-person training programs
50+
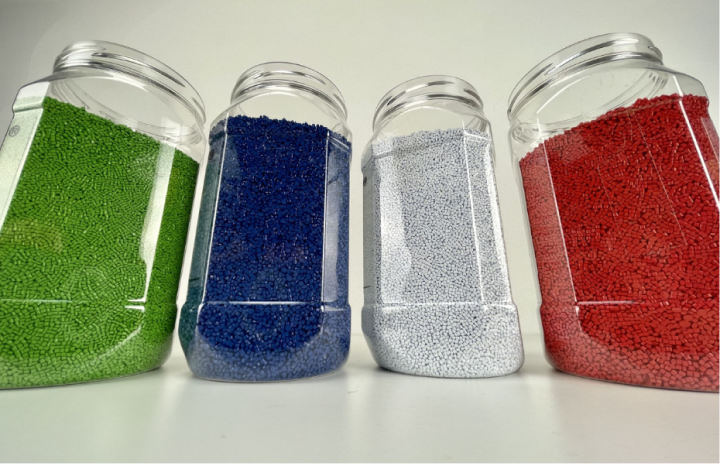
Processed polymers and composites
200+
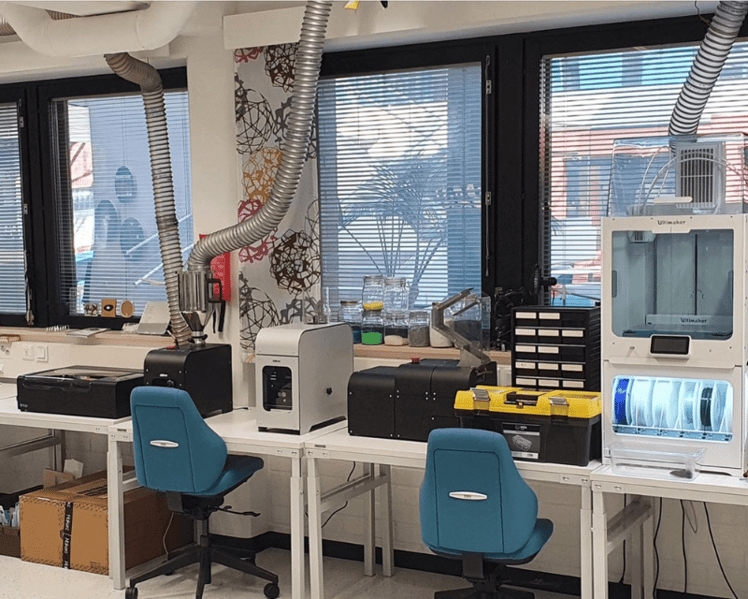
Online training sessions
150+
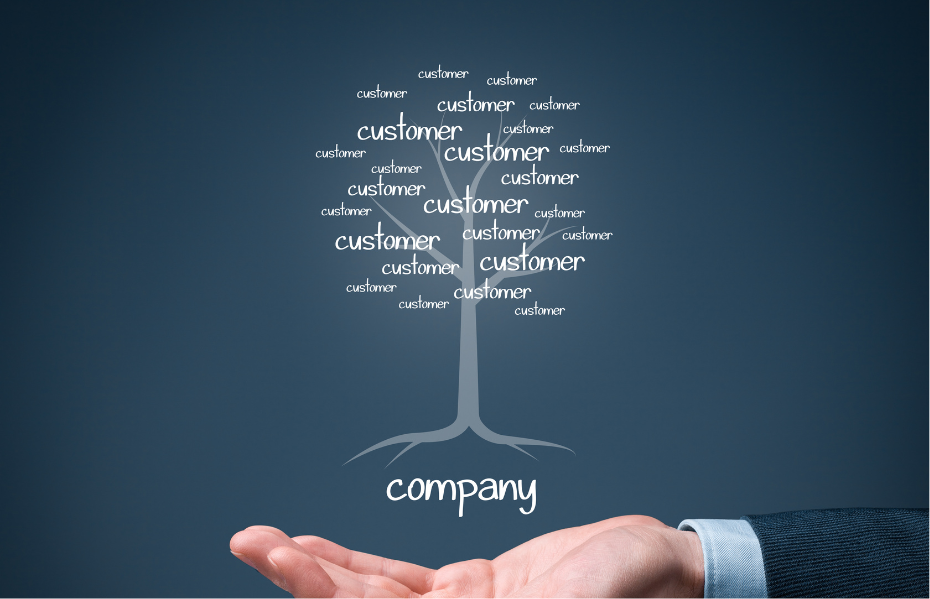
Numbers of customers
1300+
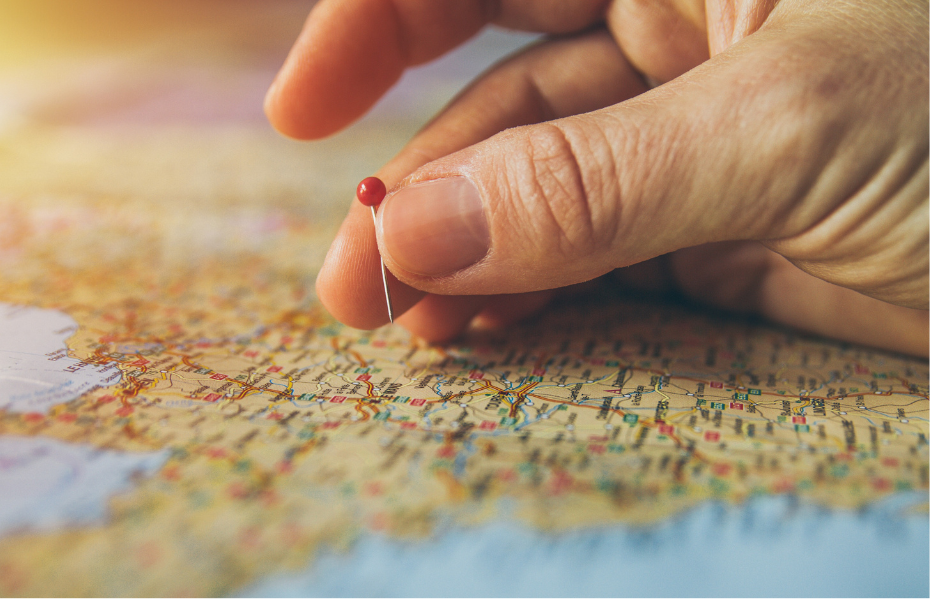
Numbers of countries
120
Curious to learn more about our machines?
Explore our machines for an exciting journey of discovery. With cutting-edge technology and innovative features, we've designed them to meet your needs, whether you're a professional or a hobbyist. Discover their potential and raise your ambitions.
Unlock your potential
Our cutting-edge machines, coupled with our in-depth knowledge of materials, hold the key to unlocking your full potential. Backed by the expertise of our material specialists and extrusion professionals, we offer expert consultations to support you in navigating challenges and making well-informed decisions
Share this
- March 2025 (1)
- January 2025 (1)
- December 2024 (2)
- November 2024 (3)
- October 2024 (4)
- September 2024 (2)
- August 2024 (3)
- July 2024 (6)
- June 2024 (3)
- May 2024 (2)
- April 2024 (1)
- March 2024 (1)
- January 2024 (1)
- November 2023 (2)
- October 2023 (5)
- September 2023 (2)
- August 2023 (1)
- July 2023 (1)
- May 2023 (1)
- December 2022 (3)
- August 2022 (1)
- June 2022 (1)
- May 2022 (2)
- April 2022 (2)
- March 2022 (7)
- February 2022 (2)
- January 2022 (3)
- December 2021 (3)
- November 2021 (3)
- October 2021 (2)
- September 2021 (3)
- August 2021 (3)
- July 2021 (2)
- June 2021 (1)
- March 2021 (1)
- October 2020 (1)
- June 2020 (1)
- May 2020 (1)
- April 2020 (4)
- November 2019 (1)
- July 2019 (2)
- June 2019 (1)
- May 2019 (1)
- March 2019 (1)
- November 2018 (1)
- September 2018 (1)
- January 2018 (1)
- October 2017 (1)
- September 2017 (1)
- July 2017 (1)
- June 2017 (1)
- May 2017 (1)
- January 2017 (1)
- December 2016 (3)
- November 2016 (2)
- October 2016 (1)
- May 2016 (2)
- August 2015 (2)
- July 2015 (1)