Share this
Guide to TPU Plastic: Flexibility with a Twist
by 3devo on Jan 26, 2022 12:31:00 PM
.jpg?width=667&height=500&name=MicrosoftTeams-image%20(62).jpg)
Introduction
In the dynamic world of 3D printing, finding the right materials can make all the difference. Enter Thermoplastic Polyurethane (TPU), a standout polymer that's been garnering attention for its unique blend of flexibility and strength. At 3devo, we've embarked on a journey to unlock the true potential of TPU in the realm of additive manufacturing, exploring ways to turn this promising material into high-quality 3D printing filaments.
Our experiments have led us to create TPU filaments that are not only robust and versatile, marking a significant step forward in the industry. As we walk you through the origins and capabilities of TPU in this blog, we hope to shed light on the transformative role it can play in various sectors. Join us as we delve into the fascinating world of TPU, showcasing how it's shaping the future of 3D printing one layer at a time.
History of TPU
The story of TPU began in 1937, with German chemist Dr. Otto Bayer pioneering the synthesis of this remarkable polymer. TPUs are linear copolymers crafted from a series of alternating hard and soft segments, granting them both rigidity and elastic properties. This beautiful blend of characteristics is achieved through intricate polyaddition reactions involving a variety of reactants.
Over the years, TPU has captivated industries with its fantastic properties, including impressive flexibility, high resistance to abrasion, and an excellent defensive barrier against chemicals. Its mechanical strengths, such as high tensile and impact resistance, make it a favorite in diverse applications.
Characteristics of TPU
.jpg?width=400&height=300&name=MicrosoftTeams-image%20(58).jpg)
TPU has carved a niche for itself in the realm of 3D printing thanks to its unique set of properties. Industries favor TPU due to its rich blend of characteristics that provide versatility and efficiency in various applications. Let’s delve into the core features that make TPU a preferred choice:
Effect of TPU Chemistry on Physical and Mechanical Properties
Altering the reactants and their ratios results in different categories of TPUs, each with a unique set of properties. For example, polyester-based TPUs have greater shore hardness, tensile strength, and tear resistance than polyether-based TPUs. At the same time, polyester-based TPUs also tend to have lower impact strength than polyether-based TPUs. Moreover, polyester-based TPUs are more prone to degradation in the presence of moisture and microbes than polyether-based TPUs.
Polyester-Based Versus Polyether-Based
When venturing into the world of TPU, you’ll predominantly encounter two categories based on soft segment chemistry: polyester-based and polyether-based TPUs. The differences between these two groups are profound and significantly influence their application areas:
Polyester-based TPUs, mainly derived from adipic acid esters, showcase excellent abrasion and chemical resistance, making them particularly suitable where resistance to oils and greases is vital.
Polyether-based TPUs, mostly based on tetrahydrofuran (THF) ethers, excel in low-temperature flexibility and microbial resistance, becoming the material of choice for applications demanding excellent hydrolysis resistance or significant flexibility under extremely low temperatures.
Abrasion and Scratch Resistance
In environments where abrasion resistance is critical, TPU shines through as a preferred material. Its high resistance to wear and tear ensures not only durability but also maintains the aesthetic appeal of the finished product. Key sectors leveraging TPU’s superior abrasion resistance include the automotive industry (specifically for interior parts), sports and leisure equipment manufacturing, and creating technical parts and specialty cables. When pitted against other thermoplastics, TPU often exhibits superior results, safeguarding its prominence in various applications.
Key Properties of TPU
-
High Elongation and Tensile Strength: TPU boasts significant elongation and tensile strength, standing as a resilient option for various applications.
-
Low-Temperature Performance: Unlike other materials, TPU maintains its properties even in low temperatures, providing versatility across different environments.
-
Rubber-like Elasticity Coupled with Excellent Mechanical Properties: TPU combines the best of both worlds - the strength of plastics and the flexibility of rubber, making it a dynamic choice for various manufacturing endeavors.
-
High Transparency: TPU materials often exhibit high levels of transparency, making them a choice material in applications where visual appeal is a priority.
-
Good Resistance to Oils and Greases: TPU stands resilient against oils and greases, further amplifying its usage in various industrial settings.
TPU's Special Offering to 3D Printing
TPU has carved out a special place in the realm of 3D printing thanks to its unique combination of strength and flexibility. Its crystalline regions provide mechanical strength, while the elastic areas offer bendability, a feature not commonly found in other 3D printing materials. Moreover, TPU showcases high chemical resistance, excelling at the temperature ranges generally used in 3D printing.
To provide a deeper understanding, here’s a comparative glimpse of TPU with other popular 3D printing materials:
Special Types of TPUs
Aliphatic TPU
For projects where maintaining a stable light color and preventing yellowing over time are essential, aliphatic TPUs come to the rescue. These TPUs, based on aliphatic isocyanates, offer excellent non-yellowing performance, ensuring the aesthetic longevity of the products.
Green Initiatives in TPU Production
In the spirit of fostering environmental sustainability, several companies have spearheaded the development of plant-based bio TPUs. Companies like BASF, Merquinsa-Lubrizol, and GRECO have introduced green thermoplastic elastomer alternatives to the market, known as Elastollan N, Pearlthane ECO, and Isothane, respectively. These innovations signify a significant stride towards a greener, more sustainable future in the 3D printing industry.
.jpg?width=400&height=300&name=MicrosoftTeams-image%20(59).jpg)
TPU Filament Extrusion
Regarding the extrusion process of TPU filament, it's essential to delve deep into the various facets that make it a standout material. TPU, a block copolymer of hard and soft segments, excels due to its dynamic mechanical properties. The hard segments grant it rigidity, while the soft segments confer elasticity. It's vital to understand that TPU can have varied behaviors depending on its specific grade; hence, selecting the right kind of TPU is crucial for successful extrusion.
Extrusion Techniques
In the extrusion process, particular attention should be given to the temperature settings, which generally range between 180-220°C. The accurate temperature ensures a smoother surface finish and a consistent diameter, thus facilitating better post-processing. Moreover, additives like fiberglass can be mixed during the extrusion to enhance the filament's properties.
3devo's Expertise
At 3devo, we extend our expertise to innovators keen to explore the vast potential of TPU. Through detailed consultations and project roadmaps, we empower our clients to venture into TPU filament extrusion with confidence, offering insights and solutions that pave the way for successful project outcomes. During the drying phase, avoid the pellets sticking together by ensuring the calibration is accurate, with a recommended drying time of 2-4 hours at 90-100°C. The filament must be purged at medium temperatures (around 220°C) to prevent any material degradation.
Ready to make your own TPU Filament?
Our Filament Extruder is designed to be your sidekick in this adventure, enabling you to experiment and create small batches of top-quality TPU filaments.
%20(1).png?width=600&height=480&name=silver-extruder-1%20-%20instasize%20(1)%20(1).png)
Challenges and Solutions
Despite the numerous benefits, TPU extrusion does come with its own set of challenges. The operation window can be relatively small, requiring careful adjustment of processing settings. 3devo functions as an extension of your team, assisting in navigating these challenges with ease and efficiency, ensuring the production of high-quality TPU filament.
3D Printing with TPU
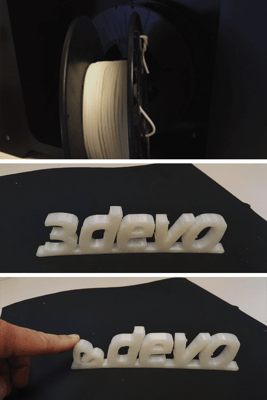
Applications
TPU finds an extensive array of applications owing to its transparency and mechanical strength. In the automotive sector, it is used in making components like dashboards and door panels. The medical field utilizes TPU in making implants and prosthetics due to its flexibility and chemical resistance.
Equipment Setup
Fused Deposition Modeling (FDM) 3D printers are generally well-suited for handling TPU. A heated bed, with a temperature around 60°C, helps in avoiding warping and ensures better adhesion during the printing process. Utilizing a direct drive extruder can significantly enhance the handling of TPU's flexible nature.
Printing Parameters
When 3D printing with TPU, maintaining a slow print speed, around 15-30mm/s, ensures higher accuracy and a better surface finish. Retraction settings should be fine-tuned to prevent stringing, which is a common issue while printing with flexible filaments.
Post-Processing
Post-processing TPU prints can involve a range of techniques. While TPU doesn't readily respond to techniques like acetone smoothing, mechanical post-processing, such as sanding, can help achieve a smoother finish. It's also possible to use secondary operations like gluing or welding to combine TPU parts.
Sustainability and TPU
Recycling and Reusing TPU
In a rapidly evolving industry, the recycling and reusing of TPU materials are becoming increasingly significant. It's not only a pathway to reducing waste but also to fostering more cost-effective and environmentally conscious manufacturing processes. Here are some examples where TPU recycling is making a tangible difference:
-
Footwear Industry: Companies like Adidas are taking steps to recycle TPU materials. In their initiative, they recycle TPU-based footwear to create new shoes, thus minimizing waste and promoting a circular economy.
-
Automotive Sector: In the automotive sector, manufacturers are exploring the possibilities of recycling TPU components from end-of-life vehicles to create new automobile parts, contributing to sustainable production cycles.
-
Medical Field: The medical field is also witnessing an increasing trend where TPU waste generated from medical implants and other products are recycled to create new medical-grade materials, reducing the environmental footprint of healthcare operations.
-
Educational Initiatives: Several educational institutions are engaging in projects where students and researchers are encouraged to experiment with recycling TPU materials to create new products, fostering a culture of innovation and sustainability.
-
Community Workshops and Labs: In various community workshops and public institution labs, individuals are encouraged to bring in their TPU waste for recycling. These facilities, equipped with tools like the Filament Maker and GP20 Plastic Shredder offered by 3devo, transform small batches of TPU waste into fresh filaments, ready for new creations.
By promoting TPU recycling, 3devo stands at the forefront of these initiatives, offering solutions that enable innovators and creators to recycle thermoplastic waste into new, viable filaments for 3D printing, thus playing a crucial role in shaping a sustainable future in the 3D printing industry.
Conclusion
In conclusion, TPU is a beacon of innovation in the 3D printing landscape, marrying flexibility with durability to foster a new realm of possibilities. As we navigate through the evolving terrains of technology, it's materials like TPU that hold the promise of a sustainable and adaptive future. Whether you're an industry leader looking for the next big opportunity or an academic entity aiming to break new ground, TPU offers a gateway to unprecedented advancements. At 3devo, we are here to walk this path of discovery with you, catalyzing change and fostering a culture of creativity and sustainability. Let's venture into the future with TPU leading the way.
FAQ
TPU is popular due to its unique blend of strength and flexibility. It combines high tensile strength and superior tear and abrasion resistance with excellent ductility, making it versatile for various applications. It can maintain its properties even in low temperatures and offers resistance to oils and greases, making it a resilient choice for different environments.
One special type of TPU is aliphatic TPU, which maintains a stable light color and prevents yellowing over time, ensuring the aesthetic longevity of the products. Companies are also developing plant-based bio TPUs as a part of green initiatives in TPU production, offering more sustainable alternatives in the 3D printing industry.
Yes, TPU can be blended with various additives or fillers to modify its properties. For instance, adding glass fibers can enhance its rigidity, while incorporating UV stabilizers can improve its resistance to UV radiation. It's vital to conduct tests to determine the optimal combination of additives for achieving the desired properties.
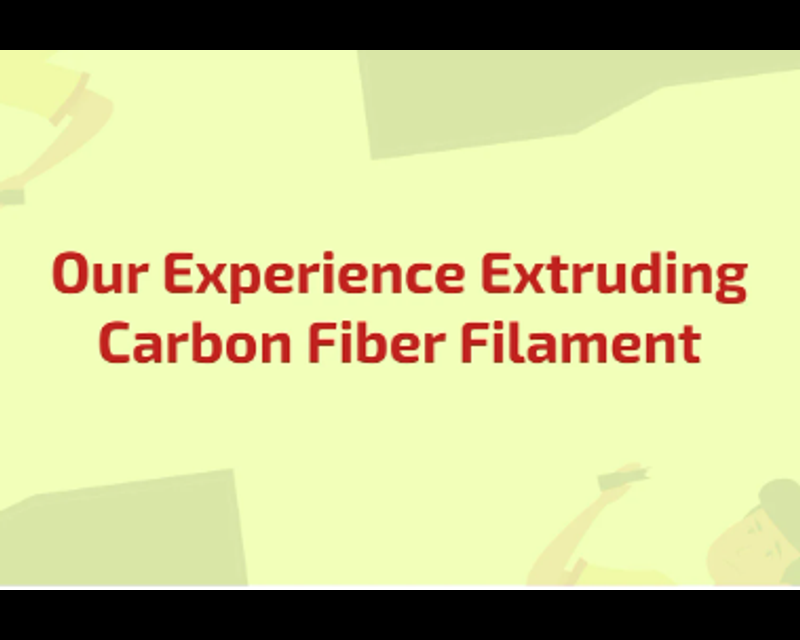
Dive Deeper into Carbon Fiber Extrusion
Ready to embark on your carbon fiber filament journey? Discover valuable insights and guidance from our recent exploration into the realm of carbon fiber filament extrusion.
%20-%20instasize%20(1)%20-%20instasize%20(1).png?width=800&height=640&name=PETG-e1494958102567%20(1)%20-%20instasize%20(1)%20-%20instasize%20(1).png)
Unlock the Secrets to Material Selection
Dive into our Complete Material Selection Guide to find your perfect fit hassle-free. Get started with your innovation journey here!
%20-%20instasize%20(2).png?width=800&height=640&name=MicrosoftTeams-image%20(39)%20-%20instasize%20(2).png)
Navigate the World of Polymers with Expert Guidance
Ready to elevate your project with the perfect material? Our Polymer Pyramid is designed to help you pinpoint the right polymer with ease.
Share this
- March 2025 (1)
- January 2025 (1)
- December 2024 (2)
- November 2024 (3)
- October 2024 (4)
- September 2024 (2)
- August 2024 (3)
- July 2024 (6)
- June 2024 (3)
- May 2024 (2)
- April 2024 (1)
- March 2024 (1)
- January 2024 (1)
- November 2023 (2)
- October 2023 (5)
- September 2023 (2)
- August 2023 (1)
- July 2023 (1)
- May 2023 (1)
- December 2022 (3)
- August 2022 (1)
- June 2022 (1)
- May 2022 (2)
- April 2022 (2)
- March 2022 (7)
- February 2022 (2)
- January 2022 (3)
- December 2021 (3)
- November 2021 (3)
- October 2021 (2)
- September 2021 (3)
- August 2021 (3)
- July 2021 (2)
- June 2021 (1)
- March 2021 (1)
- October 2020 (1)
- June 2020 (1)
- May 2020 (1)
- April 2020 (4)
- November 2019 (1)
- July 2019 (2)
- June 2019 (1)
- May 2019 (1)
- March 2019 (1)
- November 2018 (1)
- September 2018 (1)
- January 2018 (1)
- October 2017 (1)
- September 2017 (1)
- July 2017 (1)
- June 2017 (1)
- May 2017 (1)
- January 2017 (1)
- December 2016 (3)
- November 2016 (2)
- October 2016 (1)
- May 2016 (2)
- August 2015 (2)
- July 2015 (1)